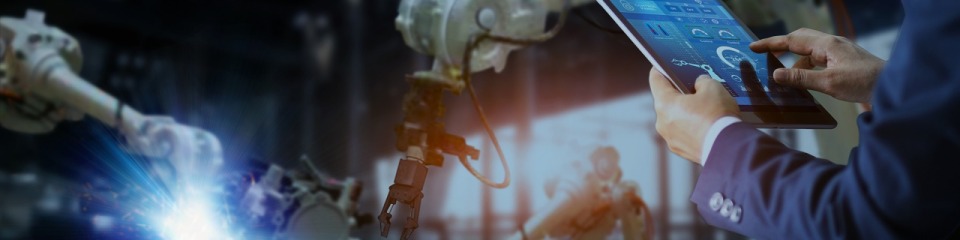
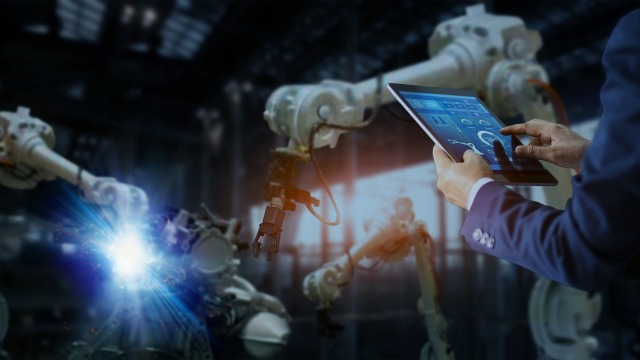
Por que um sistema de controle de soldagem precisa da capacidade da Indústria 4.0? A soldagem produz verdadeiros tesouros na forma de vastas quantidades de dados que servem como base de otimização de processos, machine learning e criação de valor. No entanto, com esse objetivo, primeiro é necessário coletar, analisar e processar os dados. Os padrões comuns de acesso a esses dados são os protocolos MQTT e OPC UA. A Bosch Rexroth combina esses dois tipos de comunicação no pacote “Conector IoT". Isso possibilita que os usuários processem os dados coletados de acordo com suas necessidades e, por exemplo, implementem registros automáticos de controle de qualidade.
O controle de soldagem PRC7000 pode ser facilmente preparado para a Indústria 4.0 com o pacote “Conector IoT", que combina os dois tipos de comunicação, MQTT e OPC UA.
O sistema de controle funciona simultaneamente como um dispositivo de processo e como um gateway de comunicação. O conector IoT disponibiliza os dados para processamento adicional, por exemplo, para avaliações estatísticas ou para registro permanente. Os objetivos incluem economia no gerenciamento de qualidade e em manutenção preventiva. Essas prioridades são cada vez mais importantes na soldagem por resistência, por exemplo, na indústria automotiva de construção de corpo, na área de fornecedores TIER1 e na engenharia mecânica.
Ambos tipos de comunicação são os principais em seus setores: o MQTT como um protocolo de rede aberto e o OPC UA como um padrão de comunicação na automação.
O MQTT é projetado para ambientes de baixa largura de banda e alta latência. Ele é adequado idealmente para o envio de grandes quantidades de dados em pacotes. Por exemplo, um sistema de controle armazena e envia até 30.000 pontos de soldagem por dia. O controle PRC7000 envia os dados no formato JSON – um formato autodescritivo baseado em texto que pode ser interpretado por seres humanos.
O OPC UA tem a capacidade de transportar dados de máquina e também de descrevê-los semanticamente em um formato legível pela máquina. Dessa maneira, é possível enviar dados à nuvem e analisá-los, e os resultados são gravados de volta no sistema de controle. Isso compõe a base das aplicações que abordam machine learning e inteligência artificial (IA).
Ambos padrões estão disponíveis no Conector IoT. A funcionalidade básica do sistema de controle de soldagem PRC7000 inclui um editor MQTT e um Servidor OPC UA por padrão. É possível ampliar o escopo dos dados com uma licença, que disponibiliza ainda mais aplicações em potencial.
Os sistemas de controle de soldagem anteriores não foram desenvolvidos para a implementação de protocolos como o MQTT e o OPC UA, devido ao desempenho insuficiente. Em vez disso, era necessário conectar um software de middleware ou de gateway entre o dispositivo e o limite ou a camada de nuvem, que pode exigir hardware próprio. Os dados eram coletados, agregados e enviados pelo middleware.
O conector IoT é compatível com integração vertical a partir do dispositivo de processo, por exemplo, à nuvem ou ao limite. Sendo um sistema aberto, ele não está sujeito a estruturas proprietárias e oferece comunicação de última geração. Os usuários podem processar os dados de acordo com suas necessidades. Com o controle PRC7000, um escopo de dados definido – por exemplo, para avaliação iO/niO – é incluído por padrão.
O pacote de expansão possibilita um fluxo de dados ainda mais amplo e, portanto, casos de uso adicionais. Por exemplo, é possível usar o conector IoT para determinar mais de 200 valores reais por ponto de soldagem. Estão inclusos valores de qualidade, dados não processados de curvas de soldagem, vários parâmetros, como pontos de ajuste, configurações e curvas de referência, além de alterações de dados. Em combinação com a avaliação de outras fontes de dados, é possível implementar conceitos de manutenção preventiva. Benefícios adicionais garantem a transparência, possibilitando que os usuários identifiquem e façam uso do potencial de otimização: registro automático pode ser implementado para fins de controle de qualidade, as alterações dos parâmetros registrados possibilitam análises da qualidade da soldagem a ponto, e é possível visualizar os status na oficina por meio das informações de parâmetros.
A indústria de hoje demanda uma produção flexível e versátil que responda às mudanças dinâmicas dos requisitos. Para atender a essas demandas, são necessárias soluções adaptáveis que sejam compatíveis com funcionamento em rede e que garantam consistência. A Bosch Rexroth está respondendo às necessidades da fábrica moderna com o Conector IoT. Ele possibilita que os controles de soldagem PRC7000 e PSI6000 da Bosch Rexroth sejam expandidos para atender aos requisitos da Indústria 4.0 e para coletar uma riqueza de dados.
Conheça o sistema de controle de tecnologia de solda da nova geração PRC7000.