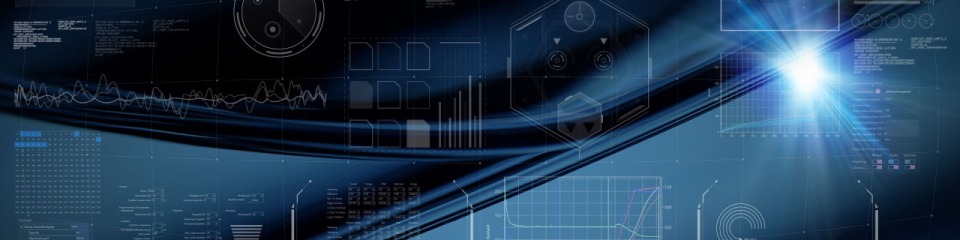
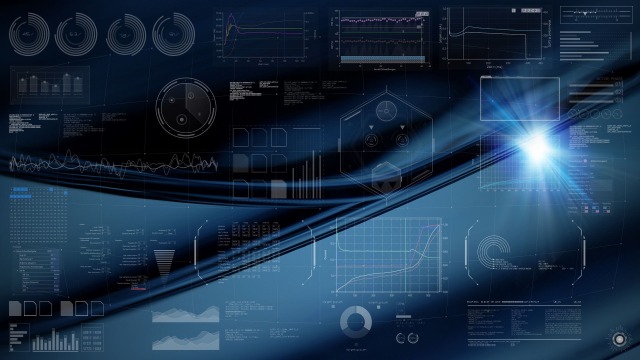
A vehicle is to be produced in four variants – on eight production lines in six plants around the world. This means over 120,000 welding spots whose parameters need to be determined, entered, optimized and validated. This example shows how high the demands are in resistance spot welding. And things are becoming increasingly complex: With persistent trends such as lightweight construction, new challenges as regards process stability and productivity will be seen all the time. A welding control system which adapts quickly and dynamically to material combinations for example is needed here.
320 parts, 80 different types of metal sheeting and coatings in various thicknesses – this results in 500 combinations of materials and thicknesses joined together with 5,000 welding spots. This is a typical vehicle body nowadays. And the demands are growing all the time. After all, the trend in vehicle construction is towards increasingly lightweight, safer vehicles. One reason for this is the fact that lower weight reduces fuel consumption and thus CO2 emissions. The vehicle manufacturer also uses less material which leads to reduced production costs. At the same time, the design forms are becoming increasingly complex and the requirements as regards crash safety must be met.
Owing to combinations of different materials, the number of demanding welding tasks continues to grow. In the automotive sector, more and more vehicle types and models are being produced on the same production line. This all directly influences commissioning as well as the requirements as regards welding control and monitoring.
In order for the required lightweight designs to be achieved, the use of high-strength steel materials with anti-corrosion coatings has constantly increased in vehicle construction in recent years. Using high-strength steels, components can be designed with thinner walls yet with the same mechanical properties. However, these materials are usually more likely to crack during resistance spot welding.
Another challenge lies in joining aluminum and steel using resistance spot welding owing to their extreme physical properties. Steel has a high electrical resistance, while aluminum has a low resistance. The new, high-performance PRC7000 welding control system from Bosch Rexroth can cope with both of these extremes. Transformers convert the output power of the welding control system precisely to suit the welding task in hand.
With the PRC7000, different sheet thickness and material combinations – from steel to aluminum – can easily be processed. To make this possible, the new welding control system uses adaptive controllers and flexible programmability. It also makes perfect welding spots reproducible.
For the first time ever, one leading automotive manufacturer used resistance spot welding to join large numbers of aluminum parts to the chassis of a new vehicle. In this case, the main body is made from aluminum and involves approx. 2,000 welding spots with different aluminum sheet combinations.
With the newest version of the PRC7000, the gun data modules for example allow process signals to be digitalized on the gun itself. Manual guns can be operated with all available controls systems without having to parameterize the control system again. The data are stored in the gun data module as a complete welding task and can then be transmitted to the control system with reduced interference. This allows greater freedom for users as well as new use case and cost savings.
With the PRC7000 welding control system, automotive manufacturers can meet the highly dynamic requirements of resistance spot welding efficiently, flexibly and in accordance with the very highest quality standards. Not only economy, process stability and productivity are guaranteed – competitiveness is too.