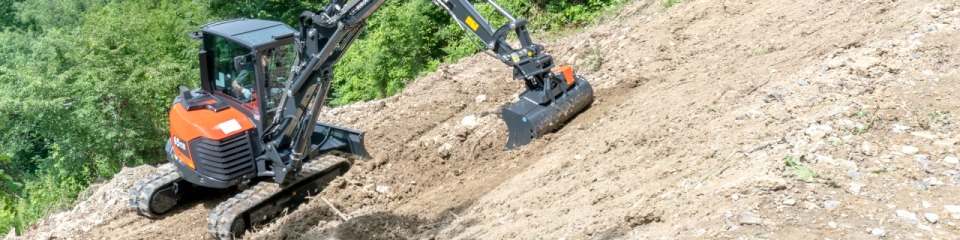
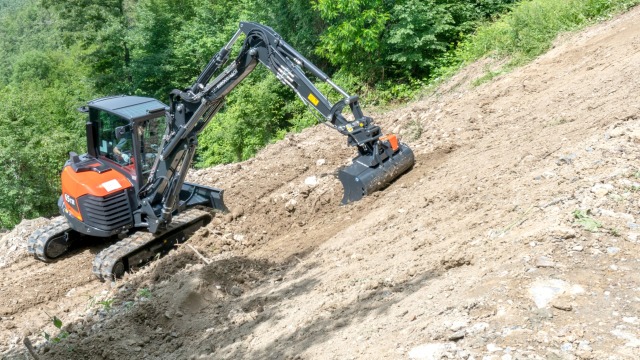
Mini excavators and compact wheel loaders of the Eurocomach brand work even more maneuverably, flexibly and productively with the electronic Open Circuit architecture from Bosch Rexroth. The combination of electrohydraulic pump control and software reduces not only fuel consumption but also overall costs from engineering to service.
Compact off-highway machines should be as maneuverable, versatile and energy-efficient as possible. A decisive key to this lies in the electronification of the working hydraulics. The fact that improvements in this respect can be combined with sustainable standardization effects is demonstrated by the new mini-excavators, wheel loaders and track loaders from the Eurocomach brand, which has been part of the Italian Sampierana Group for almost 30 years.
Faced with a growing market demand for ever greater flexibility, efficiency and productivity, Sampierana first launched the electronification of its working hydraulics on its six-ton mini-excavators. "Our compact construction machines are used for a wide variety of jobs, explains Giuseppe Fabbri, Technical Manager at Sampierana. "Loading, excavating or digging should be very accurate or quick and productive to perform, as needed, and also support a wide range of tools - from shovels to hammers or mowers." Conventional work hydraulics have stood in the way of this development because their rigidity always forces compromises on manufacturers. Because it used to be necessary to specify in advance whether the hydraulic pump was to be controlled by pressure, torque or swivel angle, it was not possible to optimize energy efficiency, flexibility and productivity in equal measure. Once parameters have been defined on the hardware side, they remain unchanged over the entire service life.
Higher efficiency, better dynamics, individual behavior: With electronic Open Circuit (eOC), machine control, operating feel and dynamics together with other parameters can be set and changed according to the situation.
Sampierana found a way out of the previous design corset with the eOC electronic open circuit architecture from Bosch Rexroth. Its central component is an electrohydraulic axial piston pump operating in an open circuit with a swivel angle sensor and pressure sensors. The eOC pump is electronically controlled in a closed loop so that the required setpoints for torque, pressure or volume flow can be controlled independently of each other precisely and highly dynamically in the range of milliseconds. Using the associated BODAS eOC software, parameters such as dynamics and power control can be individually set, changed and combined during operation. The control software communicates via the CAN bus and can be installed either on a BODAS eOC controller from Bosch Rexroth or on a controller from a third-party manufacturer.
Compact electronification: the electronic Open Circuit (eOC) architecture from Bosch Rexroth, consisting of eOC pump, electrohydraulic control block with load-holding valves, and BODAS control unit with eOC software.
The electrohydraulic pressure and volume flow software (EHpQ) controls the volume flow and the pressure independently of each other. This allows all known machine parameters to be freely adjusted according to operating mode and operator preference.
For machine optimization, the eOC pumps offer Sampierana a wide range of hydromechanical control functions and mechanical interfaces. They are all transferred directly to the control software, which provides Eurocomach engineers with the following control modes: Pressure or delta pressure control, flow rate and swivel angle control, and torque control. All three control modes each have a predefined set of parameters for optimal behavior of the eOC pump in the hydraulic system, such as load sensing. Since the BODAS eOC software continuously adapts the hydraulic power to the available engine torque and also compensates for disturbances in the load cycles of the machine, highly dynamic and highly precise work functions become possible. The overall productivity of the working machine increases while the energy consumption of the entire hydraulic system decreases in favor of fuel consumption and battery usage.
In a first project, Sampierana used the eOC architecture to develop the 60ZT and 65 TR mini excavators. While the 60 ZT has a zero radius profile with a monolithic boom, the 65T is equipped with a triple boom, which is particularly suitable for digging, handling and loading operations thanks to its small radius. Both models feature high performance and versatility thanks to eOC. While the low-noise axial piston variable displacement pump type A10VO realizes precise performance control, the compact RS12/EH control block ensures flow sharing (LUDV) and, with low pressure losses, in turn contributes to equally high-performance and energy-efficient working hydraulics.
Together with the open and scalable BODAS eOC pump control RC5-6/40 and the BODAS eOC software, the dynamic behavior and productivity of the machine can be specifically optimized, with the operator interacting directly with the machine's electronics via joystick and onboard display. Thanks to the situation-dependent modification of functional parameters such as delta-P, pressure gradient or volume flow, the mini excavators can choose to work slowly and precisely on the construction site or move larger quantities of earth at a rapid pace.
Engineering also gains flexibility and efficiency with the new electrohydraulic solution from Bosch Rexroth. "Since all control functions are transferred from the hydromechanical controller to the software, the entire range of functions and variability of the pumps is available to our customers," clarifies Simon Dreher, Sales and Industry Management Mining Excavators and Construction Machinery. In addition, the scalable solution allows manufacturers a step-by-step implementation, according to the Rexroth expert. For example, manufacturers can start with the electrohydraulic eOC pump and then expand the solution to the electrohydraulic main control block or the entire hydraulic system. Depending on requirements, the implementation can be realized with hard-coded individual parameters as well as with a whole range of adjustable digital CAN bus parameters.
Base technology for different applications, drive motor technologies and functions: With the BODAS eOC system, OEMs can determine the scope of electronic control themselves - from the pump to Advanced Assistance Functions (AAF) to the entire system.
With the help of the eOC BODAS pump control, Sampierana has managed to increase the range of working modes and tools while increasing machine performance. "The working hydraulics can be precisely controlled with short response times," reports Giuseppe Fabbri. "At the same time, we can configure the system parameters very easily. We secure these advantages in the long term because the eOC BODAS system is designed to be open and scalable."
Sampierana can also point to improvements in terms of sustainability. On the one hand, less control oil is required because several hydromechanical controller axes for pressure, flow rate and torque have been combined into one. On the other hand, the dynamic adjustment of the control parameters minimizes the energy consumption of the entire hydraulic system. "On this basis, we can comply more easily with current regulations regarding ecomobility, emissions and efficiency and support our customers even better in meeting their climate protection targets," explains Giuseppe Fabbri. "This is an important competitive factor."
As a result of the reduced pump variance, Sampierana also reduces the administrative effort from development to assembly and logistics to service, including spare parts management and aftermarket. Feature updates and trouble shooting are efficiently carried out via the BODAS Service Tool, which among other things also includes a detailed guide to pump commissioning.
The electronification of working hydraulics at Eurocomach makes clear the extent to which compact work machines can gain in flexibility, efficiency and productivity when complexity is shifted from hardware to software. "Thanks to eOC BODAS, we can now map a wide range of functions with a consistent hydraulic system and adapt it precisely to the type of work to be performed and the operator's preferences," sums up Giuseppe Fabbri. "While we delight our customers on the job site, we benefit internally from leaner processes and high degrees of freedom for the coming generations of vehicles." In view of the good results, Sampierana is extending the Bosch Rexroth eOC system to other Euromach models.
Get first hand impressions about the collaboration between Sampierana and Bosch Rexroth