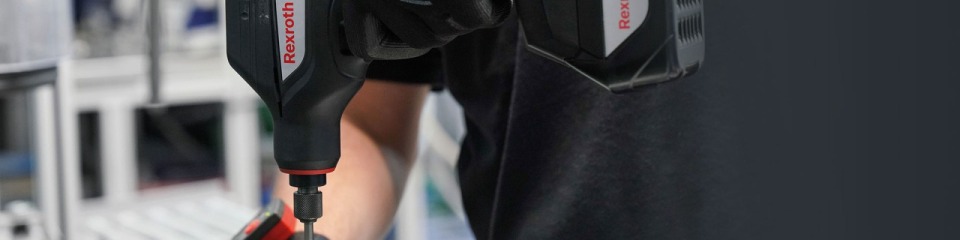
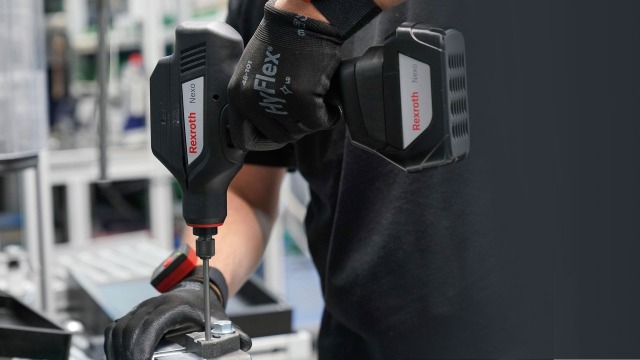
One of the more promising breakthroughs associated with the introduction of Connected Industry to industrial production settings is the innovation coming from decentralized intelligence in manufacturing. It offers industrial companies the opportunity to transform their manufacturing facilities from a static into a highly flexible production system.
Shorter product cycles as well as shorter response times can be realized by implementing mobile facility modules. Combined with intelligent, cordless tightening tools decisive advantages as higher flexibility and productivity can be achieved especially in respect of the challenges proceeding from volatile markets. This article will discuss how intelligent battery tools as the Bosch Rexroth Nexo wireless nutrunner enable a versatile, highly efficient production in tightening applications.
In the old days, automation systems were designed top down with a centralized intelligence that controlled every production machine downstream. Typically, such a system consisted of line PLCs on the top communicating with station PLCs and those in turn communicating with the individual production machines. In the case of tightening systems these machines then consisted of tightening controllers that directed and collected information from individual channels. Evidently such a system involves a tremendous amount of resources in the setup and is therefore not easily changed, rendering it quite inflexible. What it is good at, is to produce the same product in very high quantities.
Decentralized control intelligence for industrial 4.0 applications: This is already possible in tightening technology.
In the Industry 4.0 setting however flexibility even down to the ability to allow a batch size of one is often the requirement. An efficient way to handle changes is to make as many logic decisions locally.
Instead of a top down approach, a local decentralized intelligence allows variables in the production demand handled as it comes down the line. Intelligence that can be added locally such as a barcode scanner combined with a local controller that handles logic decisions on the fly provide efficient and flexible solutions to complex challenges.
An example how a Nexo combined with its integrated barcode scanner and its integrated controller could handle a real life production challenge is described in a real life example below:
A customer has four products to build with each requiring twelve tightening applications involving a M8 bolt and eighteen tightening applications involving a M6 bolt. The customer likes to minimize costs and likes to do all work with just one tool, instead of two different tools with individual controllers and an additional barcode scanner.
The solution was provided with one Nexo model that covers the torque range for both the M8 and the M6 bolts. The Nexo nutrunner designated for the application was one that contained an integrated barcode scanner for the identification of the tightening joints (bolts). In addition to the logic decision, the value stream is increased by the attachment of the type and serial number of the parts of the assembly in the documentation.
The benefits of this approach – Nexo with barcode scanner for logic decisions locally – lies in the ability to bring flexibility and efficiency to complex tasks without the need to re-program and configure upstream PLCs.
The benefits of a use of the Nexo do not stop here. In many assembly settings there arises the need for line balancing, meaning very often a relocating of assembly tasks from one station to another in order to streamline the production flow. For a line balancing involving tightening tools, a tightening system with its associated controller would involve to dismount an existing controller, disassembly the cables from its trays and festooning devices and re-install all of the above in a new location as well as providing power and grounding connections, communication wiring to the controllers and laying and festooning new tool cables. With a cordless Nexo nutrunner, the task may be as simple as taking the tool to its new assembly location. No cables, no wiring to worry about. A highly sophisticated system – almost plug and play like. Lean manufacturing does not get better than that.
Even complex tightening systems can be mapped mobile and wirelessly using decentralized intelligence. This facilitates line balancing.
As a tightening system that can be used in safety critical applications the Nexo nutrunner, like most other tightening products from Bosch Rexroth does more than just tighten and report torque and angle values associated with its operation. Using its ability to receive and send signals from line controls, this battery tool with its wireless communication is behaving like any wired machine that is fully integrated vertically in the production process. As such for example it can be fully integrated in apoka yoke system contributing its part in a zero fault production. It can through proper parameterization identify whether parts that it expects are truly present in the assembly. If in a tightening operation for example a washer has to be combined with a bolt, a forgotten washer would be identified by the means of a wrong (increased) angle value. Another example: a bolt with a wrong thread length.
The combination of the intelligent Nexo with its barcode scanner can provide a new ID that will consist of multiple single ID inputs. So you could document through an ID Code that in the assembly of a product various parts were scanned. This ID code becomes then with the tightening results part of the final documentation for this assembly application. With respect to traceability, a higher transparency of the tightening process can be achieved. If a product defect occurs, a determination of the cause of error is possible by a review of the collected data. It enables, if necessary, an individual-item based recall with a reduced recall quantity.
To summarize, it is not the centralized PLC, which assures that the required parts were identified, used in the proper order and finally tightened within the required specifications and truly no bolts were missed before the part was advanced to the next assemby stations. This is in control of the Nexo – the intelligent, cordless nutrunner.