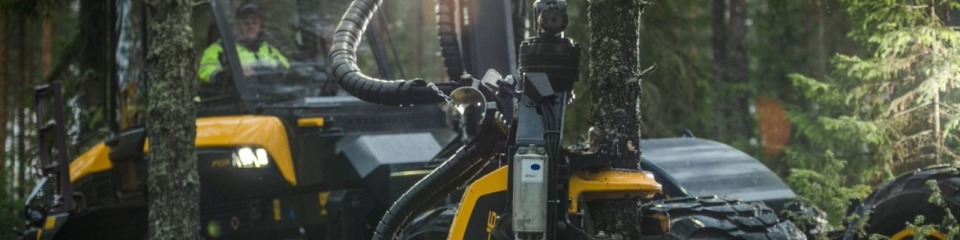
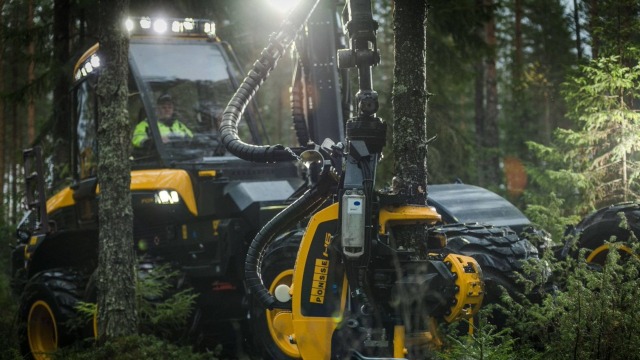
Harvesters are impressive machines. They work extremely economically – provided they are in operation. Together with Bosch Rexroth and Bosch.IO, forestry machine manufacturer Ponsse is taking its after-sales service to the next level.
As for every manufacturer of off-highway vehicles, after-sales service is an equally important and demanding task for Ponsse. This is because the efficient cut-to-length forestry machines of the Finnish company usually work in remote locations and under considerable loads. In order to avoid unplanned standstill times and minimize downtimes, Ponsse Service must act promptly and at an early stage. This is all the more true in the case of full-service contracts including extensive maintenance work. With the help of the Internet of Things and IoT solutions from Bosch Rexroth and Bosch.IO, Ponsse has come a great deal closer to meeting the customer’s wish to keep mobile machines ready for operation at all times.
The hardware and software components of the IoT partners Bosch Rexroth and Bosch.IO fit seamlessly into the existing infrastructure of Ponsse. They make the condition of the machine transparent and allow service technicians an even deeper insight from a distance. Ponsse can thus offer its customers a completely new level of support.
By default, harvesting machines often work in very remote areas. This is why it is crucial to reduce unplanned standstill times and downtimes to an absolute minimum. (Picture: Ponsse)
Ponsse has already had its own IoT infrastructure for recording and transmitting machine data for some time. With Ponsse Manager, the company also provides its customers with a tool for managing their operations, vehicle fleets and documentation processes. The long-standing cooperation with Bosch Rexroth in the field of hydraulic components has been expanded as part of the ongoing digital transformation.
Structure-borne noise analyses on rotating components such as hydraulic pumps now create the prerequisites for predictive maintenance. The usage data of Rexroth components are also included in the preventive consideration. The data collected in the vehicle is analyzed with the help of special algorithms, also developed by Bosch Rexroth.
In this IoT project, individual modules from the modular IoT value proposition BODAS Connect are used. With BODAS Connect, Bosch Rexroth offers off-highway manufacturers a great deal of freedom in designing their infrastructure and shortens the solution development time with proven and easy-to-configure modules. The portfolio of the Bosch Rexroth IoT kit ranges from connectivity devices to device management, data management and a comprehensive portfolio of apps and services. Ponsse uses an intelligent sensor solution as well as the cloud-based data management service Bosch IoT Insights from Bosch.IO. This is where the collected data is stored, managed and visualized by means of dashboards.
(Picture: Ponsse)
The IoT solution introduced in 2019 is having a positive impact at Ponsse. The after-sales service has become more proactive and the company is able to point its customers to potential problems and take action even before a machine fails. All in all, Ponsse can now take care of its customers’ problems faster and more efficiently, and contact with the service department is an even more positive experience.