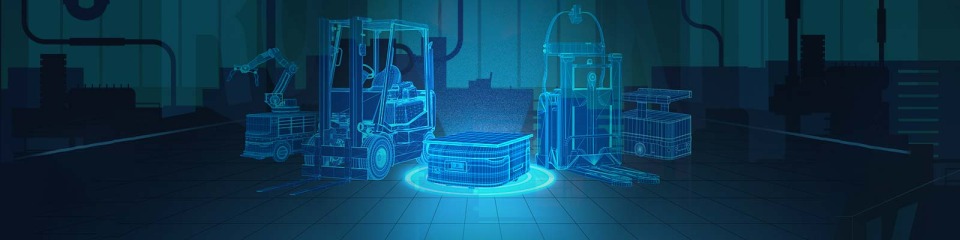
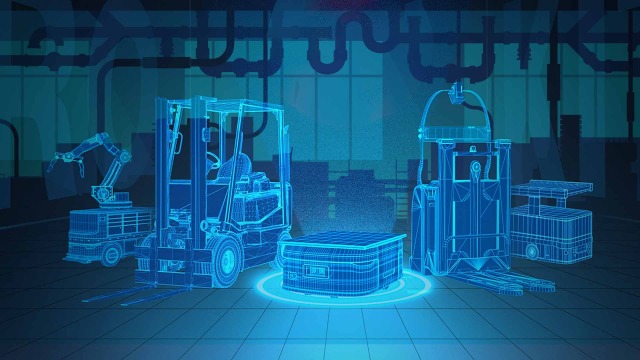
With the growing use of mobile robots in warehouses, it is becoming increasingly important to ensure smooth cooperation between manual and automated vehicles. But how can a mixed fleet be coordinated efficiently?
In the dynamic world of warehouse operations, automated guided vehicles (AGVs) and autonomous mobile robots (AMRs) are often an integral part of intralogistics operations. By 2028, 50 % of large companies will use mobile robots in their warehouse or production operations1. 40 % of large companies will use heterogeneous vehicle fleets in their warehouse operations within the next five years1. While they relieve workers and take over tasks, they also increase the volume of traffic. This becomes particularly challenging if the traffic in the warehouse is not fully transparent and centrally managed.
As not all tasks can be automated by mobile robots, the use of manned vehicles is still necessary. However, mixed operation raises various challenges:
The solution to these challenges lies in the integration of manual vehicles into a powerful fleet management system. By 2026, more than 50 % of companies using intralogistics robots will be using a multi-agent orchestration platform1. Here are some reasons why this can be an extremely worthwhile investment:
A crucial aspect of integrating manual vehicles into a fleet management system is the support of standards such as VDA 5050, which defines uniform interfaces and protocols for seamless communication and coordination between vehicles and higher-level systems. By implementing VDA 5050-compliant solutions, companies can improve the interoperability of their fleets and further increase the efficiency of warehouse traffic.
The integration of manual vehicles into an existing VDA 5050-compliant fleet management system is therefore a decisive step towards increasing efficiency in warehouse operations and reducing costs. To achieve this goal, it is necessary to retrofit manual vehicles with suitable technologies and ensure effective real-time localization and tracking. There are various technologies available to make this possible. The proven laser-based "Simultaneous Localization and Mapping" (laser SLAM) technology of autonomous vehicles is often also used in manual vehicles.
Laser SLAM offers an advanced method for localizing manned forklift trucks and mobile robots in industrial environments. Compared to other technologies, it is highly precise with comparatively low commissioning costs. Vehicles are equipped or retrofitted with a laser scanner for this purpose. The sensors send laser beams and measure the reflections of objects in the environment. At the same time, the algorithm analyzes the vehicle's movements and creates a real-time map of its surroundings. This simultaneous mapping and localization function makes it possible to locate and navigate vehicles in real time, even in dynamic warehouse environments.
With a laser-based localization software such as the Rexroth ROKIT Locator both mobile robots and manual vehicles can be localized using the SLAM algorithm. The ROKIT Locator enables the precise detection of vehicle position and movement in real time – without any further infrastructure adjustments. The API enables seamless integration into existing (interoperable) fleet management systems. This enables precise coordination of the interoperable vehicle fleet. Manual vehicles can be monitored in real time, routes optimized and collisions avoided.
In addition, the localization software makes it possible to analyze and optimize the performance of manual vehicles. By continuously collecting data, companies can make further operational improvements that additionally increase their efficiency.
AMR, AGV or forklift truck – use the ROKIT Locator flexibly!
With the ACTIVE Shuttle Management System (AMS), Bosch Rexroth supports the VDA 5050 standard.
With the ACTIVE Shuttle Management System (AMS), Bosch Rexroth supports the VDA 5050 standard and offers a fleet management system that simplifies the coordination of warehouse traffic. The central system can be used to control orders for autonomous mobile robots and manage traffic in the warehouse.
By supporting the VDA 5050 standard in the AMS fleet manager, Bosch Rexroth offers the possibility to connect manual vehicles by retrofitting them with the ROKIT Locator in order to reduce the challenges of accidents, operational inefficiencies and coordination difficulties in warehouse traffic. The AMS offers an orchestration function for VDA 5050-enabled vehicles and thanks to the "deep boarding" of selected vehicle types, it provides functional added value compared to generic VDA 5050 fleet management systems.
1https://futureiot.tech/orchestrating-the-heterogeneous-robot-fleet/. Retrieved on 07/18/2024.
Do you recognize some of your current challenges? Use the full potential of your fleet and make your goods transportation faster, more efficient and more sustainable!