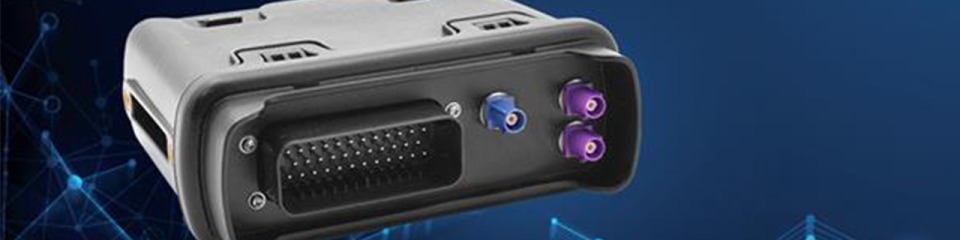
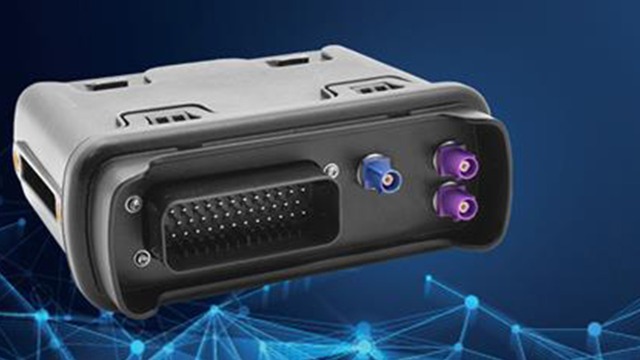
Software updates are about much more than fixing bugs and closing security gaps. In both mobile applications and industrial environments, more and more manufacturers are realizing that they can provide additional functionality for their diverse assets through updates. That way, they are not only addressing the needs of their customers. They can also understand software updates as a basis for implementing new business models in the future.
With the help of over-the-air updates (OTA), this can now be achieved much more easily and efficiently. Manufacturers don’t have to send out technicians to manually install updates, and customers aren’t forced to bring their machines into the shop.
A question of device technology
As customer needs are constantly changing and establishing new business models takes time, industrial asset manufacturers are faced with the question: What basis can they build on today to exploit the full potential of software updates in the future?
Telematics Control Units based on microprocessors are open and modular systems, usually on the basis of a layer architecture. This makes them flexibly deployable for a wide range of use cases, including future ones. (photo: Bosch Rexroth)
A key answer lies in choosing the right IoT hardware. Whether it’s a construction, agricultural or forestry machine, manufacturers need to consider which devices they want to use to network their assets. The distinction between a microprocessor and a microcontroller architecture plays an important role here.
The important distinction between microprocessors and microcontrollers – example Telematics Control Unit
How does this distinction translate to the hardware decision? It is helpful to take a look at the Electronic Control Units (ECU) of a machine – in particular the Telematics Control Unit (TCU): Its aim is to wirelessly connect the machine to higher-level IT systems in the cloud. This is done in the TCU with the help of hardware, an operating system (OS) and various software modules. The TCU is the central networking unit to which other control units and sensors are sometimes connected.
When selecting the right TCU, the focus is less on the question of which functions could be relevant in the future. It is more about laying the foundation for the flexibility and future-proofing of the entire IoT solution.
Deep dive: the whitepaper "Telematics for Construction and Agricultural Machinery: Device Management" shows how off-highway machines can be efficiently and securely connected via the Internet of Things without reaching a technological dead end.
Compared to a microprocessor-based TCU, a microcontroller-based TCU is often less expensive and may well cover all the requirements that a manufacturer currently has. However, should new customer needs or technical progress arise in the future, things will become more complex: Due to specialization and cost optimization, these devices typically have limited resources, so they allow only limited customization and expansion. For example, it is almost impossible to extend such a microcontroller architecture with a 5G module without changing the existing design significantly. This in turn entails correspondingly extensive software changes, because with a new architecture, the old software cannot be simply reused.
A TCU based on microprocessors may be more expensive to purchase, but manufacturers can react more flexibly to new developments by means of software updates. Software changes are easier and faster to make because such systems have open interfaces and typically have many libraries available. Thus, the implementation of a 5G module would be much easier by extending the software. The microprocessor architecture also creates better conditions for bringing new applications to the device in the future and thus realizing new business models (such as licensing models).
Overview telematics hardware architecture based on microprocessor vs. microcontroller (source: Bosch Rexroth)
A flexible approach to over-the-air updates
The properties and possibilities of hardware architectures therefore depend heavily on the basis on which they are built: microcontrollers or microprocessors. Manufacturers are therefore well advised to take these fundamental differences into account in their strategic considerations. However, this does not mean having to choose. When using a TCU from Rexroth (BODAS RCU), the integrated OTA Update Agent comes into play. As a central software agent, it not only ensures smooth updates of the TCU itself. It can also network downstream devices based on microcontrollers and distribute over-the-air updates in a targeted manner.