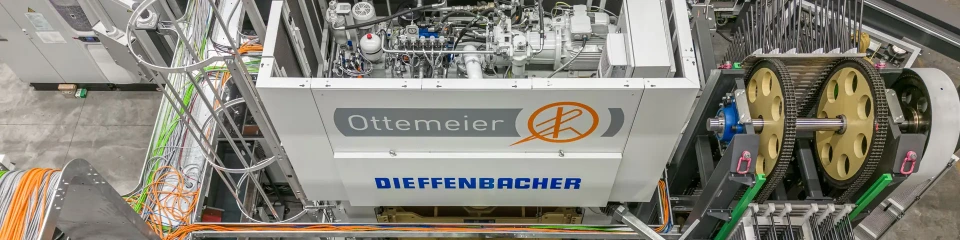
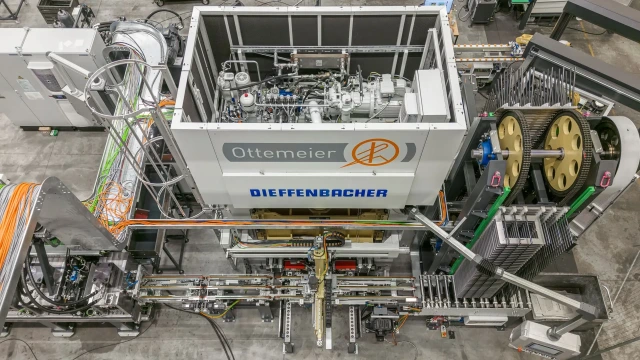
How can a press series in the medium performance class be designed and produced in such a way that impresses in terms of price, technology and energy? The leading manufacturer of press systems Dieffenbacher has found an answer using state-of-the-art industrial hydraulics from Bosch Rexroth.
Great performance, great price – with this promise, machine and system manufacturer Dieffenbacher is assisting small businesses such as craft businesses and workshops as well as industrial companies that are looking for an economical solution for forming metal and composite components. But how can a highly versatile press for forces of 1,000 to 10,000 kN be built in such a cost-effective way that it is able to hold its own in international competition?
“We wanted to build a future-proof press from standard modules that can be customized in terms of force, installation space, table and ram size”, explains Georg Obermaier, Head of Business Unit Forming, the new TailoredPress concept from Dieffenbacher. “At the same time, we placed high demands on energy efficiency. We found both aspects were fulfilled by our system partner Bosch Rexroth, with whom we jointly designed a modular drive concept that they were ultimately able to produce for us.”
The modular drive concept means that the machine manufacturer can easily offer the TailoredPress in different performance and speed classes. For example, a 500-tonne version can simply be upgraded to a speed version with active high-speed parallel holding for precise component thicknesses and higher component quality by using a different pump size. The entire range of services is covered by the Bosch Rexroth pump program as required, which streamlines the processes over the life cycle from engineering to warehousing and service. Other versions with draw cushions can also be realized quickly if required using the modular system.
Compared to the conventional drive with a constant speed, the optimally controlled electrohydraulics save around 50 percent of the energy previously required. Together with the adaptive battery control, the potential increases to 70 percent. The directly driven TailoredPress automatically adjusts the charging pressure of the hydraulic accumulator to the upcoming forming process. From the perspective of the operating personnel, however, nothing changes. Forces, travel and ram parameters are set as usual, the respective speeds are calculated in the background.
Would you like to find out what the solution looks like in detail? You can find out here: