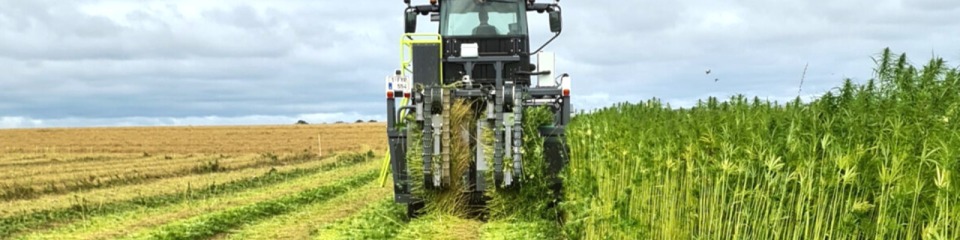
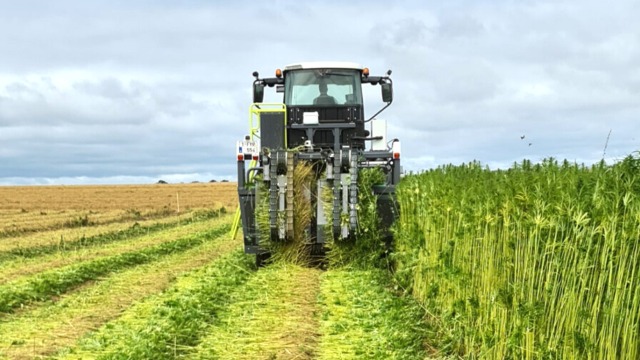
Commercial hemp has a future. With support from Bosch Rexroth, the Belgian agricultural machinery manufacturer, Hyler is implementing a self-propelled harvester including telematics. The fact that the machine will be capable of harvesting other fiber crops in future makes it all the more interesting for agriculture.
Long-fiber plants are regarded as the raw material of the future. They are versatile and help protect the climate because they are carbon-negative, require little water and promote biodiversity. This is particularly true of commercial hemp, which can cope without agrochemicals in an increasingly dry climate. However, industrial harvesting is not trivial. With end-to-end support from Bosch Rexroth, the West Flemish agricultural machinery manufacturer, Hyler has now developed an innovative solution that also excites its users in terms of connectivity.
The harvest-relevant data provides users with valuable information and parameters to optimize the harvesting process, such as the length of the swaths and the layer thickness. In addition, the RCU also records support-relevant data such as consumption, hydraulic pressure or geoposition. This enables Hyler to support its customers with remote diagnostics or remote configuration and ultimately optimize service and maintenance.. "For our customers, telematics is a great benefit, because we can help them immediately in the event of technical problems," says Niels Baert. However, it was also particularly important to Hyler to update the intelligence of the harvesters efficiently without having to send a technician to site. The complete package BODAS Connect Device Connectivity provides tools suitable for mass production including the Bosch IoT Suite platform, which has been proven a million times over. This allows both the firmware of the RCU and RC controllers as well as the driving and working software and the device software of the RCU to be updated over the air in a fail-safe manner (FOTA or SOTA) and managed highly efficiently.
Real-time data from telematics also plays a key role when it comes to fine-tuning the travel drive, working hydraulics and vehicle software. "This information is very important for testing, as there is hardly any historical data for a completely new machine from which ideal behavior can be derived," explains Maarten Van Houtte, responsible Account Development Manager at Bosch Rexroth Belgium. "For this purpose, the RCU provides us not only with important parameters but also with wear and driving conditions with a geographical reference, so that we can compare the target/actual behavior of the hydraulics precisely. This way, we not only find the best solution each time together with the customer, but can also modify it much more efficiently and improve it further in future."
In addition to the safety functions and working hydraulics, the BODAS software developed by Bosch Rexroth also controls the travel drive. On the hardware side, this consists of an A4VG high-pressure axial piston pump and four GFT8120 wheel gears with dynamic braking and integrated A6VE hydraulic motors. The programming is based on standard components from the BODAS software library such as DRC (Drive Control), HLB (High Level Breaking) or ASR. The components required for implementation, such as the controller, sensors and joystick, come from the BODAS Mobile Electronics portfolio. The various circuits of the working hydraulics are driven by reliable Rexroth gear pumps and A10VO/A10VG axial piston pumps as well as a 2-circuit variable displacement pump A30VG with differential lock function, which made it possible to implement the customer-specific hydraulic circuits in a compact, efficient and flexible way.
Supported by Bosch Rexroth's standard solutions and application knowledge, Hyler was not only able to realize inspiring driving behavior and innovative harvesting functions in a short time, but also a high-performance connection to the Internet of Things. "With Bosch Rexroth, we always find the right solution for the individual machine and its components," says Niels Baert. The market interest in the Sativa 200 with the development partner's overall package of reliable hardware, innovative software, and telematics proves him right. Even before the start of production, the first batch was sold out, and Hyler has a waiting list for the current year. Niels Baert is sure that demand will increase even further when the first farmers report on their harvesting experience. "The jointly developed harvester is a real breakthrough for Hyler," he says. "We look forward to advancing the future of fibre crops together, and want to realize many more applications together."