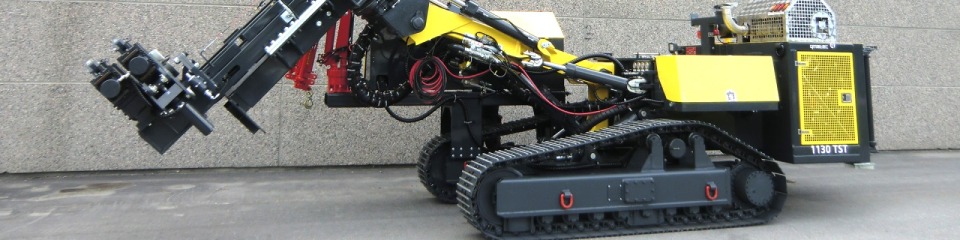
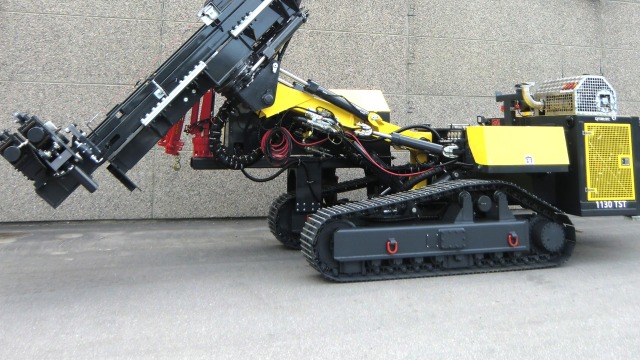
Drilling rig manufacturer Qmatec has entered the digital age with minimal use of resources. The complete telematics package from Bosch Rexroth with over-the-air services allows a nationwide remote service and helps end users to improve their transparency, productivity and environmental credentials.
Norway is famous for its impressive natural beauty. Fjords many kilometers in length, high mountains, countless islands, lakes and rivers leave an unforgettable impression on tourists. At the same time, however, the rugged landscape is a geographical hurdle when it comes to servicing off-highway machines on location in remote regions. With the help of Bosch Rexroth, Qmatec has found a solution for remote diagnostics and maintenance which prevents unplanned downtimes and helps to boost business.
Fleet overview: Qmatec machines are used in Scandinavia, Great Britain and as far afield as Greenland.
Qmatec specializes in mobile drilling rigs. At the Vinje plant, over 200 kilometers to the west of Oslo, around 25 new vehicles are produced every year. They are used for foundations, water supply systems and energy recovery throughout Scandinavia, Great Britain and even in Greenland. “International demand is increasing, as a result of which remote maintenance is becoming increasingly important,” said Managing Director Tor Olav Kyrkjebø. “In Norway alone, our service department has to cover an area around 2,500 kilometers in length.”
“Without efficient telematics, we couldn’t have managed the growing fleet which is spread across an increasingly large area in a satisfactory manner,” said Service Manager Sondre Frøland. “Our aim was to monitor not only the drilling process but also the working hydraulics and the diesel engine, to read out corresponding error codes and to track the geoposition of our machines. We also wanted to update the software modules for our machines over the air and to change important parameters remotely so that our customers could complete their projects on time even if servicing was suddenly required.”
Qmatec 407 TS: Intelligent terrain rig with IoT connection for over-the-air updates and parameterization (XOTA). The combi machine is used for wells, geothermal energy and foundations all over the world. (Image: Qmatec)
At the start of the telematics project in 2019, it was clear that Qmatec could not develop such a technically complex solution itself and would not be able to enlist a provider that was unfamiliar with the design, functions and areas of use of its machines. “We immediately thought of asking our partner Bosch Rexroth as the company had already provided a range of support when we were developing our application software,” recalled Tor Olav Kyrkjebø. “The company has also provided pump units, control units and drive motors for our drilling rigs for over 15 years.”
On the basis of Bosch Rexroth’s BODAS Connect telematics solution, a pilot project for the first intelligent terrain rig soon began. “Any insight into an off-highway machine is only as deep as our understanding of it,” said Øyvind Kjølberg, Qmatec’s account manager at Bosch Rexroth. “Our telematics systems offer small and medium-sized companies in particular a major advantage – they combine application knowledge with large-scale production-proven IoT components that we have specifically adapted to the needs of off-highway vehicles. This is the basis for an open, scalable ecosystem whose modules reduce the development work to a minimum.”
Qmatec opted for BODAS Connect All-in-one Connectivity, a proven end-to-end telematics solution which would allow a quick market launch. It comes supplied with sensors and the Rexroth Connectivity Unit (RCU). The processor-based telematics unit is used to collect vehicle data as needed and to transmit them efficiently. It is also the central component for device management including the over-the-air services which are so important to Qmatec.
As a complete telematics package, BODAS Connect All-in-one Connectivity includes all necessary modules for setting up scalable, end-to-end solutions quickly.
The telematics solution from the BODAS Connect ecosystem logically separates device and data management. This helps to improve security because the user groups for machine and operating data can be separated cleanly and the relevant authorizations can be assigned in detail. The individual functions can also be easily distributed among various people or departments in order to improve usability.
Via a dashboard, Qmatec’s service department can view all necessary information, for example a list of machines with a location graphic. There is also a detailed view with service-relevant data for each machine. Additional tabs provide information regarding the status of the telematics units, diesel engines and working hydraulics. Graphical curves visualize changes in vehicle data over time so that critical values such as pressure peaks, oil temperatures or filling levels can be viewed quickly in context. Alarms or messages are triggered if specific threshold values are exceeded.
The 1130 TS mobile terrain rig weighs over 23,000 kg and has a torque of 8,000 or 16,000 Nm with a feed length of 7,000 mm. (Image: Qmatec)
Software management for the built-in RCU and the control units from Bosch Rexroth takes place regardless of location via the Bosch Rexroth Device Portal and XOTA services (Everything Over the Air). In addition to firmware and software updates, the service team passes on individual adjusted parameters to the machine to improve its functionality or rectify acute faults. With these tools, Sondre Frøland already managed to maintain the productivity of a machine over 2,000 kilometers away when the pump for the water cooling system failed after the first borehole was drilled. Frøland remotely updated a number of parameters, had a new hydraulic hose installed and the job could be completed as planned after a short interruption. In contrast, an immediate repair on location would have resulted in a four-day delay, high transport costs and, presumably, an unhappy customer.
With the help of the XOTA services, Qmatec can not only make a range of changes quickly and easily from a remote location. They can also set up complete machines in just an hour, something which in the past was only possible with a locally connected PC. “Our customers thus benefit from reliable operation with optimum operating times,” said the service manager. “The XOTA services not only reduce maintenance and repair costs – they also reduce travel costs because many cases can be solved remotely instead of spending two or three days carrying out servicing work on location.”
Qmatec initiates regular maintenance on customers’ premises and the customers are then given a countdown until the next service is due. A predictive maintenance application is also a possibility in the future in order to extend the operating life of monitored components and thus optimize the cost of maintenance and spare parts.
Data collection in the now transparent machines offers great potential for improvements. Not just for service planning and further development but also for customers who can now limit fuel consumption and greenhouse gas emissions through automatic stops or notifications for example. The position and production data indicate how far a particular drilling machine has traveled and how many hours it was in operation. “Our customers are very keen to find out how profitable their work is,” said Tor Olav Kyrkjeb. “We’d like to provide customer-specific portals soon – portals which will make planning easier and allow billing based on the number of operating hours. The modules and interfaces needed for this are already included in the complete package from Bosch Rexroth.”
Status view for the diesel engine: Top: Graphical display of speed, coolant temperature, oil pressure, pump pressure, fuel consumption and battery voltage. Bottom: Further information regarding hydraulic and lubricating oil, diesel particle filter and Adblue.
Firmware and software updates must be transferred to the vehicle securely and reliably. Bosch Rexroth uses OTA mechanisms for this, mechanisms which have proven themselves on countless occasions in the automotive sector. In off-highway vehicles, the robust and highly secure Rexroth Connectivity Unit (RCU) ensures that all files are transferred. Only then is the target device updated following authorization via the CAN bus. The update processes are therefore as stable and secure as an update via cable using a laptop and a diagnostics tool.
Efficient standard for telematics
Qmatec now equips all new machines with an RCU as standard. The RCU will also be retrofitted to another 150 or so existing machines. All models use the same telematics unit with standardized device software and the same CAN messages. As always, type-specific differences are parameterized over the air. With the modular BODAS Connect All-in-one Connectivity complete package, the Norwegian manufacturer has established telematics quickly with minimal use of resources. “It was very helpful to be given a proven solution from one company which we can expand all the time by adding new functions and services,” said Tor Olav Kyrkjeb. “This is extremely important for the efficiency and growth strategy of our company.”