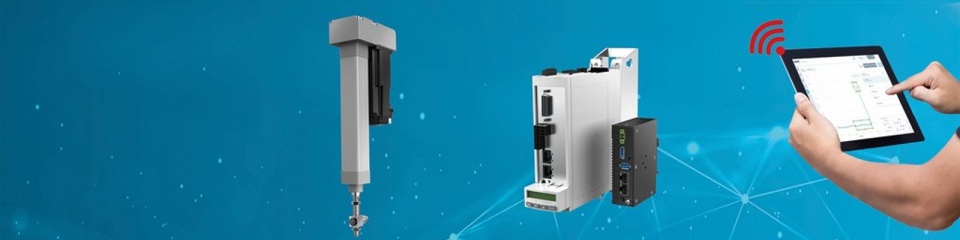
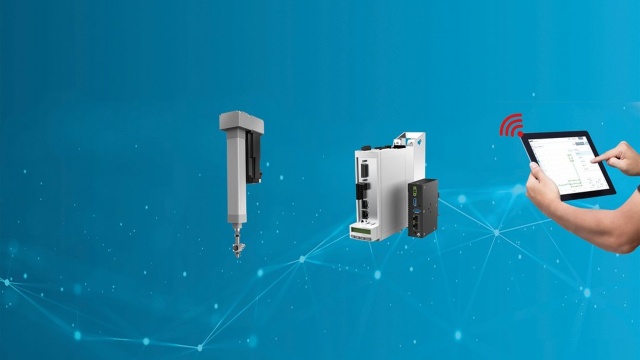
Brad Klippstein, Product Management – Mechatronics Bosch Rexroth
Assembly operations that use handling, joining, and pressing tools for a range of production applications — including fastener manufacturing — continually seek to improve the versatility, ease of use, production time, and quality of such operations.
In today’s digital world, this means adding smarter, Industry 4.0 capabilities to production platforms. For efficiency, this must entail data tracking of a machine’s production and performance with real-time sharing capabilities.
As manufacturers begin to incorporate the benefits of Industry 4.0 technology, a new concept called “smart mechatronics” has evolved, offering more intelligence and functionality in handling and joining. Mechatronic systems are devices that have fully integrated mechanical and electrical components, thanks to the combination of sensors, circuits, and motion-control applications.
In some ways, mechatronic systems could be considered a forerunner of Industry 4.0 technology. They combine disparate mechanical and electronic components into solutions for specific product assembly and transport tasks, such as Cartesian robots (capable of moving in multiple linear directions) and forming and crimping tools.
Meeting industry needs at one time, mechatronic solutions were integrated with components from multiple suppliers. That’s no longer the case. Mechatronics suppliers are replacing that time-consuming acquisition and integration step with complete solutions that are “plug and produce.” This includes the software necessary, which is preprogrammed and delivered as a single production tool. Manufacturers should know that all of the components for a complete mechatronic solution — a Cartesian robot or a pressing or joining tool — can now be specified.
Assembly operations are shifting away from individual products toward complete system kits for manufacturing equipment that produces fast solutions for handling, joining, and pressing tools — along with real-time data.
Users can enter parameters such as stroke, workpiece weight, and cycle time, which generates an output that can be verified in the CAD environment.
It’s clear end users require precise control and execution of motion sequences, but also automated tracking of production data and easy connectivity with machine-level and plantwide production management systems.
Additionally, there’s a demand for easier and faster changeovers. Many production lines or mid-sized shops seek tools that make it easier to produce a range of batch sizes — from the low end of only a few thousand parts up to hundreds of thousands — without extensive effort to reprogram tools for a new part.
The price point also matters. End users require cost-effective measures that meet budgets and readily support manufacturing orders. Kitted solutions that provide flexibility in a space-saving envelope with minimal integration time are highly desired.
Easier, faster commissioning is one significant advance provided by newer, smarter mechatronic systems and the technology that supports them. Equally valuable are the improved efficiency, flexibility, and productivity it provides end users looking for easy-to-automate solutions.
For those wanting to integrate mechatronics and update production lines, consider systems that:
Times are changing, and so are industry requirements and processes. To keep up, fastener manufacturers are wise to digitalize their operations with Industry 4.0 technology.
Smart mechatronics solutions leverage easy to-use tools, such as drag and-drop functionality and simple programming. Bosch Rexroth’s Smart MechatroniX system for pressing and joining applications is one example that demonstrates this intuitive model.