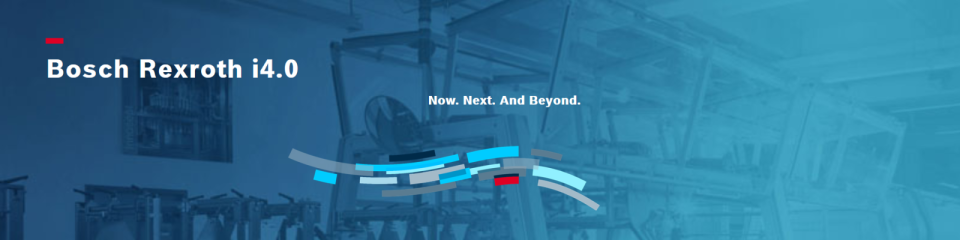
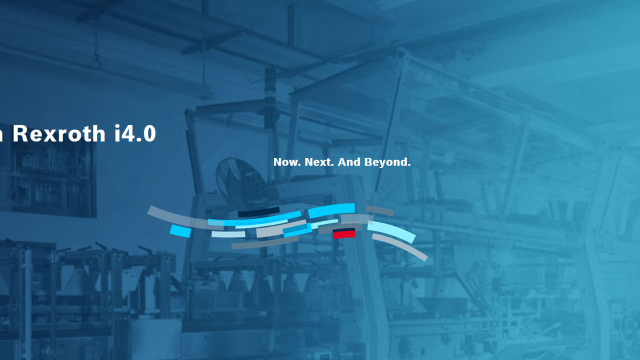
Author: Bosch Rexroth | August 30, 2021
Everyone is certainly familiar with the definition of “robot”, a machine which substitutes humans in certain dangerous or repetitive tasks. They have been our companions for decades now, driving up productivity and safety in a wide variety of applications. Robots can lift heavy weights without getting tired or incurring injuries, and repeat tasks with greater accuracy than a human operator. Robots can even work in hostile environments without putting people’s safety at risk, as is often the case in automotive welding or painting.
We can assert that robots help people, as long as they are operating a safe distance away. Ideally, they must be confined in certain areas of a factory floor that are specifically designed to enable them to freely move around without hurting humans. Consequently, the requirements increase to ensure this safety is met: more space is required on the shop floor, more safety procedures are needed to enter a robotic cell, and stricter in-feed and off-feed procedures are needed when human operators must interact with them.
Do not get us wrong, robots are great machines, with very well understood kinematics and dynamics, accurate movements and incredible repeatability, but they are missing one key element to be truly a great human companion: they lack awareness of their surroundings. Cameras, light curtains and similar safety sensors do not really offer a proactive mechanism to dynamically change the robot controls and quickly adapt to environmental changes.
Rise of Cobots
The manufacturing industry has always been receptive to technological innovation, spearheading many novel devices for pushing the boundaries of productivity. Collaborative Robots, hence the word Cobots, were designed to specifically address the increasing need of flexibility and collaboration opportunities in those areas where human operators and robotic arms could benefit from each other’s proximity.
Unlike the more commonly known, larger robotic manipulators, cobots do not require a fenced-off area to work, nor specific safety requirements; they can be deployed shoulder to shoulder, or better yet, shoulder to arm, next to a manual assembly station or in areas where humans walk by and feed material directly to a cobot. This way, machine-to-machine and human-to-machine interactions can flow seamlessly.
Cobots can be easily deployed and re-deployed in other parts of the plant floor based on production demands, following the core principles behind the Factory of the Future, where manufacturing environments are seen as flexible spaces where only the walls are fixed elements.
Paradigm Shift
From a manufacturing operations perspective, how do we effectively make use of cobots to improve safety, quality, cost and delivery? First, we must consider the use case and choose the right robot. Some common applications of cobots include assembly, pick and place, sorting, material picking, and packaging / palletization.
Not only can tedious, repetitive, and dangerous tasks be completed with more accuracy and predictability by a robot, but now with cobots we can develop hybrid workplaces that combine skills from humans and robots that allow for the automation of tasks that were not previously able to benefit from the addition of a robot.
What are the main aspects we must consider before adopting this new technology? As with most robot applications, we must consider aspects like reach, speed, payload, part identification, manipulation, etc. We must also consider the level of collaboration in four different degrees:
We cannot forget the people side of any change and how important it is to have a comprehensive, well thought out change management plan as part of implementing any cobot solution. With increased automation comes increased complexity that must be addressed via different human responsibility, for example from laborer to (robotic) supervisor or technician. Good communication is also key to ensure that cobots are viewed not as a threat to people’s jobs but rather as a helpful assistant to relieve workers from repetitive, dangerous tasks and improve productivity.
Future-proof Machines
Cobots are machines designed in the Fourth Industrial Revolution, therefore they bring with them a new approach also towards the IT side. Simulation is deeply integrated with the teaching processes; users can easily program a cobot “on the spot”, bringing the machine in its work location and use the programming software to teach its movements by manually moving the arm point after point. This makes for an extremely fast and intuitive commissioning.
Being the “newcomer” in the space, cobots typically offer all the perks you would expect from a modern Industrial IoT device, such as full cloud connectivity out of the box. Data is seamlessly and securely sent to the vendor’s cloud backend using standard communication and encryption protocols, and for this reason simulation, programming and monitoring applications are now browser-based. Cross-team collaboration becomes more agile, and analytics and condition monitoring reports can be accessed everywhere.
Moreover, the emerging cobot technology enables an evolutionary design of a production line without the productivity risk generated when a line is completely redesigned or retrofitted. This results in the possibility for the increase of cobot utility as software and hardware ecosystem capability grows.
Honorable Mention
So far, we have made the implicit distinction between the so called anthropomorphic cobots (those which resemble a human arm) and the rest of autonomous robots, such as Autonomous Mobile Robots (AMRs). It would be fair to include the latter ones into the category of collaborative robots, as they are already widely used in many different applications.
AMR can autonomously change routes, can safely work in the same working spaces with humans, and have a wide range of sensors and connectivity options. The intralogistics segment is certainly the most favorable space for Industry 4.0 solutions adoption, seeing an exponential growth in collaborative robot deployments around the world. Given the current trends of AI and edge computing capabilities, the AMR market is expected to expand 300% by 2027 reaching 3.14 billion USD [1] [2].
References
[3]https://www.grandviewresearch.com/industry-analysis/automated-guided-vehicle-agv-market
[4]https://www.youtube.com/channel/UCRdXQhcn_R3b_rfEjYe_Tyg/videos