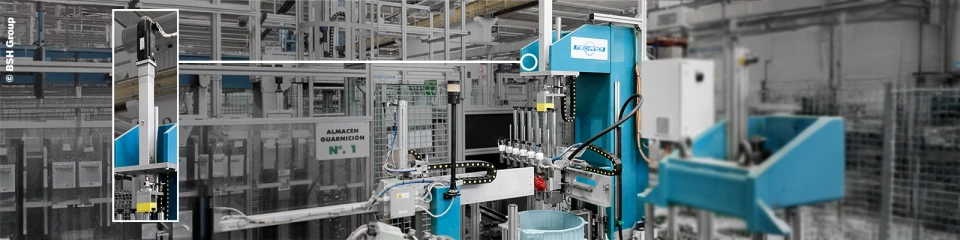
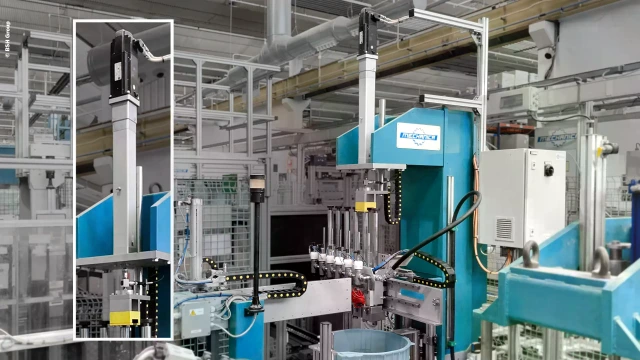
Společnost BSH Group standardizuje procesy lisování a spojování, které jsou kriticky důležité pro zajištění kvality při výrobě praček. Jak? Pomocí mechatronického subsystému Smart Function Kit Pressing. Výsledek: Vyšší flexibilita, stabilita a transparentnost s minimální dobou potřebnou na vývoj, integraci a řízení kvality.
Podle Maxmiliana Aßmutha z týmu Laundry Care Industrial Engineering společnosti BSH mají nově zavedené elektromechanické servolisy založené na systému Smart Function Kit Pressing zásadní výhodu oproti dosud používaným pneumatickým řešením. Umožňují realizovat vysoce přesné procesy, šetří energii a poskytují spolehlivý základ pro zajištění kvality a další optimalizaci procesů. Proč? Protože elektromechanické servolisy přeměňují elektricky generovaný točivý moment přímo na pohyb pomocí šroubového pohonu v elektromechanickém válci EMC, provádějí jeho jemnou regulaci a přesně zaznamenávají data procesu pomocí senzorů a softwaru. Právě tyto výhody využívá společnost BSH ke zvýšení hospodárnosti procesů v globální výrobní síti.
Maximilian Aßmuth
Tým Laundry Care Industrial Engineering společnosti BSH
Mezinárodní projekt standardizace byl spuštěn s prvním systémem Smart Function Kit Pressing pro továrnu v La Cartuja poblíž španělské Zaragozy. Mechatronické řešení se skládá z elektromechanického válce se silovým senzorem, servomotoru se servopohonem a průmyslového počítače s předinstalovaným operačním softwarem. Při výrobě praček se chytrý servolis používá ke spolehlivému zajištění kritického utěsnění mezi hřídelí bubnu a vodní nádrží, která drží vodu v pračce. Díky kompletní předmontované sestavě a kvalitní přípravě měl projekt rychlý úspěch. Výkonná kombinace lisovací technologie, softwaru a služeb byla spolehlivě uvedena do provozu za pouhé tři dny včetně zkušebního chodu.
První systém Smart Function Kit Pressing společnosti BSH byl uveden do provozu v závodu La Cartuja poblíž Zaragozy v roce 2021. Po celém světě je v současné době v provozu více než 20 servolisů. (Zdroj obrázku: BSH Group)
Továrna v La Cartuja v současné době vyrábí především domácí spotřebiče pro zavedené značky, jako jsou Bosch, Siemens, Gaggenau a Neff. Španělská továrna, která má okolo 400 pracovníků, je součástí globální výrobní sítě 37 závodů s přibližně 60 000 zaměstnanci. Systém Smart Function Kit Pressing hraje důležitou úlohu v procesu globální standardizace, stejně jako globální působení společnosti Bosch Rexroth.„Systém Smart Function Kit se po fázi vyhodnocení ukázal jako nejvhodnější a cenově nejvíce efektivní řešení. Každé jeho nasazení je praktické zejména během nočních směn, kdy operátoři nemají přístup k technické podpoře,“ vysvětluje David Ochoa, procesní inženýr ve společnosti BSH.
Smart Function Kit Pressing šetří cenný inženýrský čas před uvedením do provozu v místě instalace. Pomocí inteligentních elektronických nástrojů od společnosti Bosch Rexroth lze provádět digitální návrh, konfiguraci a objednávání mechantronického subsystému z e-shopu Rexroth během několika minut. Po obdržení předmontovaného servolisu v jediném balení vás průvodce operačního softwaru na bázi prohlížeče provede jednotlivými kroky uvedení do provozu. Definice procesu probíhá vizuálně pomocí graficky uspořádaných modulů. Díky připraveným funkčním blokům je též rychle dokončována parametrizovaná linková integrace. Výsledek a procesní data lze zobrazovat přímo na ovládacím panelu a přenášet do jiných systémů přes různá rozhraní.
Systém Smart Function Kit Pressing šetří čas od fáze vývoje až po uvedení do provozu. Návrh, konfigurace a objednávání se provádějí výhradně digitálně, přičemž předinstalovaný operační software snižuje pracovní zatížení při uvádění do provozu, definování procesu a linkové integraci. (Zdroj obrázku: Bosch Rexroth)
Smart Function Kit Pressing je k dispozici pro síly v rozsahu 2–70 kN a pokrývá tři typické aplikace: umístění do pozice, silové spojení nebo silové spojení s následným přidržením. Těsnění je umístěno do určené pozice v závodě BSH ve městě La Cartuja. Pro tento účel se nejprve zalisuje do tělesa ložiska. Po zavedení stíracího těsnění do osy se lis během krátkého časového cyklu posune do předdefinované polohy specifické pro daný produkt.
Pokud technologie RFID detekuje novou variantu, řízení linky automaticky přenese do servolisu příslušné parametry, jako jsou dráhy, síly a tolerance.„Díky digitálnímu řízení procesů jsme schopni rychle reagovat na změny komponent,” vysvětluje Ochoa.„Opakovatelnost hloubky indentace se prokazatelně zlepšila. Na rozdíl od pneumatického polohování se obejdeme bez mechanických dorazů.”
Ucelená detekce síly a dráhy ihned identifikuje jakékoli chybně namontované těsnění a tento stav se pak zobrazí přímo ve stanici prostřednictvím operačního softwaru na bázi prohlížeče jako hlášení NOK. Data o kvalitě lze přenášet přes různá rozhraní. Aplikace BSH komunikuje systémem Smart Function Kit pomocí protokolu TCP/IP. Procesní data se dále přenášejí do cloudového serveru BSH jako soubory JSON.„Díky dosažené transparentnosti procesů můžeme nepřetržitě sledovat kvalitu, trvale monitorovat procesy a rychleji odstraňovat případné chyby,“ říká Aßmuth.„Mimo jiné vytváříme trendové analýzy definující přesné toleranční zóny procesů ve vztahu k návrhu nebo samotné součásti.“
Společnost BSH mezitím tuto úspěšnou koncepci expandovala na další místa v Polsku, Německu, Turecku, Indii a Číně. Během tří let bylo uvedeno do provozu 21 systémů Smart Function Kit Pressing. Druhý systém Smart Function Kit Pressing se často instaluje do novějších stanic, kde nastavuje danou součást do přesné nulové polohy odspodu, což umožňuje ještě přesnější činnost horního servolisu.
Elektrická koncepce také dosahuje mnohem lepších výsledků z hlediska udržitelnosti v porovnání s předchozími pneumatickými řešeními.„Postupnou elektrifikací dalších montážních operací a procesů můžeme nahrazovat zbývající pneumatické systémy. Jakmile dojde k vypnutí kompresorů, energetická účinnost linky se náhle zlepší,“ říká Aßmuth.
Technologický přechod na elektromechaniku je velkým úspěchem společnosti BSH. „Systém Smart Function Kit Pressing pracuje spolehlivě již od první minuty s více než 99 procenty součástí se stavem OK,“ hlásí Ochoa ze závodu La Cartuja. A Maximilian Aßmuth je též velmi potěšen kompletním mechatronickým balíčkem:„Díky inovativní koncepci řešení společnosti Bosch Rexroth jsme byli schopni celosvětově standardizovat důležité úlohy lisování a spojování způsobem, který je připravený na budoucnost. Ocenili jsme skutečnost, že náš partner v oblasti řešení byl též otevřený návrhům na zlepšení, z nichž některé byly ihned implementovány v následující aktualizaci softwaru. Takto úzká spolupráce s klientem rovněž významně přispívá ke společnému dosažení úspěchu v projektu.“