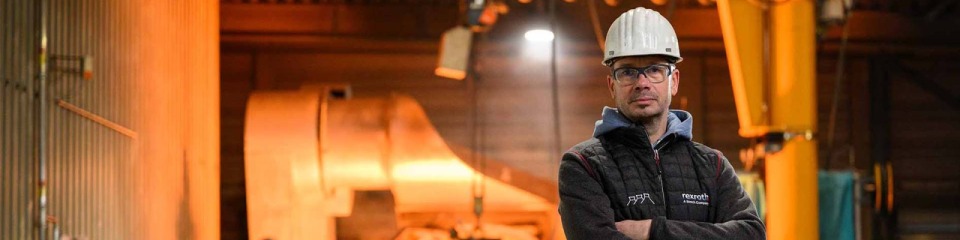
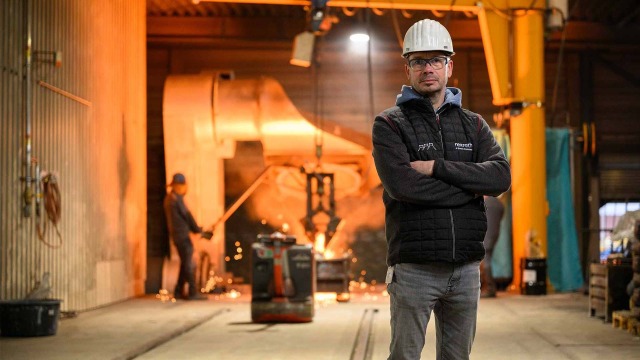
Hos Bosch Rexroth er vi konstant på udkig efter måder at spare energi på. Se nogle af de seneste innovationer, som vi har implementeret i vores anlæg verden over som gode eksempler på, hvordan det er muligt at bidrage til en øget energieffektivitet ved hjælp af en kreativ tilgang og omhyggelige analyser.
Nye måder at nedkøle på
I anlægget i Lohr i Tyskland producerer vi hydrauliktæt støbegods i flere forskellige kvaliteter af støbejern. En del af denne produktionsproces indbefatter en særlig varmebehandling kaldet "udglødning", hvor støbeemnerne opvarmes til over 900°C og derefter nedkøles i henhold til præcist definerede specifikationer.
Der bruges en enorm mængde energi til udglødning, men for nylig har vores eksperter fundet en mere energieffektiv måde at erstatte udglødning med langsom nedkøling på.
Vores nye kølehus giver os mulighed for at eliminere udglødningsprocessen, hvilket hjælper os med at reducere vores kuldioxidemissionerne fra vores støberi med mere end 2.500 tons om året. Dette har en direkte indvirkning på vores produkters kulstofaftryk.
(Billedrettigheder: Bosch Rexroth)
Reduktion af energiforbruget gennem modernisering af smelteprocessen
Vi har ligeledes installeret vores tredje nye mellemfrekvenssmelteovn på vores støberi i Lohr. Den nye ovn indbefatter topmoderne smelteteknologi, hvor alt er designet til at skabe en øget energieffektivitet. Dette gør det muligt at erstatte tre eksisterende ovne med denne nye ovn.
Ved at digitalisere og automatisere smelteprocesserne, omstrukturere materialestrømmen og reducere transporten af jern – og dermed det resulterende temperaturtab – reducerer vi vores energiforbrug yderligere. Det nye layout i vores smelteværksted gør det muligt for os at spare op til 2,9 GWh el om året.
(Billedrettigheder: Bosch Rexroth)
Skift til central vandkøling
Kompressorkølesystemer er en vigtig del af processen til produktion af hydraulikkomponenter i vores anlæg i Beijing. Disse systemer fungerer på samme måde som køleskabe eller klimaanlæg, der udsender varm luft, når systemet kører. Den varme luft skal fjernes via ventilationssystemet, hvilket betyder et højt energiforbrug.
Vores team overvejede, hvordan de kunne forbedre energistyringen, og så på det eksisterende koldtvandsnetværk i anlægget, som allerede bruges til at køle andre maskiner og processer med under produktionen. De fandt ud af, at energieffektiviteten kunne forbedres betydeligt ved at bruge dette eksisterende koldtvandsnetværk til at afkøle installerede maskinværktøjer. Kompressorkølesystemerne kan erstattes af en varmeveksler, der er forbundet til koldtvandsnetværket.
Vi implementerede det nye system i første fase, hvor fem bearbejdningscentre blev ombygget, hvilket resulterede i et reduceret energiforbrug til køling med over 80 % sammenlignet med den decentrale løsning, hvilket svarer til årlige besparelser på omkring 85.000 kWh.
(Billedrettigheder: Bosch Rexroth)
Produktion af printplader: energibesparelser med UV-stråling
På vores produktionsanlæg til printplader i Xi'an, Kina, hærdes kunstharpiks nu uden varme ved hjælp af UV-stråler, hvilket forbedrer anlæggets energibesparelsesmuligheder betydeligt.
Under produktionsprocessen samles printplader mekanisk med elektroniske komponenter og loddes. Efter funktionstestning belægges den samlede printplade med maling for at beskytte elektronikken mod påvirkninger udefra. Dette gør den egnet til brug i industrien.
Indtil for nylig blev denne belægning tørret ved temperaturer på omkring 100°C i 15-20 minutter, og derefter skulle de samlede printplader køle af i to timer. Men ved at bruge UV-teknologi kan produktionsteamet skabe en kemisk reaktion på få sekunder, hvilket sparer over 80 % af energiforbruget pr. printplade sammenlignet med den tidligere proces, og samtidig reduceres tørretiden med omkring 90 %. Herudover giver processen mulighed for at anvende et tykkere lag maling, hvilket betyder et højere beskyttelsesniveau og en bedre kvalitet af de producerede printplader.
(Billedrettigheder: Bosch Rexroth)
Leo Pototzky
Direktør, operationel bæredygtighed