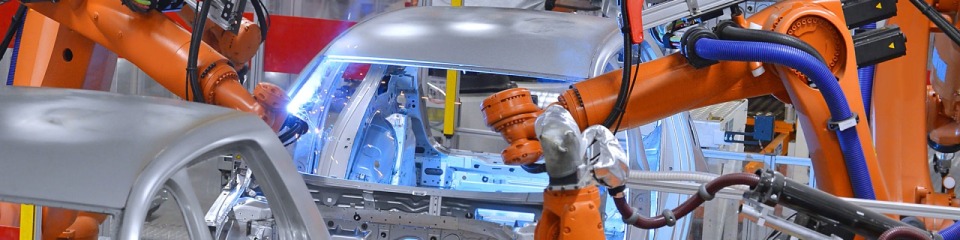
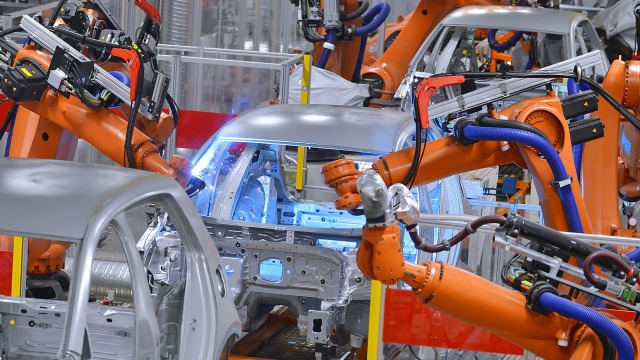
Als Innovationstreiber in der globalen Schweißindustrie steht Bosch Rexroth seit 60 Jahren immer wieder vor der Aufgabe, die Technologien fähig für die Anforderungen der Fabrik der Zukunft zu machen. Und auch diesmal ist es gelungen, einen Meilenstein im Bereich Widerstandspunktschweißen zu setzen: mit der neuen Schweißsteuerungsgeneration PRC7000. Bartosz Korajda, Vice President Resistance Welding bei Bosch Rexroth, bringt auf den Punkt, was sie so unverzichtbar und zukunftsfähig für verschiedene Branchen macht.
Herr Korajda, was sind die Herausforderungen im Bereich Widerstandspunktschweißen?
Die Widerstandspunktschweißtechnik erfreut sich nach wie vor großer Beliebtheit, wenn es um hohe Reproduzierbarkeit und Automatisierung in der Automobil- bzw. Fahrzeugbranche, aber auch in der blechverarbeitenden Industrie geht. Gleichzeitig ermöglicht sie eine sehr gute Qualität der Verbindungen. Mit anhaltenden Trends, wie zum Beispiel Leichtbau, wird das Verfahren in Bezug auf Prozessstabilität und Produktivität aber immer wieder vor neue Herausforderungen gestellt. Hinzu kommt, dass die Schweißsysteme auch in die Welt der zunehmend digitalisierten Fabriken passen müssen.
Womit punktet das Portfolio von Bosch Rexroth besonders?
Wir stellen kontinuierlich den Status-quo auf den Prüfstand und bieten dadurch ein durchdachtes und zukunftsfähiges Portfolio für Widerstandspunktschweißen. Unser Ziel ist es, dass unsere Kunden damit Wettbewerbsvorteile erzielen – und das können sie nur, wenn sie mit effizienten und zukunftsfähigen Lösungen arbeiten. Dafür sorgen wir unter anderem mit integrierten IoT-Schnittstellen, KI-fähigen Hardware-Komponenten und webbasierten Steuerungslösungen. Der Kunde kann sich bedarfsgerecht seine Systeme zusammenstellen, so dass er entweder eine Gesamtlösung aus Hard- und Software erhält oder einzelne benötigte Komponenten.
Unsere vielfältigen Lösungsansätze decken einen riesigen Bereich von sehr unter-schiedlichen Anwendungsfällen ab. Das reicht von der einfachen pneumatischen Zange mit Konstantstromregelung bis zur „Integrated Servogun Control“ mit Aluminium- und Stahlregler 2.0. Und auch hinsichtlich Erweiterungen sind wir bestens aufgestellt. Neben den neusten IoT-Anforderungen wie MQTT und OPC UA bieten wir ein breites Spektrum an unterschiedlichen Feldbussen und eine sehr moderne Softwarearchitektur, die sich schnell bedarfsgerecht erweitern lässt.
Inwiefern wird hier ein ganzheitlicher und gleichzeitig modularer Ansatz erfüllt?
Bei unseren Lösungen verfolgen wir zum einen stringent ein modulares Hardware-Konzept. Das betrifft die verschiedenen Leistungsklassen, die Kühlkonzepte sowie die Einspeisekonzepte mit unterschiedlicher Spannung. Zum anderen ist unser Softwarekonzept modular gestaltet, so dass durch Erweiterungen schnell auf neue Anforderungen am Markt reagiert werden kann. Ein großer Vorteil für unsere Kunden ist dabei der „Pay what you need“-Ansatz. Unser Lizenzierungssystem ermöglicht es, nur die Software zu erwerben, die auch wirklich benötigt wird.
Schweißen ist nicht gleich Schweißen. Wie können Sie alle Anforderungen abdecken?
Das stimmt. Zum Beispiel bestehen Unterschiede zwischen Aluminium- und Stahl-schweißaufgaben. Transformatoren können aber die Ausgangsleistung der Schweißsteuerung passgenau für die jeweilige Schweißaufgabe umwandeln. Die Zangenspeicher bieten in unserer neuesten Ausbaustufe die Möglichkeit, die Prozesssignale bereits auf der Zange zu digitalisieren. Beispielsweise können Handzangen an jeder verfügbaren Steuerung betrieben werden, ohne dass die Steuerung dazu parametriert werden muss. Die Daten werden dafür in Form einer vollständigen Schweißaufgabe direkt auf dem Zangenspeicher gespeichert und können störgemindert an die Steuerung übermittelt werden. So ermöglichen wir unseren Kunden neue Use-Cases, die zu mehr Handlungsspielraum und Kosteneinsparungen führen.
Mit der PRC7000 hat Bosch Rexroth eine neue Schweißsteuerungsgeneration auf den Markt gebracht. Inwiefern setzt sie neue Maßstäbe?
Diese leistungsstarke Schweißsteuerungsgeneration ist die Antwort auf viele Fragen, die die Industrie aktuell stellt. Das System bietet maximale Qualität beim Schweißen von Stahl oder Aluminium. Mit adaptiven Reglern und flexibler Program-mierbarkeit können unterschiedliche Blechdickenkombinationen sowie Materialmixe problemlos verarbeitet werden. Außerdem werden perfekte Schweißpunkte endlich reproduzierbar. Der integrierte IoT-Connector stellt zudem strukturiert Daten zur zentralen Verarbeitung, Qualitätsüberwachung und Technologiedatenverwaltung bereit. Damit ist die PRC7000 bestens gerüstet für die Anforderungen der Industrie 4.0.
Wie erfüllt die Lösung im Detail die Anforderungen der Fabrik der Zukunft?
Als erster Anbieter haben wir MQTT und OPC UA vollständig in unsere Steuerung integriert. Dieser Schritt ist wesentlich, um mögliche neue Use-Cases abzubilden. Ein weiteres großes Thema ist die Verfügbarkeit von Daten. Diese verwerten wir ge-winnbringend für unsere Kunden. Erste Anwendungen wie die „Adaptive Spatter-control“ haben wir bereits in unsere Steuerung implementiert.
In den vergangenen Jahren waren wir auf den Automobilbereich fokussiert. Unser Blick richtet sich mittlerweile zunehmend auf weitere Märkte, da unsere neue Software-Architektur uns befähigt, auch klassische Anwendungen des Maschinen-baumarktes zu bedienen.
Welche Vorteile hat der Kunde bzw. Anwender, wenn er auf Schweißsysteme von Bosch Rexroth setzt?
Ein großes Plus ist die hohe Skalierbarkeit unserer Systeme. Der Kunde hat die Auswahl zwischen 15 Lizenzen und kann seine Lösung bedarfsgerecht nach der bereits erwähnten zukunftsträchtigen “Pay what you need“-Methode konfigurieren.
Ein deutlicher Vorteil liegt auch in den Einsparpotenzialen, die sich beispielsweise mit der Anwendung „Adaptive Spatter Reduction“ bieten. Kunden haben fast immer eine maximale Spritzerquote. Diese wird durch die Kunden heute manuell optimiert – zukünftig geschieht dies mit unserem Automatismus „Adaptive Spatter Reduction“. Zur Reduzierung von Arbeit und Kosten tragen auch die neuen Einlernprozesse bei, die nicht in der Serienlinie, sondern im Labor erfolgen.
Schließlich sind auch die Qualitätsvorteile signifikant. Mit der „Integrated Servogun Control“ können wir neben den klassischen elektronischen Signalen auch zahlreiche mechanische Signale aufzeichnen. Dadurch lassen sich Überwachungen ableiten und Detektionen von Störgrößen identifizieren. Mit adaptiven Steuerungen ist der Schweißprozess so gestaltbar, dass alle auftretenden Störgrößen bestmöglich überwunden werden. Wir können mit ihnen aber nicht nur erfolgreich regeln, sondern auch klare und passgenaue Überwachungsaussagen treffen.
Was ist Ihre Antwort auf die künftigen Anforderungen der Zielbranchen?
Der Trend geht eindeutig dahin, dass die anspruchsvollen Schweißaufgaben durch Mischkombinationen und unterschiedliche Varianten zunehmen. Das dafür benötigte Know-how entwickelt sich analog dazu jedoch sowohl im Steuerungs- als auch Schweißprozess auf Anwenderseite nicht mit. Im Automobilsektor werden darüber hinaus immer mehr Fahrzeugvarianten über die gleiche Linie gefahren. Dies alles nimmt direkten Einfluss auf die Inbetriebnahme und die Anforderungen an Regelung und Überwachung.
Um diese stetig komplexer werdenden Aufgaben zu lösen, verfolgen wir das Ziel, das System permanent weiter zu vereinfachen. Indem wir immer mehr Automatismen in unser System integrieren, kann sich dieses im Zielbild bald vollständig autonom verhalten. Außerdem beziehen wir zunehmend Komponenten der Automatisierungsplattform ctrlX AUTOMATION von Bosch Rexroth mit in die Konzepte ein. Mit all diesen Stellschrauben und stetiger Weiterentwicklung machen wir die Schweißtechnologie anschlussfähig für die Anforderungen der Fabrik der Zukunft und stärken unsere Kunden für die neuen Herausforderungen – das schweißt zusammen.