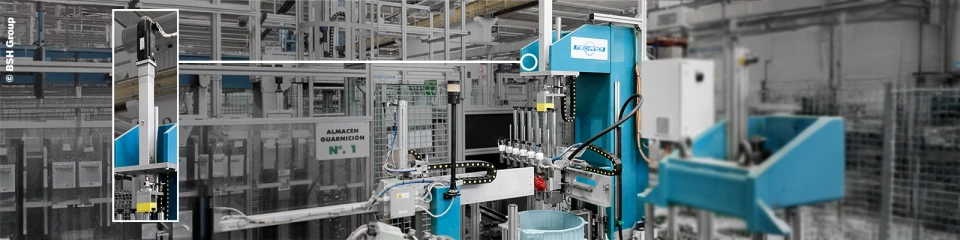
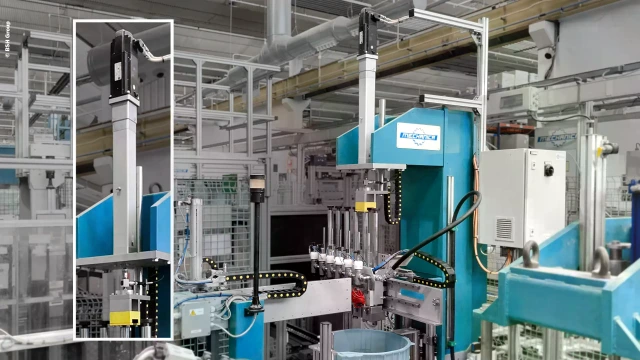
The BSH Group standardizes pressing and joining processes critical to quality in washing machine production. How? With the Smart Function Kit Pressing mechatronic subsystem. The result: more flexibility, stability, and transparency with minimal time required for engineering, integration, and quality control.
For Maximilian Aßmuth of the Laundry Care Industrial Engineering Team at BSH, the newly introduced electromechanical servo presses based on Smart Function Kit Pressing have a crucial advantage over the pneumatic solutions used up to now. They enable highly precise processes, save energy, and provide a reliable basis for quality assurance and further process optimization. Why? Because the electromechanical servo presses convert the electrically generated torque directly into movement via the screw drive in the electromechanical cylinder EMC, finely control it, and precisely capture the process data using sensors and software. It is these advantages that BSH leverages to make the processes in the global production network more economical.
Maximilian Aßmuth
Laundry Care Industrial Engineering Team at BSH
The international standardization project was launched with the first Smart Function Kit Pressing for the plant in La Cartuja near Zaragoza, Spain. The mechatronic solution consists of an electromechanical cylinder with force sensor, a servo motor with servo drive and an industrial PC with pre-installed operating software. In washing machine production, the smart servo press is used to reliably fix a critical seal between the drum shaft and water container that holds the water in the machine. Thanks to the pre-assembled complete package and good preparation, the project was quickly a success. After just three days, including a test run, the powerful combination of press-fit technology, software, and service was reliably put into operation.
The first Smart Function Kit Pressing at BSH went into operation at the La Cartuja plant near Zaragoza in 2021. More than 20 servo presses are now in operation worldwide. (Image source: BSH Group)
Nowadays, La Cartuja mainly produces household appliances for well-known brands such as Bosch, Siemens, Gaggenau, and Neff. The Spanish location with around 400 employees is part of the global production network of 37 plants with roughly 60,000 employees. The Smart Function Kit Pressing plays an important role in process standardization, as does Bosch Rexroth’s global presence. “After the evaluation phase, the Smart Function Kit turned out to be the most suitable and cost-effective solution. Ease of use is particularly practical during night shifts when operators do not have access to technical support,” explains David Ochoa, process engineer at BSH.
Smart Function Kit Pressing saves valuable engineering time even before commissioning on site. Using the intelligent e-tools from Bosch Rexroth, the mechatronic subsystem can be digitally designed, configured, and ordered through the Rexroth shop in a matter of minutes. Following the pre-assembled delivery of the servo press in one package, the browser-based operating software’s wizard guides you through the commissioning process step by step. Process definition takes place visually using modules which are graphically arranged and parameterized line integration is also completed quickly thanks to prepared function blocks. The result and process data can be visualized directly in the dashboard and transferred to different systems via various interfaces.
Smart Function Kit Pressing saves time from engineering to the operational phase. Design, configuration, and ordering are purely digital, while the pre-installed operating software reduces the workload for commissioning, process definition, and line integration. (Image source: Bosch Rexroth)
Smart Function Kit Pressing is available in the force range from 2 to 70 kN and covers three typical applications: join to position, join to force, or join to force with subsequent holding. The seal is joined to position at the BSH plant in La Cartuja. For this purpose, it is first pressed into the bearing housing. After the wiper seal has been fed to the axis, the press moves to the product-specific predetermined position within a short cycle time.
If a new variant is detected by RFID, the line control automatically transfers the relevant parameters such as paths, forces, and tolerances to the servo press. “Thanks to the digital control of the process, we can react very quickly to component changes,” explains Ochoa. “The repeatability of the indentation depth has clearly improved. Unlike with pneumatic positioning, we can do without mechanical stops.”
The consistent force and path detection instantly identifies any incorrectly mounted seal and displays this directly at the station via the browser-based operating software as an NOK message. Quality data can be transferred via various interface. The BSH application is connected to the Smart Function Kit via TCP/IP. In addition, the process data is also transferred to the BSH cloud server as JSON files. “Thanks to the process transparency gained, we can continuously monitor the quality, constantly improve processes, and eliminate possible errors more quickly,” says Aßmuth. “Among other things, we create trend analyses to define precise tolerance zones for the process in relation to the design or the part itself.”
In the meantime, BSH has expanded the successful concept to other locations in Poland, Germany, Turkey, India, and China. Within three years, 21 Smart Function Kit Pressing were put into operation. A second Smart Function Kit Pressing is often installed in newer stations, which brings the component to the exact zero position from below, allowing the upper servo press to work even more precisely.
Compared to previous pneumatic solutions, the electrical concept also scores points in terms of sustainability: “We can gradually replace the remaining pneumatic systems by successively electrifying more assembly operations and processes. As soon as the compressors are switched off, the lines’ energy efficiency suddenly improves," says Aßmuth.
The technology changeover to electromechanics is a complete success for BSH. “The Smart Function Kit Pressing has been working reliably from the very first minute with over 99 percent OK parts,” Ochoa reports from the La Cartuja plant. And Maximilian Aßmuth is also very pleased with the mechatronic complete package: “Thanks to Bosch Rexroth’s innovative solution approach, we have been able to standardize important pressing and joining tasks worldwide in a future-proof manner. We liked the fact that our solution partner was also open to suggestions for improvements, some of which were implemented right away in the next software update. Working so closely with the customer also contributes significantly to the joint success of the project.”