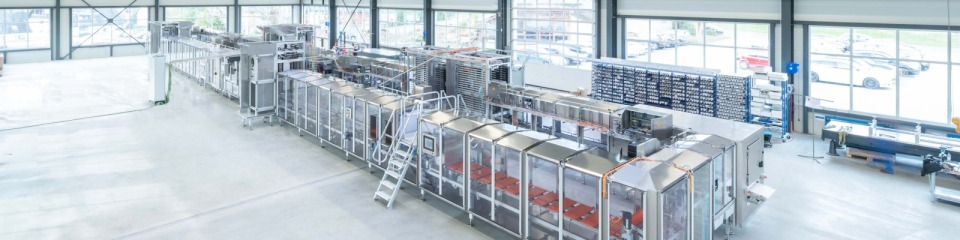
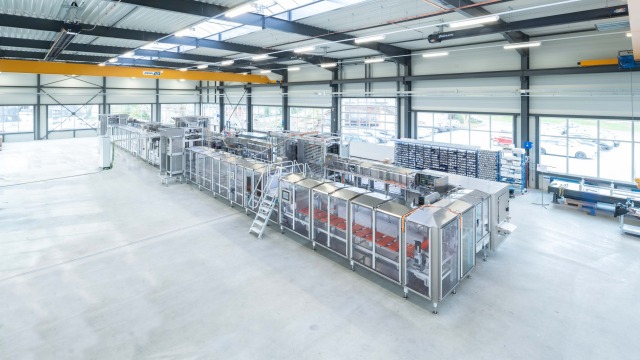
In many industries, digitalization is leading to new impulses in terms of innovation and efficiency, including in the confectionery industry. Digital technologies are changing production processes, enabling data-driven decisions and simplifying the maintenance of complex machines. Bernd Plies from Winkler und Dünnebier Süsswarenmaschinen (WDS) explains how his company masters the requirements for efficiency and transparency through digitization and platform strategies. The SweetConnect platform, developed together with partner companies, demonstrates how digital networking is setting new standards in a traditional industry.
Digitalization in the confectionery industry involves more than the introduction of new technologies. It leads to a fundamental change in work processes. Production facilities are usually geared to specific requirements and are used over a period of several years. The implementation of digital assistance systems optimizes processes, reduces maintenance costs and increases productivity. However, the use of digital technologies in the industry is still in its infancy. "Many production companies rely on semi-skilled workers who take on basic tasks but do not have the necessary expertise for maintenance," explains Bernd Plies.
SweetConnect is at the heart of WDS' digital strategy. This platform acts as a central portal that records all production and machine data of a plant in real time. The modular design allows customers to integrate apps and services as needed. This flexibility is particularly attractive for medium-sized companies that want to control their costs of digitization.
Bernd Plies underlines: "SweetConnect offers customers the opportunity to manage their entire production line via a dashboard." This facilitates maintenance and troubleshooting and provides an overview of the efficiency of each machine.
The use of production data is crucial for the success of digital strategies. In practice, there are often concerns about data security, but there is an increasing willingness to share data. SweetConnect’s "Customer Cockpit" provides customers with comprehensive insights into their production processes. This allows interference factors to be identified and production to be optimized. "The Customer Cockpit provides operators with an overview of machine parameters and helps to identify and remedy bottlenecks at an early stage," adds Bernd Plies.
Digitalization also offers a solution for dealing with the shortage of skilled workers. Digital assistance systems and automated processes reduce the workload and reduce the dependency on specialist personnel. SweetConnect offers integrated maintenance and inspection systems with features such as remote monitoring and predictive maintenance planning. As a result, unplanned downtimes and downtimes can be reduced to a minimum. This relieves the companies and ensures the maintenance of operations even in times of a shortage of skilled workers.
The digitalization and platform strategy of WDS and its partners is an important step into the future of confectionery production. SweetConnect increases the efficiency and transparency of the production line and meets the requirements of the digitized industry. Companies benefit from more flexible and efficient operations, which are key success factors in a rapidly changing market. The examples of WDS illustrate that digitization can transform the confectionery industry in a sustainable way.
WDS is one of the world’s leading manufacturers of confectionery machines. As a specialist for moulding lines, they are able to cover the entire spectrum of cast confectionery with different application and performance ranges. Learn more about the company.
These and other episodes from different topics can be found in our tech podcast channel "Industrie neu gedacht" or on all known platforms.
You want to listen to the episode directly?
Interview guest:
Bernd Plies
Position:
former Head of Digitalization,
Winkler und Dünnebier Süßwarenmaschinen (WDS)
Already connected on LinkedIn?
Bernd Plies
Always stay up to date:
Bosch Rexroth AG
Contact person tech podcast:
Susanne Noll