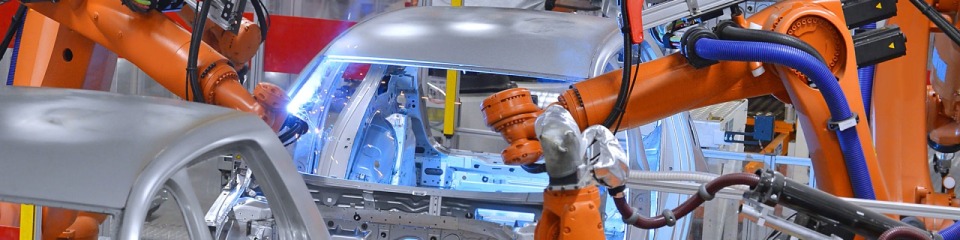
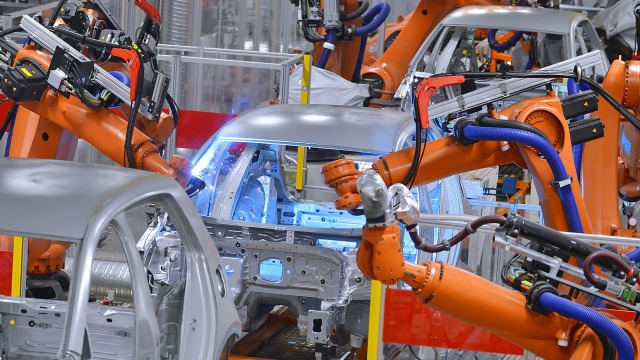
For the past 60 years, Bosch Rexroth, an innovabon driver in the global welding industry, has repeatedly faced the task of making technologies fit the requirements of the Factory of the Future. And once again, a milestone has been achieved in resistance spot welding – with the new welding control generation PRC7000. Bartosz Korajda, Vice President Resistance Welding at Bosch Rexroth, explains in a nutshell what makes it so indispensable and future-proof for various industries.
Mr. Korajda, what challenges does resistance welding present?
Resistance welding is still as popular as ever when it comes to reproducibility and high automation in the automotive sector, but also in the sheet metal working industry. Plus, it enables high quality welding joints. With persistent trends such as lightweight construction, processes relating to process stability and productivity continuously face new challenges. What’s more, welding systems must also fit into the world of increasingly digitalized factories.
What’s special about Bosch Rexroth’s portfolio?
Because we never stop questioning the status quo, our portfolio for resistance welding is well thought-out and future-proof. Our goal is to enable our customers to achieve competitive advantages, which they can only do if they work with efficient and future-proof solutions. We do so with integrated IoT interfaces, AI-enabled hardware components and web-based control solutions, among others. Customers can assemble their systems either as an overall solution with hardware and software, or they can purchase only the individual components they require.
Our versatile solutions cover a vast area of very different application cases, ranging from the simple pneumatic gun with constant current control to integrated servogun control with aluminium and steel controllers 2.0. And we are also well positioned in terms of expansions. In addition to the latest IoT requirements such as MQTT and OPC UA, we offer a wide spectrum of different fieldbuses and a highly modern software architecture that can quickly be expanded to meet individual requirements.
To what extent does this fulfill a holistic yet modular approach?
Our solutions follow a strictly modular hardware concept. This applies to the various power classes, cooling concepts and feed-in concepts with different voltages. But our software concept is also modular so that we can respond quickly to new market requirements with expansions. One big advantage for our customers is the “only pay for what you need” approach. Our licensing system allows our customers to limit their purchase to the software they really need.
Welding spans such a broad spectrum. How can you cover all requirements?
That's true. For example, aluminium and steel welding tasks differ. However, transformers can convert the output power of the welding controller precisely to suit the welding task at hand. In our latest expansion stage, the gun data module offers the possibility of digitalizing the process signals on the gun. For instance, manual guns can be operated with all available controls without having to parameterize the controller. The data is stored directly in the gun module as a complete welding task and can then be transmitted to the control system with reduced interference. This makes more new use cases available to our customers, which leads to more flexibility and cost savings.
With the PRC7000, Bosch Rexroth has brought a new welding control generation on the market. To what extent does it set new benchmarks?
The powerful new welding control generation is the answer to many questions the industry is currently asking. The system offers maximum quality for welding steel or aluminium. Adaptive controllers and flexible programmability allow for easy processing of different sheet thickness combinations and material mixes. And at last, perfect weld seams are reproducible. The integrated loT connector also provides structured data for central processing, quality control and technology data management, so that the PRC7000 is ideally equipped for the requirements of Industry 4.0.
How does this solution fulfill the requirements of the Factory of the Future in detail?
We are the first provider to offer MQTT and OPC UA fully integrated into our control system. This is a must for mapping possible new use cases. Another major topic is data availability, which we use profitably for our customers. We have already implemented the first applications such as Adaptive Spatter Control in our control system.
In the past, we focused on the automotive sector. In the meantime, we are increasingly looking at other markets, as our new software architecture enables us to serve classic applications in the mechanical engineering market as well.
What advantages do customers or users stand to gain if they opt for Bosch Rexroth welding systems?
Our systems are highly scalable. That is a big plus factor. Customers can choose from 15 licenses and can configure their solutions to match their needs with the future-oriented “only pay for what you need” method I mentioned earlier.
One major advantage is the savings potential that applications such as Adaptive Spatter Reduction offer. Customers almost always have a maximum spatter rate, which they currently tend to optimize manually. In future, this can be done with our Adaptive Spatter Reduction automatism. The new learning processes, which take place in the lab rather than on the production line, also help to reduce labor and costs.
Finally, there are significant quality advantages, too. With the Integrated Servogun Control, we can record numerous mechanical signals as well as the classic electronic signals. This facilitates monitoring derivations and the detection and identification of disturbance variables. With the adaptive control system, the welding process can be designed specifically to overcome all occurring disturbance variables in the best possible way. We can not only successfully control with them, but also make clear and accurate monitoring statements.
What is your response to the future requirements of target industries?
The trend is clearly moving toward a rise in sophisticated welding tasks due to mixed combinations and different variants. The requisite expertise develops at the same time, but this does not apply to users for both control and welding processes. In the automotive sector, more and more vehicle types are being produced on the same production line. This all directly influences the commissioning as well as the control and monitoring requirements.
In order to solve these increasingly complex tasks, our goal is to continuously simplify the system. By integrating more and more automatisms in our system, our mission is that it will soon be able to behave completely autonomously. We are also increasingly incorporating components of the Bosch Rexroth ctrlX AUTOMATION platform in the concepts. With all these mechanisms and continuous further development, we are aligning welding technology with the requirements of the factory of the future and strengthening our customers for new challenges -– that's what welds us together.