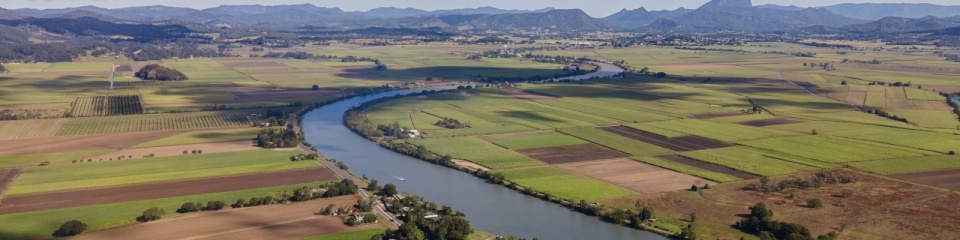
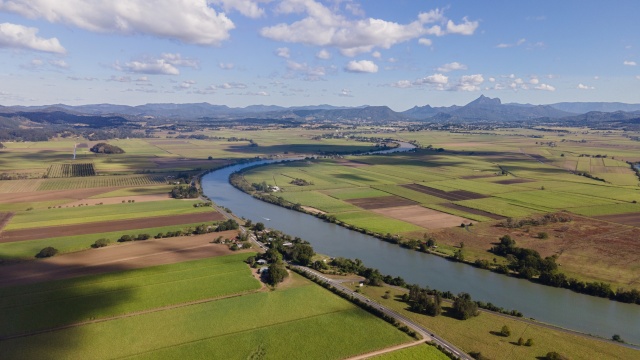
Powerful Hägglunds assistance after damaging floods
Situated in New South Wales, Sunshine Sugar is a partnership between the family-owned Manildra Group and the grower-owned NSW Sugar Milling Co-operative. Between its sites in Harwood, Condong and Broadwater, the company crushes around 2 million tons of cane yearly. As the only company to mill sugar in the state, it faces unique challenges from the start.
“Here in New South Wales, we work mainly with two-year-old cane. That makes us more sensitive when things like major weather events happen. Because we have a two-year crop cycle, it takes two or three years to recover,” says Mark Campbell, Engineering Manager at the Broadwater mill.
That sensitivity was painfully clear in March 2022, when catastrophic floods swept through New South Wales. Sunshine Sugar sustained around 43 million Australian dollars of damage – well over half of it in Broadwater alone. At all three of the company’s sites, Hägglunds drive systems that power the mill rollers were submerged.
Hägglunds drives have been used at Sunshine Sugar since the early 1990s. Major upgrades were made into the early 2000s, which included putting Hägglunds direct drives on three of the four mills in Broadwater. The change was motivated by the cutting-edge advantages that hydraulic drives offer over electromechanical systems, which include high torque at low speed and unprecedented speed control.
Since then, Sunshine Sugar has seen other benefits. “We’ve had these drives for over 20 years now, and the main thing for me is the service,” says Campbell. “The Hägglunds team have been very good in terms of response. If I call at three o’clock in the morning with an issue that I can’t resolve, there’s always someone who answers. And they’ll come down if they need to.”
Little did the team at the Broadwater mill know how much they would appreciate that responsiveness in 2022.
Though it lies on the bank of the Richmond River, the Broadwater mill is situated in a flat area where flooding is uncommon. Ironically, the mill had implemented a new emergency flood plan just one month before the heavy rains started. Designed to protect against a 1:100 flood level of 4.6 meters above normal, it still proved insufficient. In the end, the water rose by 6.2 meters – nearly 2.5 meters above the level where it enters the mill.
Passing over fences and other barriers, the water penetrated well into the elevated sugar shed. Vessels were moved, and a massive molasses tank was lifted from its foundations and rendered unusable. The Hägglunds drive systems, whose closed design could have protected against the worst, were hit hard due to maintenance happening at the time.
“We had everything pulled apart and open, so we copped it a lot harder than we needed to,” says Campbell. “We’d actually moved the motors across the road, which is the highest ground we have. We thought that would be safe, but we lost all the motors that we put over there in the last minute. We weren’t expecting anything of this magnitude.”
With all 12 Hägglunds motors and a number of hydraulic drive units submerged, Broadwater was most impacted. But things were little better for Sunshine Sugar elsewhere. In Harwood and Condong, an additional four Hägglunds motors, two hydraulic couplings and a long, custom-built torque arm also went underwater.
“I guess we always feel that we’ll recover, but it’s a question of how long it’s going to take and how much pain we have to go through,” says Campbell, reflecting on his feelings as the water subsided. “Our insurers have disaster management people who were there to guide us. But I knew exactly who to go to for the hydraulics: Bosch Rexroth. Essentially, we told them to come down, make an assessment and give us a plan to repair.”
Ben Hawkins, who heads the Hägglunds service team at Bosch Rexroth in Brisbane, was among the first on the scene. “I went down and observed the damage along with Matthew Perchard, who manages aftermarket development, and Mark Blake, one of our drive sales engineers,” he says. “Basically, the Broadwater mill had lost everything. From there we started working out quotes, and within around three months we’d restored it all.”
Campbell is still astonished by how fast it all went. “They said they needed all the drives and cabinets back, so they got trucks down and we loaded it up for them,” he relates. “Then they just took it all back to their workshop and shuffled around what they could to make it happen in the time frame.”
Of course, the reality of those months was far more complex, especially with so much equipment across three sites. Nearly every motor from Broadwater – a mix of Hägglunds CB and older Hägglunds Marathon motors – had to be carefully rebuilt by the workshop technicians. Where this was not possible, new Hägglunds CB or Hägglunds CBm motors had to be ordered from the factory in Mellansel, Sweden. This was the case for all the affected motors from Harwood.
“We couldn’t have done this alone,” saws Hawkins, who praises the team in Mellansel for working to slash lead times. “They were dispatching whole motors straight out of the factory, nine days from when we ordered them. From there it was just the air freight to Australia. I don’t know how you even achieve that!”
Similar efforts were made to restore the drowned control systems. These had been based on very old Jupiter cards, which the mill had been able to refurbish and keep going over the years. When they proved impossible to recover, seven new Hägglunds Spider control units were sourced from Mellansel in record time – despite component shortages stemming from the Covid-19 pandemic.
As for the affected pumps, arranging for rebuilds was even more demanding. Parts for the Rexroth pumps were readily available, but Broadwater had many older third-party pumps. Because the manufacturer’s own seal stocks had been depleted, the Hägglunds team went straight to the sub-supplier, arranging for seals to be custom-made.
On top of it all, there was the issue of feet on the ground. Besides having motors, control systems and seals shipped to New South Wales, labor had to be imported to manage the extensive work. Not only did the equipment need to be refurbished and installed, the new control systems also had to be integrated, replicating the mill-specific routines that had arisen through years of manipulating Jupiter cards.
“We contacted the team in Sweden with a dream of them sending a couple guys out, because we had our normal workload to handle simultaneously,” Hawkins relates. “Three people came from Sweden to help us for four weeks, and we had people flown in from New Zealand, plus backup from Sydney and other branches in Australia. It was a lot of stress from start to finish, but having the full support from our field service technicians on site was unbeatable – and the customer got exactly what they needed.”
Campbell most certainly agrees. “We’ve worked with Hägglunds service for many years, so I was confident that the team would deliver,” he says. “I think they had to drag a few people out of retirement, but they managed to pull it off!”
With the repair work now behind them, Sunshine Sugar can focus on business recovery. The refurbishments, and in some cases upgrades, were unplanned and acute. But Campbell finds it easy to see the bright side.
“This has given us a shot in the arm,” Campbell says. “Our Hägglunds drives were 20 years old, but the work we’ve done has set us up for smooth running and added a decade to their life. With the reports Bosch Rexroth has given us, we can better plan our maintenance over the next five to ten years, because we know what issues we need to address.”
The coming year especially, will be a tough one. Yet, as Sunshine Sugar deals with its mud-logged cane, Campbell is taking it in stride. “I’ve got peace of mind,” he says. “Nothing has really given us problems this far into the season. As long as our equipment keeps going, it makes our life easier!”
Fire, Floods and Drought. The Australian weather is demanding but crews like ours, Sunshine Sugar & Hägglunds show the environment how resilient we can be. Discover the story of how we worked with our teams around the globe to get Sunshine Sugar back up and running in time for the harvesting season after the devastating floods of 2022.