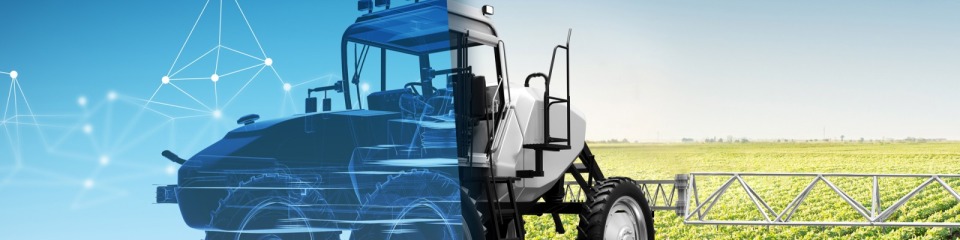
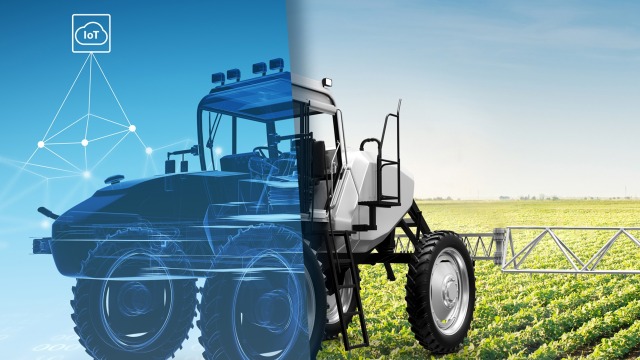
Telematics solutions for construction and agricultural machines are only as good as their weakest link. Off-highway players should bear in mind these five points when collecting data.
Anyone who would like to prepare vehicle data for fleet managers, contractors or support staff needs to collect the data first. How efficient and future-proof the entire telematics solution will be is decided here at the start of the information chain. The Telematics Control Unit is therefore the first point on our checklist.
Transferable device software has another advantage: The manufacturers can not only manage and update it themselves – it can also be expanded as required with specific software modules, for example manufacturer-specific algorithms for edge analytics. The device software for the Rexroth Connectivity Unit offers OEMs a protected area for this. Thanks to full support for standard interfaces, most of the common programming languages are supported. This ensures ample room for maneuver, protects know-how and guarantees portability in the event of a change in hardware.
Once device connectivity and management are clarified, the next step is data management, an area which allows considerably more room for maneuver. Vehicle data now appear on the interface in a manner geared to the needs of target groups. They are visualized before being passed on to user-specific portals. Fleet managers and workshops need a customer portal, while customer services need a service portal, each with suitable dashboards. When it comes to setting these up, companies once again need to decide whether to program them themselves, have them programmed by somebody else or adapt ready-to-use modules. In order to ensure maximum flexibility, an open telematics solution should cater for all these scenarios. This is possible within the BODAS Connect ecosystem as device and data management are logically separate from each other.
Using a complete package including data management is particularly beneficial in terms of time to market. After all, the requirements regarding data management are highly complex given the many peculiarities of the off-highway sector. This quickly becomes clear when it comes to data storage, storage costs, analytics and cloudtocloud communication. In order to enable companies to start providing their own IoT services quickly, Bosch Rexroth offers not only the basic BODAS Connect Device Connectivity package but also the BODAS Connect All-in-one-Connectivity end-to-end telematics solution. In addition to connectivity, edge analytics and device management modules, it includes a data management module as well. Its configurable modules and data interfaces allow companies to set up individual front ends with their own look and feel quickly. OEMs thus not only enjoy a high level of standardization – they also have considerable freedom when it comes to developing their services and can enter the market more quickly.