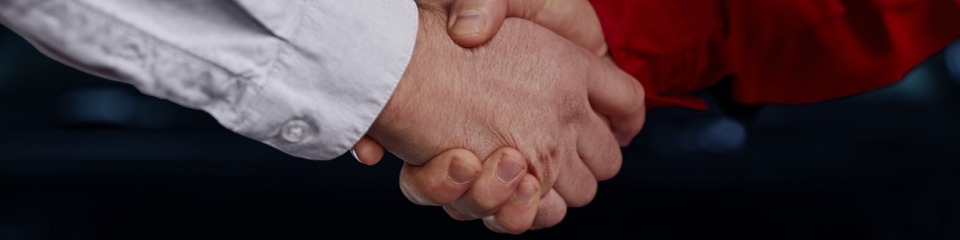
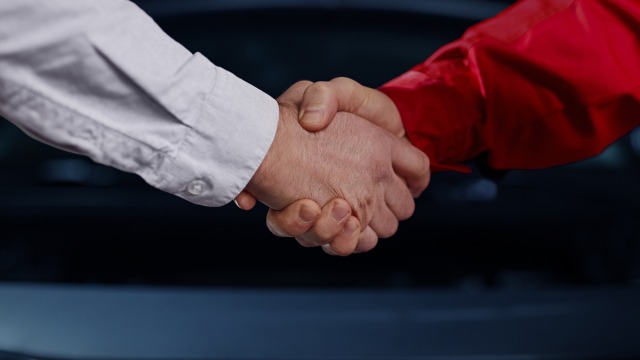
The automotive sector is dominated by the demand for ever lighter vehicles with sophisticated designs and high crash performance under intense cost pressure. In addition, new products are coming onto the market at increasingly shorter intervals. The commissioning and retooling phases in production are becoming shorter and more frequent. All of this is combined with less and less in-house expertise, driven by the shortage of skilled workers. This change also increases the complexity of resistance spot welding. Bosch Rexroth therefore offers functional bundles to provide assistance. For example, welding processes in for the body in white are simplified so that they can be carried out easily by both skilled and unskilled operators.
From flying sparks to precision craftsmanship – resistance spot welding has become an indispensable technology in the automotive industry. And the demands are constantly increasing. Companies want to produce faster, more efficiently and more cost-effectively without compromising on quality. At the same time, complexity is increasing, for example in lightweight construction. This requires specialist knowledge. Or is it possible to achieve the goals without special expertise within your company?
As a provider of control and drive technology, Bosch Rexroth continuously examines market requirements and offers new solutions to challenges such as the shortage of skilled workers. Since trained specialists for the future tasks in resistance spot welding are few and far between, Bosch Rexroth offers productive and simple solutions for all: The “Productivity” and “Simplicity” functional bundles, which are designed for the PRC7000 welding control system.
The “Dynamic Squeeze Time” and “Adaptive Spatter Reduction” software components are part of the “Productivity” license package. Both simplify resistance spot welding, for example for the body in white construction of passenger cars. These two functions result in higher productivity, quality optimization and reduced workload for users.
“Dynamic Squeeze Time” reduces the squeeze time depending on force and position. The feature can only be used in conjunction with the 7th axis function. The overall result is reduced squeeze time and increased productivity by shortening the production process. This means that with the same number of systems or welding controllers, more spot welds can be made in the same time and thus more cars produced.
“Adaptive Spatter Reduction” also focuses on savings and supports welding parameter optimization during the commissioning phase and series production of the car. Welding parameters are automatically optimized in terms of quality and spatter rate, as well as energy efficiency and threshold values. The function can be used, for example, to automatically detect and minimize weld spatter within a predefined tolerance range. Considerable savings can be achieved by using this function: The work required for optimization and post-processing, which would otherwise have to be carried out manually, is significantly reduced. It thus dispenses with the need for welding specialists, which many manufacturing companies simply do not have within their ranks or cannot find on the labor market. Only the PRC7000 welding control system from Bosch Rexroth offers this feature.
The functions of the “Simplicity” licensing package are aimed at simplifying processes. Currently, two components make up the product: “Web PRI” and “Auto Reference Curve Creation”.
Web PRI is a web-based user interface, which is accessed, for example, using a standard Internet browser, and which has a particular focus on simple and intuitive usability. It offers advantages over the classic PRI, especially for untrained users. The classic PRI offers all options for commissioning and operating the PRC7000 welding controls from Bosch Rexroth. It is designed for all applications – from those carried out by unskilled operators to those performed by specialists. This broad spectrum, however, naturally requires compromises.
The new Web PRI feature is designed for use on mobile devices, such as tablets, and is intended to simplify processes. Users are provided with an intuitive interface that offers many advantages, such as the ability to quickly find and operate specific functions. Professionals can also continue to use the existing PRI software for the PRC7000.
The Auto Reference Curve Creation functionality addresses two important capabilities of the PRC7000 welding controller: adaptive control and monitoring. For these, control curves must initially be recorded and activated. Until now, this required a high level of domain knowledge. This procedure can now be automated, which reduces the time and work required and may even improve the result. Users have the option of having new reference curves generated semi-automatically for individual or all spot welds.
Bosch Rexroth is successively expanding the “Productivity” and “Simplicity” license packages to include additional functions. The first add-on that is planned is “Auto Monitoring Curve Creation”. This will generate the corresponding monitoring curve in line with the automated generation of the reference curves. Further features are set to follow.
There is the option to use the products or the licenses with the already installed base of the PRC7000, through subsequent licensing. Bosch Rexroth regularly enhances the PRC7000 with new functionalities, which can be licensed as and when they are needed. Thanks to the modular software concept, users can install expansions at any time, license functions as needed, and thus respond quickly to market changes.
The shortage of skilled workers in the automotive market is omnipresent. At the same time, domain knowledge is indispensable in many areas, as requirements become more complex and specialized. Therefore, solutions are needed that bundle knowledge and can be easily used by all responsible employees. Bosch Rexroth transforms its expertise into practical functions and thus significantly expands the scope of action in resistance spot welding.
Find out more about the next level resistance welding control system PRC7000!