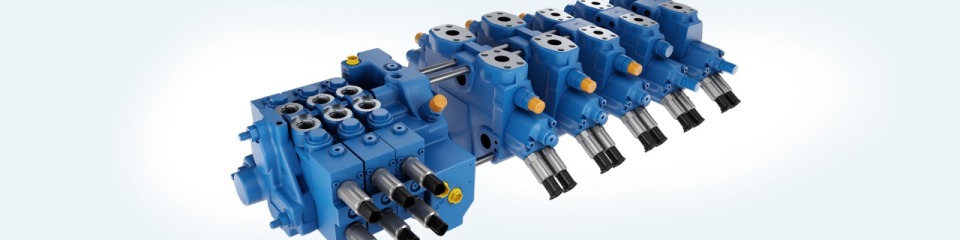
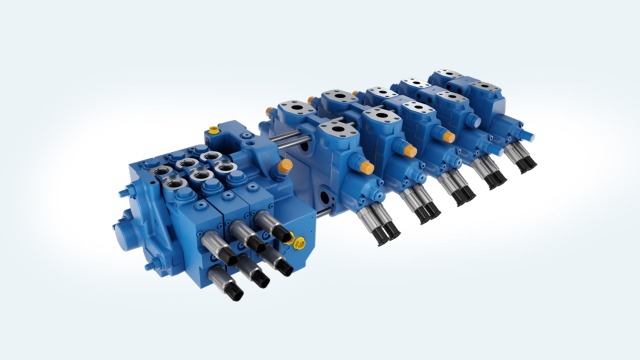
The Korean off-highway manufacturer Hyundai Construction Equipment is standardizing the working hydraulics of wheeled loaders, excavators, and forklifts with the help of Bosch Rexroth's flexible RS valve platform. The modularly assembled control blocks increase design freedom, functionality, and cost-effectiveness against the backdrop of advancing electronification.
How can the working hydraulics of excavators, wheeled loaders, and heavy forklifts be made more flexible, scalable, and efficient? Hyundai has found a sustainable answer with the flexible RS valve platform from Bosch Rexroth and established it in the Construction and Material Handling product segments. The modular system for combining slice modules and integrating functions as required plays a key role in the ongoing efforts to simplify processes, increase energy efficiency, and electronify working hydraulics in terms of intelligent functions.
The HL series wheeled loaders from Hyundai Construction Equipment are equipped throughout with the RS valves in sizes 15 and 20 (photo: Hyundai Construction Equipment).
Before the introduction of the modular valve platform, the working hydraulics of the mobile off-highway machines varied greatly by type and model. After all, excavators, wheeled loaders and forklifts require different and different numbers of functions. In addition, different performance classes require larger or smaller control blocks, whose control axes must in turn be adapted to the required functions.
Monolithic control blocks cannot map this cross-vehicle spectrum of requirements, as they realize the desired functions with a model-specific manufactured component. In contrast, the modular RS platform enables Hyundai Engineering to flexibly configure and standardize individual control blocks with flow-sharing (LUDV) to meet specific requirements.
„With the help of Bosch Rexroth's innovative solutions, we keep our fleet's working hydraulics at the cutting edge of technology and functionality," says Kangjun Sim, Team Manager Hydraulic Components at Hyundai Construction Equipment. „With the introduction of the RS platform, we are not only simplifying engineering and assembly, but also setting the course for the digital future at the same time.“
Hyundai laid the foundation for the switch to today's RS solution back in 2009. In just two years, the manufacturer equipped ten wheeled loader models with the Rexroth Monoblock M6 with flow-sharing technology (LUDV). At the same time, the Monoblock M7 LUDV went into series production in the forklift product range (larger than 18t). Both innovations represented an important step for Hyundai in the direction of energy efficiency and functionality. With this step, the previous fixed displacement pumps were replaced by variable displacement pumps and the hydraulic architecture was changed to closed center. The resulting reduction in pressure losses led to energy savings of ten percent and more, depending on the model. In functional terms, both vehicle types also benefited from the flow-sharing, as it distributes a brief undersupply evenly to all (non-safety-related) consumers and functions, thus avoiding the abrupt shutdown of just one function.
Example configuration for wheeled loaders: tailored functionality, optimum supply to different consumers, basis for progressive electronification and assist functions. (photo: Bosch Rexroth)
Hyundai took an even bigger evolutionary step from 2019 with the introduction of the RS valve platform as a flexible replacement for the two monoblocks M6 and M7. On the one hand, this allows individual control blocks to be assembled from standardized slice and function modules, and on the other hand, both worlds of flow-sharing (LUDV) and load-sensing (LS) can be combined. For example, prioritized functions such as steering can be implemented with the aid of the RBM priority module. With further integrated functions, Hyundai implements, for example, a vibration damping system (boom suspension) as well as anti-drift valves, variable or fixed tank preload valves and a control oil supply system.
The modular valve platform not only gives engineering a high degree of freedom in design, but at the same time lays the foundation for the gradual electronification of the working hydraulics. This is because in addition to hydraulic control, the internal channeling also enables electrohydraulic (EH) control, which Hyundai is successively expanding. The eOC software modules (electronic Open Circuit), for example, gives operators a feel for the payload even without load sensing by controlling the variables flow and pressure particularly finely at the start of the movement. In the course of increasing electronification, a number of new assistance and logic functions have already been implemented, such as a floating position for planning, anti-drift, or return-to-dig. More are to follow.
In the meantime, the RS platform with its characteristic slice modules has proven itself in four vehicle types at Hyundai. The first to go into series production with them were seven machine sizes in the HL wheeled loader series. While the smaller HL930 and HL940 models use size 15 modules, the larger machines from HL955 to HL970 are based on size 20. Thanks to the slice design modules of both sizes can also be combined to meet different volume flow requirements or to combine several functions that could not previously be integrated in just one block to save installation space, weight and expense. Following the successful series launch of the wheeled loaders, Hyundai also introduced the new platform in wheeled excavators and mini-excavators in the HW and HX model series.
In diesel-powered forklifts, the 18 to 25-ton weight class has been changed from M7 LUDV to RS since 2022. Bosch Rexroth was also awarded the contract to equip the 10 to 16 ton class. Hyundai is thus extending flow-sharing technology to smaller trucks and now benefits from a uniform platform for the complete model range from 110D to 250D. Here, too, different valve blocks are designed in line with flow rate requirements by combining modules of different nominal sizes. For example, the lift function can be represented by the RS20, the tilt function realized with the RS15 and the steering backed up by the RBM priority module.
Excavators and wheeled loaders have different functions, but with the RS modules from Bosch Rexroth they have a uniform valve platform for the working hydraulics - including the option of electronic control (photo: Hyundai Construction Equipment).
The decision to use the modular RS valve platform with similar equipment brings many advantages. The same modular technology for all machine types and performance classes not only simplifies engineering, but also documentation and service. At the same time, Hyundai benefits from even more precise design and design freedom in the course of standardization. For example, the electric pilot valves with their uniform characteristics simplify software creation. At the same time, the amount of piping required in production is reduced.
„Bosch Rexroth's modular solution approach enables us to combine the market requirements of flexibility and standardization in the interests of our customers," explains Kangjun Sim. "In doing so, we achieve noticeable time and cost savings over the entire life cycle, which strengthens our overall competitive position.“
In the operating phase, the RS platform reduces energy requirements and thus diesel consumption. For example, the load-sensing controlled priority valve realizes energy benefits compared with conventional priority valves, as only the oil volume dedicated for steering flows via the LS priority valve, thus avoiding previous pressure losses. A further customer benefit results from the electrohydraulic control, which makes operation significantly quieter and enables so-called "hydraulics-free cabs".
RS20 / RS15 valve platform: Economical combination of standardized slice modules to form energy-efficient and scalable control manifolds with integrated functions. (photo: Bosch Rexroth)
By switching to the RS modular valve platform from Bosch Rexroth, Hyundai has taken a further step toward future viability. „For us, the partnership with Bosch Rexroth is a competitive factor," sums up Kangjun Sim. "The quality of support and solutions is excellent, response times are short, and the innovative strength reinforces the future viability of our vehicles - in terms of design and cost efficiency as well as functionality and sustainability.“