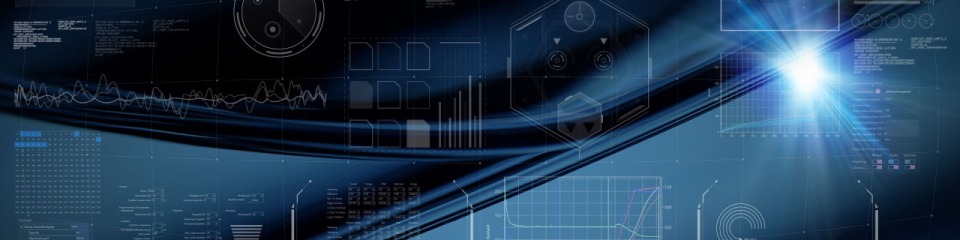
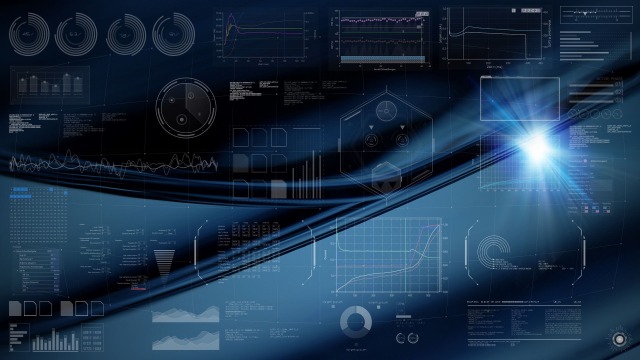
세계 곳곳의 6개 공장, 8개 생산 라인에서 자동차 한 대가 4종류로 생산됩니다. 12만 개가 넘는 용접 스폿에 제각각 매개변수를 결정하고 입력하며 최적화하고 검증해야 합니다. 이 예시는 저항 스폿 용접의 수요가 얼마나 높은지를 보여줍니다. 상황은 더욱 복잡해지고 있습니다. 경량 구조와 같은 트렌드가 지속되면서 공정 안정성과 생산성 면에서 새로운 과제가 계속 부각되기 때문입니다. 여기에는 이를테면 재료 조합에 따라 동적으로 빠르게 적응하는 용접 제어 시스템이 필요합니다.
320개 부품이 각기 다른 두께로 80가지 판금 작업과 코팅을 거칩니다. 이 과정에서 재료와 두께의 조합 500가지가 탄생하며 합쳐서 5,000여 개 스폿을 용접해야 합니다. 이것이 요즘 일반적인 자동차의 차체입니다. 수요는 계속 증가합니다. 자동차 구조의 트렌드를 요약하면 더 가볍고 더 안전한 차입니다. 무게가 가벼워야 연료 소비가 적고 CO2 배출이 감소하기 때문입니다. 재료를 적게 사용하므로 자동차 제조사의 생산비 감소로 연결됩니다. 동시에 디자인 형태는 갈수록 복잡해지고 있으며 충돌 안전성 조건도 반드시 맞춰야 합니다.
각기 다른 재료를 조합하기 때문에 여기에 필요한 용접 작업의 수도 계속 증가하는 추세입니다. 자동차 산업의 경우 동일한 생산 라인에서 여러 자동차 유형과 모델을 생산하는 경우가 늘어나고 있습니다. 이러한 현상은 용접 제어와 모니터링은 물론 시운전 요건에 모두 직접적인 영향을 줍니다.
가벼운 디자인을 만들기 위해 최근 자동차에는 부식 방지 코팅을 입힌 고강도 스틸 재료를 사용하는 일이 잦아지고 있습니다. 고강도 스틸을 사용하여 부품을 더 얇은 벽으로 설계하면서도 동일한 기계 속성을 가질 수 있습니다. 그러나 이런 재료는 저항 스폿 용접 도중에 갈라지기 쉽습니다.
알루미늄과 스틸을 저항 스폿 용접으로 접합하는 경우에도 양극단의 물리적 속성 때문에 난관에 부딪칩니다. 스틸은 전기 저항이 높지만 알루미늄은 낮기 때문입니다. Bosch Rexroth의 새로운 고성능 PRC7000 용접 제어 시스템은 두 가지 문제를 모두 해결합니다. 변압기가 용접 제어 시스템의 출력을 현재 용접 작업에 맞도록 정확하게 변환합니다.
PRC7000을 사용하면 스틸부터 알루미늄까지 재료와 두께 조합이 각기 달라도 간단하게 용접할 수 있습니다. 이를 위해 새로운 용접 제어 시스템은 적응형 컨트롤러와 유연한 프로그래밍 기능을 이용합니다. 용접 스폿의 완벽한 재현도 가능합니다.
한 유명 자동차 제조사가 최초로 저항 스폿 용접으로 신차 섀시에 다량의 알루미늄 부품을 접합했습니다. 이때 메인 바디는 알루미늄이었고 각기 다른 알루미늄 판 조합과 약 2,000개 스폿을 용접했습니다.
새로운 버전의 PRC7000에서는 건 데이터 모듈이 공정 신호를 건 자체에 디지털화합니다. 제어 시스템에 변수를 입력할 필요 없이 가용한 모든 제어 시스템에서 수동 건이 작동합니다. 데이터는 완전한 용접 작업으로 건 데이터 모듈에 저장되며 이후 제어 시스템으로 전송할 수 있으므로 작업을 중단할 필요가 없습니다. 이를 통해 사용자는 더 많은 자유를 누릴 수 있을 뿐만 아니라 새로운 용도에 활용할 수 있으며 비용을 절감할 수 있습니다.
자동차 제조사는 PRC7000 용접 제어 시스템을 이용해 매우 높은 품질기준을 준수하면서 다양한 저항 스폿 용접의 요구조건을 효율적이고 유연하게 충족할 수 있습니다. 이로써 경제성과 공정 안정성, 생산성이 보장됨은 물론 경쟁력도 높일 수 있습니다.