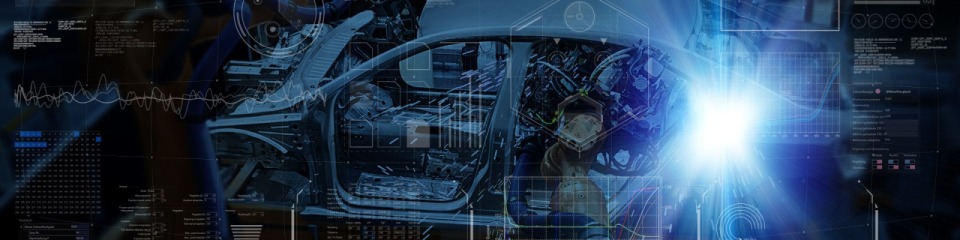
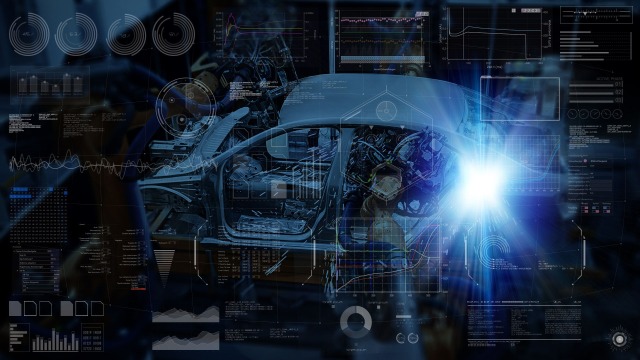
미래의 용접 공정에서는 모든 것이 연결될 것입니다. 이때 핵심 요소는 용접 제어 시스템입니다. 다른 장치와 시스템에 잘 연결되어 통신하기 위해 과거에는 하드웨어 게이트웨이 형태의 미들웨어를 사용하는 경우가 많았습니다. 그러나 더 이상 중간 장치는 필요하지 않습니다. Bosch Rexroth PRC7000 용접 제어 시스템에 직접적으로 지능이 통합되기 때문입니다. 그 결과 4차 산업을 지원하며 MQTT 및 OPC UA 프로토콜이 완전히 통합된 최초의 '올인원' 솔루션을 저항 스폿 용접에 사용할 수 있습니다. 이로써 비용이 절감되고 연결 요구조건을 쉽사리 충족할 수 있습니다. 이 기반에서는 AI 응용 또한 가능합니다.
용접 공정 중에는 다량의 데이터가 생산됩니다. 이 데이터는 4차 산업의 공정 최적화와 머신러닝, 가치 창출의 근간을 이룹니다. 그러나 그에 앞서 그 데이터를 수집하고 분석하여 추가로 처리해야만 합니다. 그래야만 의사결정 목적으로 활용할 세부 정보가 생성되고 이후 자동으로 정의된 조치를 시작할 수 있습니다.
이후 OPC UA 프로토콜을 통해 클라우드로 데이터를 보내 분석하고 피드백은 산출물이 되어 제어 시스템으로 향합니다. 이 기반에서는 머신러닝이나 인공지능(AI) 등 응용 또한 가능합니다. 데이터 수집과 분석을 통해 머신러닝 용도의 올바른 결정을 도출할 수 있습니다. 개선도 가능하며 품질관리 비용을 크게 절감할 수 있습니다.
OPC UA 개방형 통신 표준은 디지털 공장에 더욱 중요해지고 있습니다. IoT에서 가장 중요한 통신 프로토콜 중 하나이며 현재 산업 표준이 되고 있기 때문입니다. OPC UA는 기계에 데이터를 전송할 뿐만 아니라 기계가 읽을 수 있는 방식으로 의미 서술이 가능하므로 AI와 머신러닝 응용을 지원합니다.
Bosch Rexroth PRC7000 용접 제어 시스템은 OPC UA를 완전히 통합한 최초의 솔루션입니다. 갈수록 많은 자동차 제조사가 MQTT 개방형 네트워크 프로토콜의 사용과 함께 이를 요구하고 있습니다.
PRC7000에는 OPC UA 서버 외에도 MQTT 퍼블리셔가 완전히 통합되어 있습니다. 둘 다 라이선스를 받은 소프트웨어로 사용할 수 있습니다. MQTT는 저대역 고지연 환경에서 사용하도록 설계되었습니다. 그래서 다량의 데이터를 패키지로 보내야 하는 경우에 적합합니다. 예를 들어 제어 시스템은 하루 최대 3만 개의 용접 스폿을 기록하고 데이터를 전송할 수 있습니다. 이때 전송되는 데이터는 인간이 해석할 수 있는 텍스트 기반의 자기 서술 형식인 JSON 포맷입니다.
또 다른 JSON 기반 프로토콜인 PPMP는 연결된 산업에서 데이터를 전송하기 위해 Bosch가 새로 개발한 개방형 산업 표준입니다. PPMP를 이용해 Bosch의 Nexeed PPM(Production Performance Manager)과 같은 제조 실행 시스템(MES)을 연결할 수 있습니다. 이전의 용접 제어 시스템은 충분히 강력하지 않았기 때문에 OPC UA와 MQTT와 같은 프로토콜을 실행하기 위한 설계가 아니었습니다. 장치와 에지 또는 클라우드 레이어 사이에는 자체 하드웨어가 필요할 수도 있는 미들웨어 또는 게이트웨이 소프트웨어를 제공해야 했습니다. 데이터를 수집하고 취합하여 전송하는 것은 미들웨어의 역할이었습니다.
PRC7000의 경우 OPC UA와 MQTT가 제어 시스템에 직접 통합되므로 중간 하드웨어가 필요하지 않습니다. 미래 자동차 공장에서는 데이터 무결성이 대단히 중요한 만큼 인증 기반의 데이터 암호화가 가능해야 합니다.
PRC7000 용접 제어 시스템은 MQTT와 OPC UA 인터페이스를 이용해 4차 산업에 필요한 IoT 연결을 제공합니다. 그러나 연결과 지능형 응용에 관한 또 다른 기능도 있습니다. 고성능 하드웨어의 일부로서 IA 사용 사례의 복제에 필요한 성능을 제공한다는 것입니다.
PRC7000의 4차 산업 기능은 수없이 많은 사용 사례와 새로운 비즈니스 모델을 지원합니다. OPC UA 액세스를 통해 소규모 기계 제조사는 자체 사용자 인터페이스를 손쉽게 개발하고 제공할 수 있습니다. 혹은 시스템 중단 추세라든가 결함 원인과 같은 것을 식별하고 예방 조치를 실행하여 공정 최적화 및 비용 절감의 근간으로 활용할 수도 있습니다.