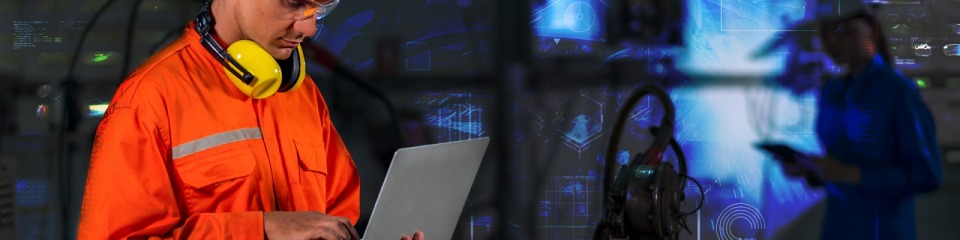
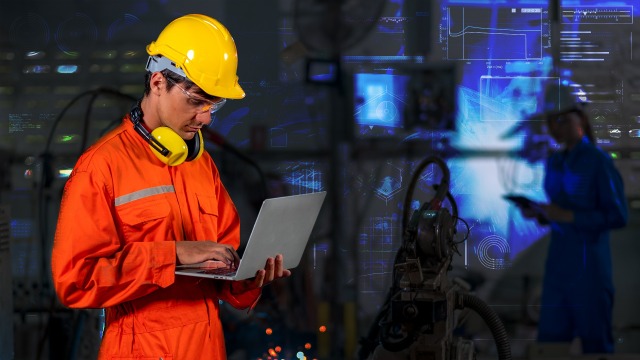
The modern welding control system is designed to be sustainable, highly efficient, and Industry 4.0-capable. Ideally, it will have a long life as well. Bosch Rexroth resistance spot welding controls have long been much more than just a piece of hardware; they are being guided into the future with software solutions that can be configured as needed. At the same time, services support the entire product life cycle. This results in welding process optimizations that lead to quality improvements, shorter cycle times, and economic advantages.
In industries like the automotive sector, the pace of change is rapid. Higher, faster, lighter. Developments such as lightweight construction are also increasing the complexity of resistance spot welding. This means that the process is constantly facing new challenges in terms of process stability and productivity.
A modern control system for resistance spot welding must therefore be flexible, adaptable, highly powerful, and future-proof. To make this possible, Bosch Rexroth relies on services for an entire product life and beyond – from commissioning to second life – whereby used control devices are given a new lease of life, for example.
With its welding services, designed for the PSI6000 and PRC7000 welding controls, Bosch Rexroth is breaking new ground in the industry. Until now, few, if any, services have generally been marketed in welding technology. However, they are the only way to make welding controls fit for the challenges of today and tomorrow.
Resistance spot welding technology can be used to join materials with a wide variety of physical or chemical properties, as well as different surfaces, shapes, and thicknesses. The weldability check enables users to determine the optimum parameterization for the process. This service package includes, among other things, material testing in the laboratory, welding quality assurance by means of welding tests and parameter determination in accordance with VDA (German Association of the Automotive Industry), metallography, and destructive testing.
Bosch Rexroth also supports commissioning in the field of resistance welding technology with services for greater safety and efficiency. This is because increasingly demanding welding tasks due to mixed combinations and different variants require experience and expertise. However, these skills do not develop analogously in the control and welding process on the part of the users. These and other factors have a direct influence on commissioning. Thanks to the wealth of experience of Bosch Rexroth associates in a wide range of welding tasks and the services based on them, control systems, control cabinets, or complete production plants can be commissioned quickly and effectively.
Constant process changes in welding, wear, optimization of components and materials, and the modernization of plant components permanently alter the welding parameters. Welding parameters that are appropriate for the material form the basis for productivity and quality – especially when starting up a new production line. Bosch Rexroth offers a service package for this purpose, which includes the analysis of parameters for welding in constant current control.
Services can also be used to optimize the welding parameters in terms of quality, spatter-free welding, energy efficiency, and limit values. Analysis software is also available. Targeted evaluations can be used, for example, to reduce cycle times.
In addition to optimizing the welding process, services for the entire life cycle also aim to extend the product life of the welding control system and save resources. One key to this is repair, including, for example, cleaning, modification to the current hardware status, readjustment to original data and parameters, as well as functional tests and endurance tests in accordance with specifications. Defective parts are replaced with a warranty period of twelve months from delivery.
In addition to repair, product remanufacturing is recommended in the interests of sustainability and longevity. This involves the preventive replacement of all electrical and electromechanical wear parts such as power semiconductors, fans, and electrolytic capacitors. After delivery, the remanufactured product has a warranty period of 24 months.
The serviceability of installed products and solutions beyond the usual service period is ensured by the Long Life Service (LLS). This provides spare parts as well as remanufacturing and repairs depending on material availability. And with the extended warranty, which can be increased from 24 months to up to 60 months, users can rest easy.
When it comes to any kind of service, nothing beats the original. Bosch Rexroth offers service from the manufacturer and provides only original spare parts. Support and services are available 24/7 throughout the year in over 80 service centers worldwide.
The services ensure long runtimes and stable processes for the welding controls, and thereby minimize downtimes. They also contribute to sustainability, which is so important for the future, saving both money and resources.
Find out more about the next level resistance welding control system PRC7000!