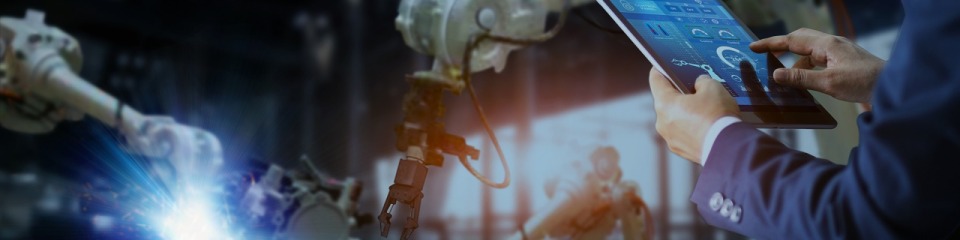
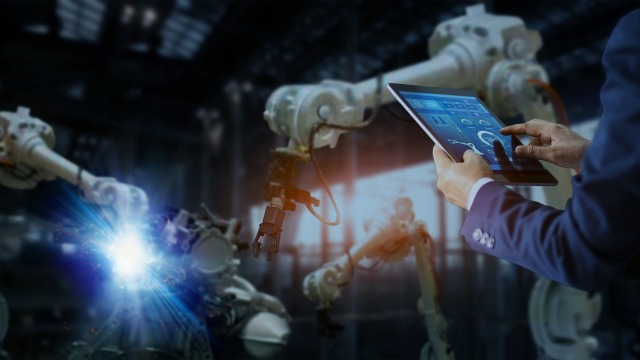
Why does a welding control system need Industry 4.0 capability? Welding yields true treasures in the form of immense amounts of data, which can serve as the basis for process optimization, machine learning, and value creation. To this end, however, the data must first be collected, analyzed, and processed. Common standards for accessing this data are MQTT and OPC UA. Bosch Rexroth bundles these two types of communication in the “IoT Connector” package. This allows users to process the collected data according to their needs and, for example, implement automatic logging for quality assurance.
The PRC7000 welding control can be easily prepared for Industry 4.0 with the "IoT Connector" package, which combines the two communication types MQTT and OPC UA.
The control system functions as a process device and communication gateway in one. The IoT Connector makes data available for further processing, for example, for statistical evaluations or permanent logging. The goals include cost savings in quality management and preventive maintenance. These are increasingly important priorities in resistance welding, for example, in the automotive industry for body-in-white construction, in the area of TIER1 suppliers, and also in mechanical engineering.
Both types of communication are leaders in their field: MQTT as an open network protocol and OPC UA as a communication standard in automation.
MQTT is designed for low-bandwidth, high-latency environments. It is ideally suited for sending vast amounts of data in packets. For example, a control system stores and sends up to 30,000 weld spots per day. The PRC7000 control sends the data in JSON format – a text-based, self-describing format that can be interpreted by humans.
OPC UA has the ability not only to transport machine data, but also to semantically describe it in machine-readable form. In this way, data can be sent to the cloud, analyzed, and the results written back to the control system. This forms the basis for applications approaching machine learning and artificial intelligence (AI).
Both standards are available in the IoT Connector. The basic functionality of the PRC7000 welding control system includes not only an MQTT publisher, but also an OPC UA server as standard. The data scope can be extended with a license, which opens up even more potential applications.
Previous welding control systems were not designed for the implementation of protocols such as MQTT and OPC UA due to insufficient performance. Instead, middleware or gateway software, which may require its own hardware, had to be connected between the device and the edge or cloud layer. The data was fetched, aggregated, and sent by the middleware.
The IoT Connector supports vertical integration from within the process device, for example, to the cloud or edge. As an open system, it is not subject to any proprietary structures and offers state-of-the-art communication. Users can process the data according to their needs. With the PRC7000 control, a defined data scope – for example, for iO/niO evaluation – is included as standard.
The expanding package enables an even more extensive data flow and thus further use cases. For example, the IoT Connector can be used to determine more than 200 actual values per weld spot. These include quality values, raw data from welding curves, various parameters such as setpoints, settings and reference curves, as well as data changes. When combined with the evaluation of other data sources, preventive maintenance concepts can be implemented. Further benefits help to ensure transparency by allowing users to identify and exploit optimization potential: Automatic logging can be implemented for quality assurance purposes, logged parameter changes enable analyses of the spot weld quality, and the status in the body shop can be visualized via parameter information.
Today's industry requires flexible and versatile production that can respond to dynamically changing requirements. This demands adaptable solutions that support networking and ensure consistency. Bosch Rexroth is responding to the needs of the modern factory with the IoT Connector. It enables the PRC7000 and PSI6000 welding controls from Bosch Rexroth to be expanded to meet Industry 4.0 requirements and to mine data treasures.
Find out more about the next level resistance welding control system PRC7000!