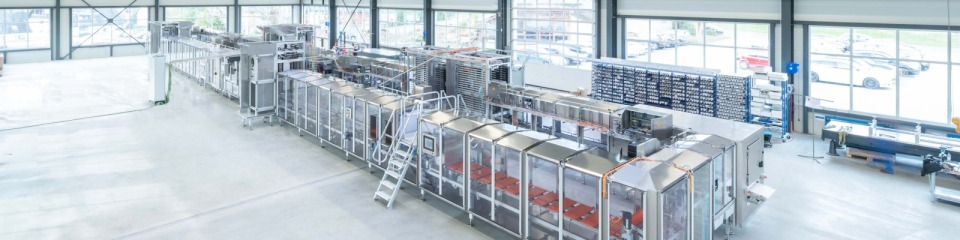
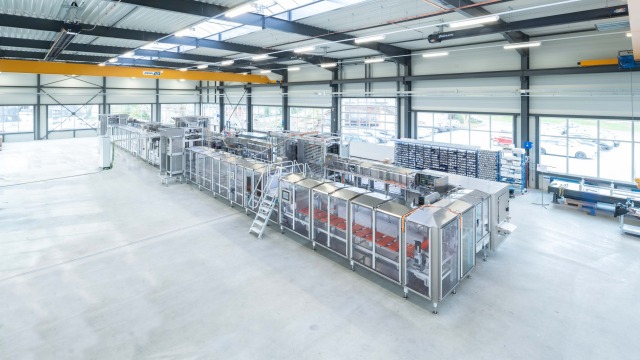
WDS modularises its confectionery machines with the help of control cabinet-less drive technology from Bosch Rexroth. Users benefit from faster commissioning, space-saving production and optional M2M communication right through to packaging.
A modular machine design has several advantages for confectionery machine manufacturers: The pre-installed and tested equipment saves time and costs during on-site assembly. At the same time, modules that can be quickly combined into customised solutions achieve valuable standardisation effects. Decentralised drive technology from Bosch Rexroth plays a key role here, as it does not require a control cabinet and can be wired quickly and easily.
At interpack 2023, Winkler und Dünnebier Süßwarenmaschinen GmbH (WDS) will be demonstrating just how powerful the new modular concept is, among other things, on a pouring station of the ConfecPRO modular confectionery production system. Depending on the product and equipment, it fills up to 25 moulds of chocolate, jelly or over-the-counter products per minute. This corresponds to an hourly output of up to three tonnes, with a dosing accuracy of only 0.5 per cent of the average product weight.
The high demands in terms of quality and productivity require not only accurate mechanics, but also a powerful control system. "In larger plants, we implement up to 120 axes and 100 drives in synchronous mould transport," says Bernd Plies, head of digitalisation at WDS. "Each drive can run its own optimised motion profile in the process." For the technical implementation of decentralisation, WDS chose a combination of the control cabinet-free drive solution IndraDrive Mi and the motion control IndraDrive MLC.
We have been working with Bosch Rexroth for around 30 years and know of no other supplier with a comparably sophisticated solution that can be integrated into our overall system so flexibly and without additional effort - including supply units in protection class IP65
Bernd Plies, Head of Digitalisation at WDS
In the modular production plant of this type, the IndraMotion MLC coordinates around 40 electronically synchronised transports with their own decentralised drive. In this way, the ConfecPRO seamlessly conveys the moulds made of polycarbonate through the system using the loose mould principle with a chain drive. After heating, the first pouring process with liquid chocolate follows. Then the patented cold stamp technology (flash-shell cooling) forms a shell which is filled, cooled and sealed again. The dosing unit and other individual axes are switched on by the control system depending on the situation.
The modular design reduces the effort for electrical installation on site by up to 70 percent. All previous power and feedback cables to the central control cabinet are eliminated. Instead, the individual drive modules are connected via hybrid cables using the daisy-chain method. In this way, WDS saves more than 50 percent of supply and feedback cables compared to the previous machine generation. In the first ConfecPRO, the control cabinet was only 1.8 m long instead of 12 m previously. With the latest generation, the rest of the control cabinet has now also been eliminated. The power consumption is also reduced: since the former central cooling units could be replaced by decentralised enclosures with filter fans, a total of 7.5 kW less air-conditioning power is required. The use of regenerated energy through the DC link coupling of the servo system further improves the energy balance.
Control cabinet-free: The decentralised drive solution IndraDrive Mi enables a modular design and reduces the cabling effort through serially laid hybrid cables (image source: WDS).
Decentralised servo drives ensure precise feed of the chocolate moulds. The individual transports are synchronised by the IndraDrive MLC motion control (image source: WDS).
The many networking options of the Rexroth ctrlX CORE control system as an edge device are also decisive for WDS. They range from vertical interfaces according to the Weihenstephan Standard (WS) or PackML (Packaging Machine Language) to direct data tapping by ERP and MES systems to horizontal communication based on OPC UA, the new language sub-area WS Sweets, in the Weihenstephan Standard. Tobias Gerhard, Business Development Fast Moving Consumer Goods, at Bosch Rexroth, illustrates the potential inherent in this. "M2M communication enables the current status to be passed on to the respective upstream and downstream machine. Due to the consistently transparent value stream, the entire line can thus flexibly adapt to new products and situations - from preparation to the moulding line to primary and secondary packaging. Bernd Plies sees a further added value of the ctrlX Core Edge solution in the simple connection to the SweetConnect industry platform - an open platform ecosystem developed for the confectionery industry, which will be presented by various machine manufacturers at Interpack.
Author: Tobias Gerhard
Position: Senior Business Development Manager Consumer Goods in Central Europe Sales, Bosch Rexroth AG