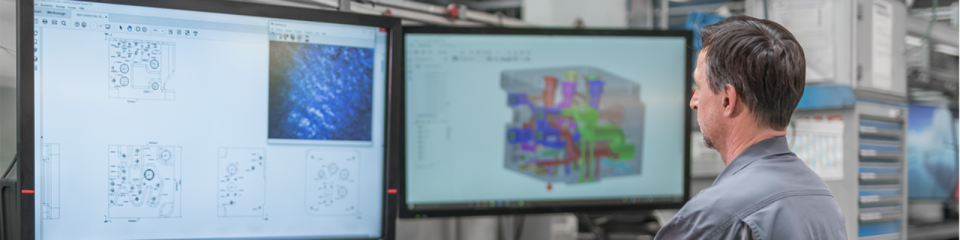
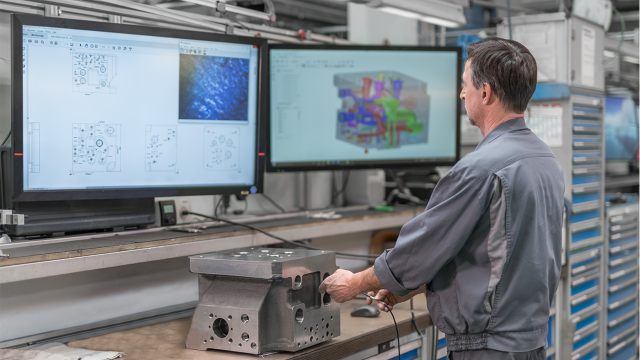
Manifolds produced using additive manufacturing with optional condition monitoring get recycling systems ready for the future
Flow-optimized manifolds save materials, increase energy efficiency and avoid CO2 emissions. Bosch Rexroth designs manifolds for recycling systems as part of efficient hydraulics according to individual requirements and produces them using 3D sand core printing as part of an additive manufacturing process. This new design freedom and integrated functions reduce the weight by about a third and make it easier to install the manifolds in machines. An optional condition monitoring concept further increases the availability of hydraulic systems.
Next-generation hydraulics offers three key levers for greater sustainability: Less energy, less fluid and less material. When it comes to manifolds, the key to this lies in additive manufacturing.
With the help of CFD simulation (Computational Fluid Dynamics), Bosch Rexroth designs the internal and external geometries so optimally that the need for materials, fluid and energy is reduced over the entire life cycle. The fact that a manifold produced using 3D sand core printing requires around 50 kg less material than manifold produced in the conventional manner shows what savings are possible.
Because fewer resources are required, the CO2 emissions during production are reduced by 130 kg, i.e. a third. The difference equates to the emissions from a car powered by fossil fuel traveling 1,000 km.
In the operating phase, the manifold requires much less energy thanks to its flow-optimized internal geometry with minimal Delta p and low noise emissions. After 3,000 operating hours per year, 740 kWh of electricity is saved. This means that the CO2 footprint is reduced by around 450 kg a year, which equates to driving a car for 3,000 km. Thanks to the electricity saved during the operating phase, the investment usually pays for itself after around 3.5 years. After that, costs are reduced on an ongoing basis.
The optimization also allows a more compact machine design in which the manifold fits optimally. Formerly external components can be integrated into the machine even in situations where space is limited. The hydraulics are combined in a single module. Users thus reduce their costs and cut the effort required for assembly, piping and service.
The individual manifolds complement Bosch Rexroth’s conventional range of products for baling presses, scrap shears and scrap presses. In order to maximize energy and CO2 savings, Bosch Rexroth recommends viewing all hydraulic components on a system level.
Condition monitoring for manifolds
In order to increase the availability of hydraulic recycling systems, Bosch Rexroth has developed a complementary condition monitoring concept for manifolds. This software module for extra productivity works with control systems from various manufacturers and visualizes not only the circuit diagram but also the status of valves. Operators of channel balers and other hydraulic applications are therefore able to monitor the relevant machine function, analyze errors immediately and restore availability more quickly.
Media Assets
Basic Information Bosch Rexroth
As one of the world’s leading suppliers of drive and control technologies, Bosch Rexroth ensures efficient, powerful and safe movement in machines and systems of any size. The company bundles global application experience in the market segments of Mobile Applications, Machinery Applications and Engineering, and Factory Automation. With its intelligent components, customized system solutions and services, Bosch Rexroth is creating the necessary environment for fully connected applications. Bosch Rexroth offers its customers hydraulics, electric drive and control technology, gear technology and linear motion and assembly technology, including software and interfaces to the Internet of Things. With locations in over 80 countries, more than 31,000 associates generated sales revenue of around 6.2 billion euros in 2021.
Basic Information Bosch
The Bosch Group is a leading global supplier of technology and services. It employs roughly 402,600 associates worldwide (as of December 31, 2021). The company generated sales of 78.7 billion euros in 2021. Its operations are divided into four business sectors: Mobility Solutions, Industrial Technology, Consumer Goods, and Energy and Building Technology. As a leading IoT provider, Bosch offers innovative solutions for smart homes, Industry 4.0, and connected mobility. Bosch is pursuing a vision of mobility that is sustainable, safe, and exciting. It uses its expertise in sensor technology, software, and services, as well as its own IoT cloud, to offer its customers connected, cross-domain solutions from a single source. The Bosch Group’s strategic objective is to facilitate connected living with products and solutions that either contain artificial intelligence (AI) or have been developed or manufactured with its help. Bosch improves quality of life worldwide with products and services that are innovative and spark enthusiasm. In short, Bosch creates technology that is “Invented for life.” The Bosch Group comprises Robert Bosch GmbH and its roughly 440 subsidiary and regional companies in some 60 countries. Including sales and service partners, Bosch’s global manufacturing, engineering, and sales network covers nearly every country in the world. With its more than 400 locations worldwide, the Bosch Group has been carbon neutral since the first quarter of 2020. The basis for the company’s future growth is its innovative strength. At 128 locations across the globe, Bosch employs some 76,100 associates in research and development, of which more than 38,000 are software engineers.
Press Contact
Spokesperson technology topics
Manuela Kessler
+49 9352 18-4145
Manuela.Kessler@boschrexroth.de