ENERGIZE YOUR INTRALOGISTICS
with the autonomous Mobile Robot (AMR) ACTIVE Shuttle
The AMR ACTIVE Shuttle makes it possible to enter the factory of the future today. Without adapting your existing factory infrastructure, the ACTIVE Shuttle is quickly implemented, intuitive to operate, fully networked and safe to use! ACTIVE Shuttle automates and standardizes your internal material and goods flow. In the future, transport your floor rollers loaded with small load carriers (KLT) in a highly flexible and safe manner. The ACTIVE Fleet Manager (AFM) enables highly flexible order management, in which orders can be entered manually or fed in automatically via third-party systems. The ACTIVE Shuttle communicates via the VDA 5050 interface with third-party systems for controlling the fleet.
AMR ACTIVE Shuttle
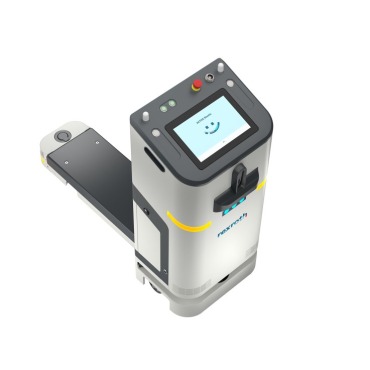