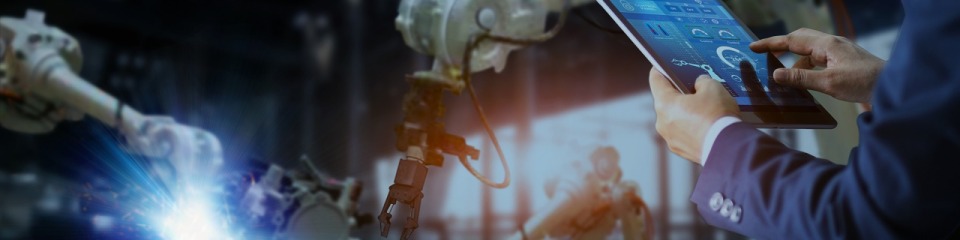
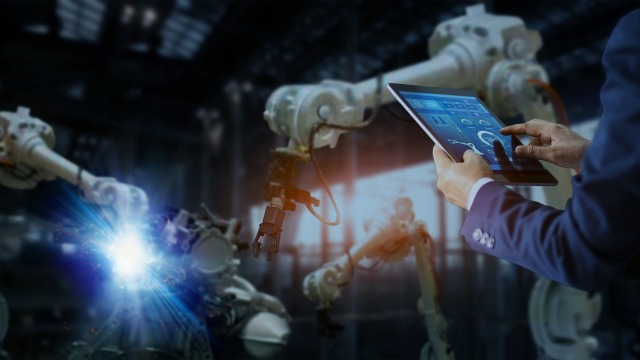
¿Por qué un sistema de control de soldadura necesita poder adaptarse a la industria 4.0? Las soldaduras crean verdaderos tesoros en forma de enormes cantidades de datos que pueden servir como base para la optimización de procesos, el aprendizaje automático y la creación de valor. Sin embargo, para alcanzar este objetivo primero tenemos que recopilar, analizar y procesar datos. Los estándares comunes para acceder a estos datos son MQTT y OPC UA. Bosch Rexroth agrupa estos dos tipos de comunicación en el paquete "conector IoT". Así, los usuarios pueden procesar los datos recopilados según sus necesidades y, por ejemplo, implementar registros automáticos para los controles de calidad.
El control de soldadura PRC7000 puede prepararse fácilmente para la industria 4.0 con el paquete "conector IoT", que combina los tipos de comunicación MQTT y OPC UA.
El sistema de control funciona a la vez como dispositivo de procesos y pasarela de comunicación en uno. El conector IoT hace que los datos estén disponibles para su posterior procesamiento, por ejemplo, para evaluaciones estadísticas o registros permanentes. Sus objetivos incluyen el ahorro de gastos en gestión de la calidad y el mantenimiento preventivo. Estas son prioridades cada vez más importantes para la soldadura por resistencia, por ejemplo, en la industria del automóvil para la construcción de carrocerías en bruto, en el sector de los proveedores de TIER1 y para la ingeniería mecánica.
Ambos tipos de comunicación son líderes en su sector: MQTT como protocolo de red abierto y OPC UA como estándar de comunicación en automatización.
MQTT se diseñó para entornos con poco ancho de banda y alta latencia. Es perfecto para enviar cantidades enormes de datos en paquetes. Por ejemplo, un sistema de control almacena y envía hasta 30.000 puntos de soldadura cada día. El PRC7000 envía los datos en formato JSON, un formato basado en texto y autodescriptivo que los humanos pueden interpretar.
OPC UA no solo tiene la capacidad de transportar datos de la máquina, sino también de describirlos semánticamente de forma que sea legible para la máquina. Así, los datos pueden enviarse a la nube y analizarse, y los resultados escribirse de nuevo en el sistema de control. Esto constituye la base de las aplicaciones que abordan el aprendizaje automático y la inteligencia artificial (IA).
Ambos estándares están disponibles en el conector IoT. Las funciones básicas del sistema de control de soldadura PRC7000 no solo incluyen un editor de MQTT, sino también un servidor OPC UA de serie. El ámbito de los datos se puede ampliar con una licencia, abriendo paso así a aún más posibles aplicaciones.
Los sistemas de control de soldadura anteriores no estaban diseñados para la implementación de protocolos como el MQTT y el OPC UA, ya que no tenían el rendimiento necesario. En lugar de esto, entre el dispositivo y la capa de borde o la nube había que conectar un software de intermediación o pasarela, que podía requerir hardware propio. El software intermedio recogía, agregaba y enviaba los datos.
El conector IoT es compatible con la integración vertical desde el interior del dispositivo de procesos, por ejemplo, a la nube o el borde. Como sistema abierto, no está sujeto a ninguna estructura privada y ofrece lo último en comunicaciones. Los usuarios pueden procesar datos según sus necesidades. El control PRC7000 incluye de serie un ámbito de datos definido (por ejemplo, para evaluación de iO/niO).
El paquete en crecimiento permite un flujo de datos aún más amplia y, por lo tanto, más casos de uso. Por ejemplo, el conector IoT puede utilizarse para determinar más de 200 valores reales por punto de soldadura. Estos incluyen valores de calidad, datos sin procesar de curvas de soldadura, varios parámetros como puntos de ajuste, configuración y curvas de referencia, así como cambios en los datos. Al combinarlo con la evaluación de otras fuentes de datos, se pueden implementar conceptos de mantenimiento preventivo. Otros beneficios ayudan a garantizar la transparencia permitiendo a los usuarios identificar y explotar su potencial de optimización. Se puede implementar el registro automático para el control de calidad, los cambios en los parámetros registrados hacen posible el análisis de la calidad de la soldadura por puntos y es posible visualizar el estado en el taller mediante la información del parámetro.
La industria actual requiere una producción flexible y versátil que pueda responder a los cambios dinámicos de los requisitos. Esto hace necesario tener soluciones adaptables que soporten las conexiones de red y garanticen la consistencia. Bosch Rexroth responde a las necesidades de las fábricas modernas con el conector IoT. Este hace posible ampliar los controles de soldadura PRC7000 y PSI6000 de Bosch Rexroth para cumplir los requisitos de la industria 4.0 y extraer tesoros en forma de datos.
Obtenga más información sobre el siguiente nivel del sistema de control de soldadura por resistencia PRC7000.