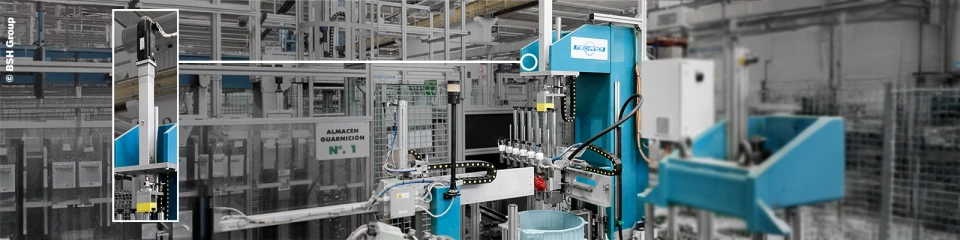
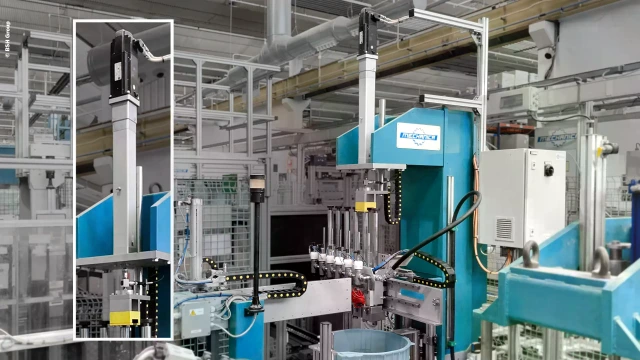
Le groupe BSH standardise les processus de pressage et d’assemblage importants pour la qualité de la production de machines à laver. Comment ? Avec le sous-système mécatronique Smart Function Kit Pressing. Le résultat : davantage de flexibilité, de stabilité et de transparence, avec une durée minimale requise pour l’ingénierie, l’intégration et le contrôle de la qualité.
Selon Maximilian Aßmuth de l’équipe d’ingénierie industrielle de blanchisserie chez BSH, les servopresses électromécaniques récemment lancées et basées sur le Smart Function Kit Pressing présentent un avantage de taille par rapport aux solutions pneumatiques utilisées jusqu’à présent. Elles permettent des processus de haute précision, économisent de l’énergie et fournissent une base fiable pour l’assurance qualité et davantage d’optimisations de processus. Pourquoi ? Car les servopresses électromécaniques convertissent le couple généré électriquement directement en mouvement par le biais d’un entraînement à vis dans le vérin électromécanique EMC, le contrôlent minutieusement et saisissent avec précision les données du processus au moyen de capteurs et de logiciels. Tels sont les avantages que le groupe BSH met à profit pour rendre les processus du réseau de production mondial plus économiques.
Maximilian Aßmuth
Équipe d’ingénierie industrielle de blanchisserie chez BSH
Le projet de standardisation international a été lancé avec le premier Smart Function Kit Pressing dans l’usine de La Cartuja près de Saragosse, en Espagne. La solution mécatronique est composée d’un vérin électromécanique avec un capteur de force, d’un servomoteur équipé d’une servocommande et d’un PC industriel avec logiciel d’exploitation préinstallé. Dans la production de machines à laver, la servopresse intelligente est utilisée afin de fixer de manière fiable un joint important entre l’arbre du tambour et le réservoir d’eau, lequel contient l’eau dans la machine. Grâce au pack complet préassemblé et à une bonne préparation, le projet a rapidement connu le succès. Après trois jours seulement, ainsi qu’un essai, la combinaison puissante de la technologie de pressage, du logiciel et du service a été mise en service de manière fiable.
Le premier Smart Function Kit Pressing de BSH a été mis en service à l’usine de La Cartuja, près de Saragosse, en 2021. Plus de 20 servopresses sont maintenant exploitées dans le monde entier. (Source de l’image : BSH Group)
Aujourd’hui, l’usine de La Cartuja produit principalement des appareils électroménagers pour des marques bien connues comme Bosch, Siemens, Gaggenau et Neff. Ce site espagnol, avec environ 400 employé(e)s, fait partie du réseau de production mondial composé de 37 usines qui emploient environ 60 000 personnes. Le Smart Function Kit Pressing joue un rôle important dans la standardisation de processus, tout comme la présence mondiale de Bosch Rexroth.« Après la phase d’évaluation, le Smart Function Kit s’est avéré être la solution la plus adaptée et la plus rentable. La simplicité d’utilisation est particulièrement pratique durant les services de nuit, lorsque les opérateurs n’ont pas accès à l’assistance technique », explique David Ochoa, ingénieur en processus chez BSH.
Smart Function Kit Pressing permet de gagner un temps précieux en ingénierie avant même la mise en service sur site. À l’aide des outils électroniques intelligents de Bosch Rexroth, le sous-système mécatronique peut être conçu, configuré et commandé de manière numérique dans la boutique Rexroth en quelques minutes. Après la livraison de la servopresse prémontée en un seul colis, l’assistant du logiciel d’exploitation basé sur un navigateur Web vous guide pas à pas dans le processus de mise en service. La définition du processus a lieu visuellement à l’aide de modules disposés graphiquement et l’intégration paramétrée de la ligne est également réalisée rapidement grâce à des blocs fonctionnels préparés. Le résultat et les données de processus peuvent être visualisés directement sur le tableau de bord et transférés vers différents systèmes par le biais d’interfaces variées.
Le Smart Function Kit Pressing permet de gagner du temps entre la phase d’ingénierie et la phase opérationnelle. La conception, la configuration et la commande sont exclusivement numériques, tandis que le logiciel d’exploitation préinstallé réduit la charge de travail occasionnée par la mise en service, la définition du processus et l’intégration de la ligne. (Source de l’image : Bosch Rexroth)
Smart Function Kit Pressing est disponible dans la gamme de force de 2 à 70 kN et couvre trois applications typiques : joindre à la position, joindre à la force ou joindre à la force avec maintien ultérieur. Le joint est mis en place dans l’usine BSH de La Cartuja. Dans ce but, il est tout d’abord pressé dans le boîtier du roulement. Une fois que le joint racleur a été introduit dans l’axe, la presse se déplace vers la position prédéterminée spécifique au produit dans un temps de cycle court.
Si une nouvelle variante est détectée via RFID, la commande de ligne transfère automatiquement les paramètres pertinents tels que les trajectoires, les forces et les tolérances à la servopresse.« Grâce au contrôle numérique du processus, nous pouvons réagir très rapidement aux changements de composants », explique David Ochoa.« La reproductibilité de la profondeur de pénétration s’est nettement améliorée. À la différence du positionnement pneumatique, nous pouvons agir sans arrêts mécaniques ».
La détection constante de la force et de la trajectoire identifie instantanément tout joint mal monté et l’affiche directement sur la station au moyen du logiciel d’exploitation basé sur un navigateur Web sous la forme d’un message NOK (incorrect). Des données de qualité peuvent être transférées par l’intermédiaire de différentes interfaces. L’application BSH est connectée au Smart Function Kit via TCP/IP. De plus, les données du processus sont également transférées au serveur cloud BSH en tant que fichiers JSON.« Grâce au gain de transparence de processus, nous pouvons surveiller en permanence la qualité, améliorer constamment les processus et éliminer plus rapidement les erreurs éventuelles », affirme Maximilian Aßmuth.« Nous créons entre autres des analyses de tendances afin de définir des zones de tolérance précises pour le processus en relation avec la conception ou la pièce elle-même ».
Entre-temps, le groupe BSH a étendu le concept fructueux à d’autres sites en Pologne, en Allemagne, en Turquie, en Inde et en Chine. En l’espace de trois ans, 21 Smart Function Kit Pressing ont été mis en service. Un second Smart Function Kit Pressing est souvent installé dans des stations plus récentes, ce qui amène le composant à la position zéro exacte par le bas et permet à la servopresse supérieure de travailler avec encore plus de précision.
Par rapport aux solutions pneumatiques précédentes, le concept électrique marque également des points en matière de durabilité :« Nous pouvons progressivement remplacer les systèmes pneumatiques restants en électrifiant successivement davantage d’opérations et de processus de montage. Dès que les compresseurs sont désactivés, l’efficacité énergétiques des lignes s’améliore soudainement », ajoute Maximilian Aßmuth.
Le changement technologique pour l’électromécanique est un succès total pour le groupe BSH.« Le Smart Function Kit Pressing a fonctionné de manière fiable dès la première minute avec plus de 99 % de pièces en parfait état », reporte David Ochoa depuis l’usine de La Cartuja. Et Maximilian Aßmuth est également très satisfait du pack mécatronique complet :« Grâce à l’approche de solution innovante de Bosch Rexroth, nous avons été en mesure de standardiser les tâches importantes de pressage et d’assemblage dans le monde entier de manière pérenne. Nous avons apprécié le fait que notre partenaire de solution était également ouvert aux suggestions d’optimisation, dont certaines ont été mises en œuvre dès la prochaine mise à jour du logiciel. Travailler de manière si étroite avec le client contribue également énormément au succès commun du projet »
.