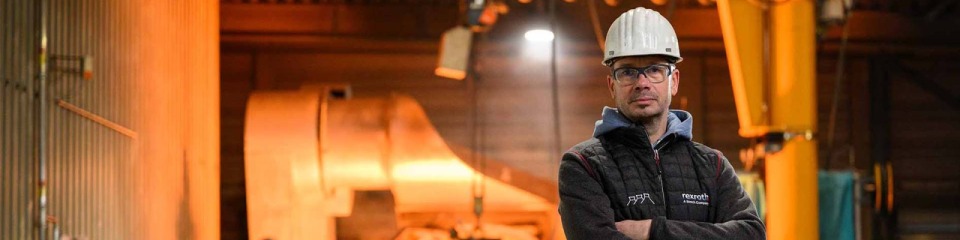
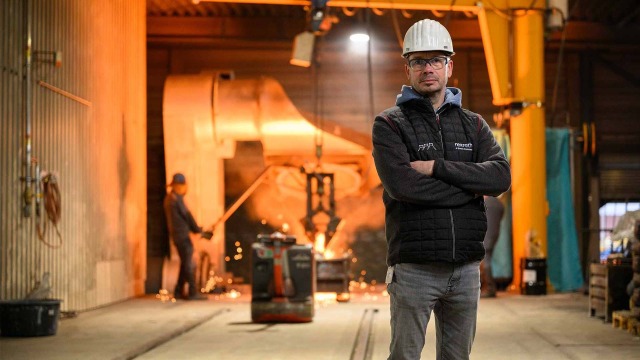
Chez Bosch Rexroth, nous sommes constamment à la recherche de moyens d’économiser de l’énergie. Découvrez quelques-unes des innovations récentes que nous avons mises en œuvre dans nos usines à travers le monde. Celles-ci démontrent qu’en alliant créativité et analyse minutieuse, il est possible d’améliorer l’efficacité énergétique.
Trouver de nouvelles façons de refroidir les matériaux
Dans notre usine de Lohr, en Allemagne, les pièces moulées hydrauliques sont fabriquées à partir de fontes de niveaux de qualité différents. Une partie de ce processus de production implique un traitement thermique particulier appelé « recuit », au cours duquel les pièces moulées sont chauffées à plus de 900 °C, puis refroidies selon des spécifications définies avec précision.
Cette étape de recuit nécessitant énormément d’énergie, nos spécialistes ont récemment trouvé une solution plus efficace sur le plan énergétique : la remplacer par une étape de refroidissement lent.
Notre nouvel espace de refroidissement nous permet d’éliminer le processus de recuit tout en nous aidant à réduire les émissions de dioxyde de carbone de notre fonderie de plus de 2 500 tonnes par an. Cela a un impact direct sur l’empreinte carbone de nos produits.
Droit d'auteur : Bosch Rexroth)
Moderniser le processus de fusion pour réduire la consommation d’énergie
Nous avons également installé notre troisième four de fusion à fréquence moyenne dans notre fonderie de Lohr. Ce nouveau four est doté d’une technologie de fusion de pointe, où tout est conçu pour une efficacité énergétique accrue. Il permet de remplacer nos trois fours existants.
Grâce à la digitalisation et à l’automatisation des processus de fusion, à la restructuration des flux de matériaux et à la diminution du transport du fer (et de la déperdition de chaleur qui en résulte), nous réduisons encore plus notre consommation d’énergie. La nouvelle configuration de notre fonderie nous permet d’économiser jusqu’à 2,9 GWh d’énergie électrique par an.
Droit d'auteur : Bosch Rexroth)
Passer au refroidissement central par l’eau
Les systèmes de réfrigération à compression sont un élément essentiel du processus de production des composants hydrauliques de notre usine de Pékin. Ils fonctionnent de la même manière que les réfrigérateurs ou les climatiseurs, c’est-à-dire que de l’air chaud est émis lorsque le système fonctionne. L’air chaud doit être évacué via le système de ventilation, ce qui implique une consommation d’énergie élevée.
Au cours de ses recherches en vue de déterminer la meilleure manière d’améliorer notre gestion de l’énergie, notre équipe s’est intéressée au réseau d’eau froide de l’usine, déjà utilisé pour refroidir d’autres machines et processus lors de la production. Elle a constaté que l’efficacité énergétique pourrait être considérablement améliorée en utilisant ce réseau d’eau froide existant pour refroidir les machines-outils installées. Les systèmes de réfrigération à compression pourraient être remplacés par un échangeur thermique raccordé au réseau d’eau froide.
Nous l’avons déployé lors d’une première phase au sein de cinq centres d’usinage, ce qui a permis de réduire la consommation d’énergie pour le refroidissement de plus de 80 % par rapport à la solution décentralisée, soit une économie annuelle d’environ 85 000 kWh.
Droit d'auteur : Bosch Rexroth)
Production de cartes de circuits imprimés : économiser de l’énergie à l’aide des rayons UV
Au sein du site de production de cartes de circuits imprimés de notre usine de Xi’an en Chine, les résines synthétiques sont maintenant durcies sans chaleur à l’aide des rayons UV, ce qui améliore considérablement les capacités de l’usine en matière d’économie d’énergie.
Au cours du processus de production, les cartes de circuits imprimés sont assemblées mécaniquement avec des composants électroniques, puis soudées. Après un test fonctionnel, les cartes de circuits imprimés assemblées sont recouvertes d’une couche de peinture pour protéger les composants électroniques des effets de l’environnement. Elles peuvent alors être utilisées dans le cadre d’applications industrielles.
Jusqu’à récemment, ce revêtement était séché à des températures avoisinant les 100 °C pendant 15-20 minutes, puis les cartes de circuits imprimés assemblées devaient refroidir pendant deux heures. Mais grâce à la technologie UV, l’équipe de production est parvenue à provoquer une réaction chimique en quelques secondes seulement. Résultat ? Plus de 80 % d’économie d’énergie par carte de circuit imprimé par rapport au processus précédent et une réduction du temps de séchage d’environ 90 %. Par ailleurs, ce procédé permet d’appliquer une couche de peinture plus épaisse afin de produire des cartes de circuits imprimés de meilleure qualité et de mieux les protéger.
Droit d'auteur : Bosch Rexroth)
Leo Pototzky
Directeur, Durabilité des opérations