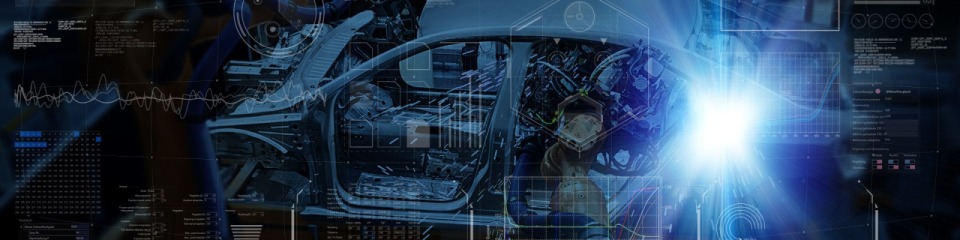
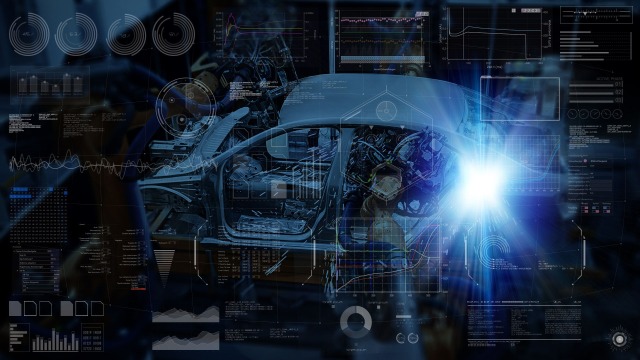
La connexion sera centrale dans les opérations de soudage de demain, dont la clé de voûte sera le système de contrôle du soudage. Auparavant, un intergiciel était couramment utilisé sous la forme d’une passerelle matérielle afin de permettre au contrôle de soudage de se connecter à d’autres dispositifs et systèmes, et de communiquer avec eux. Grâce à Bosch Rexroth, ce dispositif intermédiaire n’est plus nécessaire : l’intelligence est directement intégrée au système de contrôle de soudage PRC7000. Cette solution tout-en-un inédite, conforme avec l’Industrie 4.0 et intégrant les protocoles MQTT et OPC UA, est maintenant disponible pour les opérations de soudage par résistance. Elle permet de réduire les coûts et de satisfaire aisément aux exigences en matière de connectivité, tout en ouvrant le champ des possibles pour les applications avec IA.
Le processus de soudage génère d’énormes quantités de données qui peuvent servir de base pour l’optimisation des processus, l'apprentissage automatique et la création de valeur dans l’Industrie 4.0. Cependant, ces données doivent d’abord être collectées, analysées et traitées. C’est le seul moyen de produire des informations détaillées et exploitables, et de lancer ensuite des actions automatiquement définies.
Avec le protocole OPC UA, les données sont envoyées sur le cloud et analysées, puis le feedback est envoyé au système de contrôle. Cela permet d’envisager l’implémentation d’applications d'apprentissage automatique ou d’intelligence artificielle (IA), par exemple. La collecte et l’analyse des données permettent de tirer des enseignements pour la mise en place de l'apprentissage automatique, d’apporter des améliorations et de réduire drastiquement les coûts de contrôle qualité.
La norme de communication ouverte OPC UA revêt une importance croissante dans les usines numériques. Elle constitue l’un des protocoles de communication les plus importants pour l’IoT et devient maintenant la norme de l’industrie. Le protocole OPC UA fait non seulement transiter les données de vos machines, mais il les décrit également de façon sémantique dans un format lisible par machine. Cela permet de prendre en charge l’IA et l'apprentissage automatique.
Avec le système de contrôle de soudage PRC7000, Bosch Rexroth commercialise la première solution de ce type intégrant entièrement le protocole OPC UA. La demande en la matière est croissante, notamment chez les constructeurs automobiles, qui souhaitent également voir l’utilisation du protocole de réseau ouvert MQTT se généraliser.
En plus du serveur OPC UA, le système PRC7000 intègre un éditeur MQTT. Les deux sont disponibles en tant que logiciels sous licence. Le protocole MQTT est conçu pour les environnements avec une bande passante faible et une forte latence. Il est idéal dans les situations où vous avez besoin d’envoyer d’énormes quantités de données sous forme de paquets. Par exemple, avec un système de contrôle, plus de 30 000 points de soudage peuvent être enregistrés par jour et leurs données transmises. Le système de contrôle transmet les données au format JSON, un format de données textuelles autodescriptif qui peut être interprété.
PPMP est un autre protocole fondé sur le format JSON. Il s’agit d’une nouvelle norme ouverte de l’industrie développée par Bosch à des fins d’échange de données dans un environnement connecté. Le protocole PPMP permet de connecter les systèmes d’exécution de fabrication (MES). C’est le cas du gestionnaire de performance de production (PPM) Nexeed de Bosch, par exemple. Les anciens systèmes de contrôle de soudage n’étaient pas conçus pour mettre en œuvre des protocoles tels qu’OPC UA et MQTT, car ils n’étaient pas assez puissants. Des intergiciels ou des logiciels de passerelle, avec matériel propre requis ou non, étaient nécessaires pour l’échange de données entre le dispositif et la périphérie du réseau ou la couche du cloud. Les données étaient collectées, agrégées et envoyées par l’intergiciel.
Avec le système PRC7000, aucun matériel intermédiaire n’est nécessaire, car les protocoles OPC UA et MQTT sont intégrés directement au système de contrôle. L’intégrité des données est cruciale pour les usines automatisées de demain. Le cryptage des données doit donc être possible sur la base d’un certificat.
Avec les interfaces MQTT et OPC UA, le nouveau système de contrôle de soudage PRC7000 offre la connectivité IoT nécessaire pour la mise en œuvre de l’Industrie 4.0. Il possède également d’autres fonctionnalités en matière de connectivité et d’applications intelligentes. En tant que logiciel de pointe, le système PRC7000 fournit les performances requises pour répliquer les cas d’utilisation de l’IA.
Les fonctions conformes à l’Industrie 4.0 du système PRC7000 prennent en charge de nombreux cas d’utilisation et de nouveaux modèles économiques. Grâce à l’accès OPC UA, les petites entreprises de fabrication de machines peuvent facilement développer et fournir leur propre interface utilisateur. Les tendances en matière d’interruptions ou les causes de dysfonctionnements peuvent également être identifiées, et des applications de prévisions peuvent être mises en place afin d’optimiser les processus et de réduire les coûts.