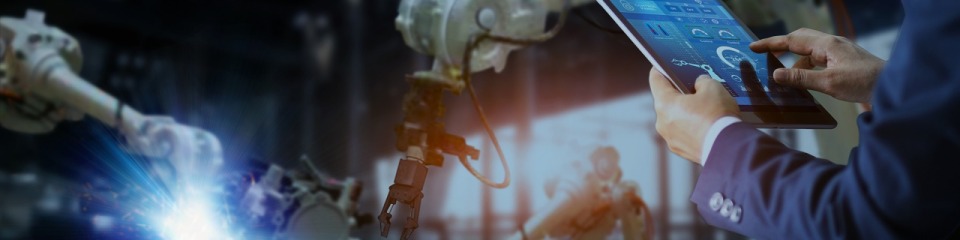
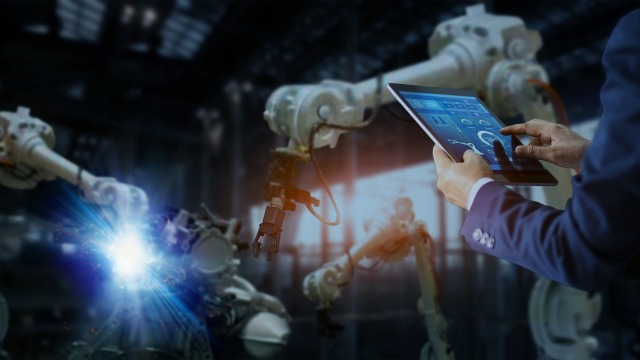
Pourquoi un système de contrôle de soudage doit-il être compatible avec l’Industrie 4.0 ? Le soudage génère d’énormes volumes de précieuses données qui peuvent servir de base pour l’optimisation des processus, l’apprentissage automatique et la création de valeur. Pour cela, les données doivent d’abord être collectées, analysées et traitées. Les normes standard d’accès à ces données sont MQTT et OPC UA. Bosch Rexroth regroupe ces deux types de communication dans le kit « Connecteur IoT ». Cela permet aux utilisateurs de traiter les données collectées selon leurs besoins et d’implémenter la connexion automatique pour l’assurance qualité, par exemple.
Le contrôle de soudage PRC7000 est prêt pour l’Industrie 4.0 grâce au kit « Connecteur IoT » qui combine les types de communication MQTT et OPC UA.
Le système de contrôle fonctionne comme un dispositif de traitement combiné à une passerelle de communication. Le connecteur IoT rend les données disponibles à d’autres fins, pour les évaluations statistiques ou la connexion permanente, par exemple. L’un des objectifs est de réaliser des économies en matière de gestion de la qualité et de maintenance préventive. Il s’agit de priorités qui prennent de plus en plus d’ampleur dans le domaine du soudage par résistance : dans l’industrie automobile pour la construction de caisses en blanc, par exemple, ou encore dans le domaine des fournisseurs de rang 1 ou de l’ingénierie mécanique.
Les deux types de communication sont incontournables dans leur domaine respectif : MQTT en tant que protocole de réseau ouvert et OPC UA en tant que norme de communication pour l’automatisation.
MQTT est conçu pour les environnements à bas débit et latence élevée. Il est idéal pour l’envoi de gros volumes de données par paquets. Par exemple, un système de contrôle peut stocker et envoyer jusqu’à 30 000 points de soudure par jour. Le contrôle PRC7000 envoie les données au format JSON, un format texte autodescriptif qui peut être interprété par les opérateurs.
OPC UA peut non seulement acheminer des données machine, mais aussi les décrire de manière sémantique dans un format lisible par machine. De cette manière, les données peuvent être envoyées sur le nuage et analysées, puis le résultat est renvoyé au système de contrôle. C’est la base des applications qui abordent l’apprentissage automatique et l’intelligence artificielle (IA).
Les deux normes sont disponibles dans le connecteur IoT. La fonctionnalité de base du système de contrôle de soudage PRC7000 comprend un éditeur MQTT ainsi qu’un serveur OPC UA. L’étendue des données peut être augmentée avec une licence, ce qui permet d’accéder à plus d’applications potentielles.
Les anciens systèmes de contrôle de soudage n’étaient pas conçus pour mettre en œuvre des protocoles tels qu’OPC UA et MQTT, car leurs performances étaient insuffisantes. Un intergiciel ou un logiciel de passerelle, qui pouvait nécessiter son propre matériel, devait donc être connecté entre le dispositif et la périphérie du réseau ou la couche du nuage. Les données étaient collectées, agrégées et envoyées par l’intergiciel.
Le connecteur IoT prend en charge l’intégration verticale à partir du dispositif de traitement vers le nuage ou la périphérie du réseau, par exemple. En tant que système ouvert, il n’est pas soumis aux structures de propriété et fournit donc une communication de pointe. Les utilisateurs peuvent traiter les données selon leurs besoins. Le contrôle PRC7000 inclut par défaut une étendue de données définie, par exemple, pour l’évaluation OK / NOK.
Le kit d’extension permet d’obtenir un flux de données plus important et donc d’ouvrir la porte à de nouveaux cas d’utilisation. Le connecteur IoT peut ainsi être utilisé pour déterminer plus de 200 valeurs réelles par point de soudure. Il peut s’agir de valeurs de qualité, de données brutes de courbes de soudage, de différents paramètres tels que des points de consigne, des paramètres et des courbes de références, et de modifications de données. Lorsque ces valeurs sont combinées à l’évaluation d’autres données source, des concepts de maintenance préventive peuvent être mis en œuvre. D’autres avantages contribuent à assurer la transparence en permettant aux utilisateurs d’identifier et d’exploiter le potentiel d’optimisation. La connexion automatique peut être implémentée dans un but d’assurance qualité, les modifications de paramètres enregistrés permettent d’analyser la qualité des points de soudure, et le statut dans l’atelier de carrosserie peut être consulté dans les informations relatives aux paramètres.
L’industrie d’aujourd’hui a besoin d’une production polyvalente et flexible, apte à répondre à ses besoins qui évoluent de manière dynamique. Il lui faut donc des solutions adaptables qui prennent en charge la mise en réseau et garantissent la cohérence. Bosch Rexroth apporte la solution dont l’industrie moderne a besoin : le connecteur IoT. Grâce à celui-ci, les commandes de soudage PRC7000 et PSI6000 de Bosch Rexroth peuvent être étendues afin de répondre aux besoins de l’Industrie 4.0 et d’exploiter les richesses de vos données.
Découvrez le système de contrôle du soudage par résistance PRC7000 nouvelle génération.