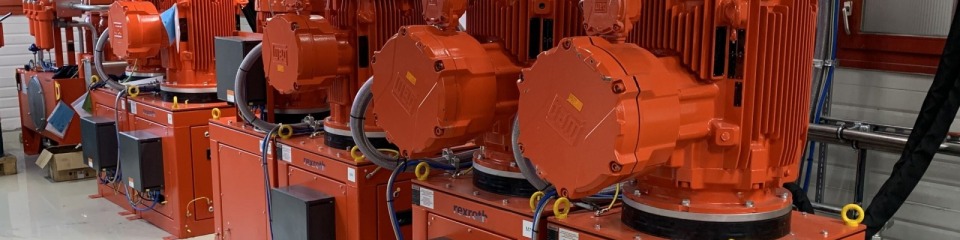
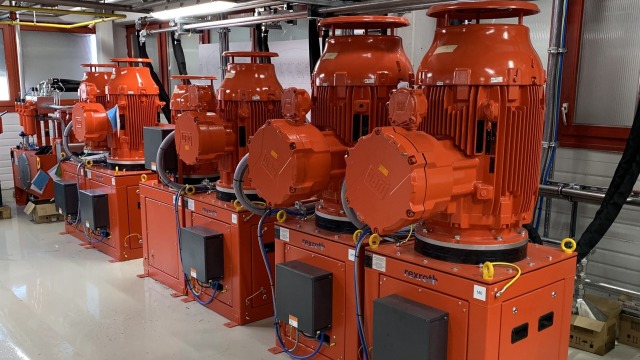
Pendant longtemps, les plus de 20 agitateurs et mélangeurs utilisés par la société Stahl dans l’usine de Leinfelden pour produire des matériaux de base pour des revêtements haute performance ont consommé beaucoup d’électricité. Grâce à une solution hydraulique innovante de Bosch Rexroth, l’installation de production fonctionne désormais avec une efficacité énergétique de 60 %. Dans le même temps, l’entreprise bénéficie d’une sécurité et d’une qualité de processus plus élevées.
Il existe des produits que peu de gens connaissent, bien qu’ils soient indispensables dans leur vie quotidienne. Ces champions cachés sont, par exemple, des revêtements de haute performance pour les chaussures, les vêtements, le textile de maison ou la décoration intérieure des voitures. La société Stahl, qui produit des centaines de formules dans son usine de Leinfelden près de Stuttgart, est considérée comme le leader mondial dans le domaine de ces revêtements performants.
La réussite des processus sensibles de réaction, de mélange et de dispersion dépend directement de la vitesse de rotation des moteurs hydrauliques montés sur les 23 agitateurs de l’installation. Selon l’étape du processus, les entraînements hydrauliques doivent produire un couple d’arbre aussi constant que possible sur de longues distances, mais aussi un niveau de force beaucoup plus élevé parfois. Afin de représenter le fonctionnement normal et les pics de puissance le plus efficacement possible sur le plan énergétique, Stahl a chargé Bosch Rexroth de moderniser l’hydraulique.
Les revêtements haute performance confèrent entre autres des propriétés particulières aux chaussures (source d’image : Stahl)
La raison concrète du développement du nouveau concept d’entraînement a été l’arrêt de la production de l’ancien fabricant de moteurs hydrauliques, ce qui a finalement compromis l’approvisionnement en pièces de rechange. Pour trouver une alternative, Stahl s’est tourné vers le fournisseur régional Hydrobar de Sindelfingen, qui fait partie du réseau de partenaires Certified Excellence de Bosch Rexroth. En raison des exigences complexes, Hydrobar a recommandé d’adresser la demande directement à la division Rexroth Hägglunds.
Outre les moteurs hydrauliques, l’alimentation centralisée en cours d’exploitation devait être progressivement remplacée par un concept d’entraînement plus efficace. „Nous avons remarqué que la consommation électrique de l’installation n’était pas corrélée à la charge de travail“, rapporte Miquel Forcadell, chef de projet chez Stahl à Leinfelden. „Les mesures de consommation correspondantes ont montré un potentiel d’économie de plus de 60 %, ce qui correspond à une économie d’énergie d’environ 15 % par rapport à l’ensemble de l’usine. Cette économie auprès des plus grands consommateurs de notre site était la ligne directrice du projet.“
Jalon de la stratégie ESG : le site de Staaahl à Leinfelden économise au total 15 % d’électricité et d’émissions de CO2 grâce au nouveau concept hydraulique de Bosch Rexroth (source d’image : Stahl)
La grande disparité entre l’énergie produite et l’énergie réellement utilisée était due à l’approvisionnement en énergie central existant, dont la capacité n’était initialement prévue que pour sept agitateurs. Les pompes hydrauliques à entraînement électrique produisaient une pression élevée constante qui consommait en permanence beaucoup d’électricité. Mis à part des pics de puissance occasionnels, le système a été limité par des soupapes, de sorte qu’une grande partie de l’énergie hydraulique a été convertie en chaleur.
„Dans le cadre de notre stratégie ESG, nous travaillons en permanence à l’identification des gros consommateurs et à l’optimisation de leurs besoins en énergie“, explique Salvatore Alfieri, responsable du site. En outre, avec ce projet de modernisation, Stahl voulait rendre les processus de production transparents et mieux contrôlables. La saisie et la mise à disposition de toutes les données d’entraînement à la commande supérieure permettent d’optimiser davantage les processus à l’avenir.
Mais les exigences du projet étaient encore plus complexes : outre les objectifs de durabilité et de numérisation, Bosch Rexroth devait développer un concept d’entraînement, qui prend en compte, outre les opérations d’agitation en fonction des besoins, les conditions de travail dans différentes zones ATEX. De plus, le nouveau système hydraulique devait être installé et mis en service pendant la production. Bosch Rexroth a répondu à ces exigences complexes avec un concept sur mesure, a repris la conception et a notamment livré neuf moteurs à pistons radiaux de la série AMX de Hägglund pour les réacteurs à haut rendement à fonctionnement lent. Ceux-ci sont nettement plus compacts et plus puissants que la solution précédente. En outre, l’alimentation en huile pour les 23 entraînements a été remplacée par de nouveaux groupes compacts, tous les modules haute pression fonctionnant avec des pompes à vitesse contrôlée.
Parmi les deux unités d’alimentation centrales, une unité de pompage est réalisée de manière redondante. Comme l’une des deux salles de machines se trouve dans la zone Ex, les groupes compacts installés dans cette zone ont été réalisés en version ATEX. Les variateurs de fréquence Rexroth sont utilisés pour la commande précise des entraînements hydrauliques à vitesse variable. Hydrobar, partenaire d’excellence certifié, a assuré la tuyauterie exacte de l’installation et assure la maintenance.
Du point de vue de Stahl, le projet Engineered-to-Order a été un franc succès. En seulement cinq mois, Bosch Rexroth et les partenaires mandatés pour les différents corps de métier ont réussi à remplacer les moteurs hydrauliques et les entraînements à vitesse variable. „Après la préparation de la tuyauterie et du système électrique, y compris les variateurs de fréquence, l’agitateur concerné a été séparé du réseau à pression constante existant le week-end pendant la période sans production“, le chef de projet Forcadell décrit la procédure progressive. „Les agitateurs modernisés pouvaient généralement être remis en service après trois jours.“
Pour une mise en œuvre dans les délais, Bosch Rexroth a aidé l’équipe de montage à installer les nouveaux moteurs hydrauliques et les groupes compacts selon les besoins. „Malgré sa complexité, le projet a été mis en œuvre très rapidement, en particulier du côté de la direction. La tuyauterie d’Hydrobar était exemplaire. Chaque installation a été très bien préparée, testée et remise clé en main toujours plus rapidement. Les six derniers moteurs ont été remplacés en une semaine.“
Depuis cette armoire de commande, les variateurs commandent les groupes compacts à vitesse variable Rexroth pour l’alimentation en fluide des moteurs hydrauliques (source d’image : Stahl)
Les économies d’énergie prévues ont également pu être réalisées dans leur intégralité. „Le projet multi-technologie de Bosch Rexroth a constitué un nouveau jalon dans notre feuille de route ESG“, a déclaré Alfieri. „L’économie réelle par rapport à l’ancien système à pression constante est de 60 %, ce qui signifie que l’ensemble de l’usine consomme 15 % d’électricité en moins. Grâce à l’approche à vitesse variable pour une alimentation électrique adaptée à la demande, la consommation d’énergie absolue reste à un niveau bas constant. Même avec une charge élevée des agitateurs, il n’y a plus de fluctuations, de sorte que la sécurité du processus est garantie en permanence.“
„Étant donné que la commande moderne fournit exactement la puissance requise pour chaque étape du processus, nous pouvons garder les conditions d’agitation sous contrôle à tout moment“, ajoute le chef de projet Forcadell. „De cette façon, nous bénéficions d’une reproductibilité élevée du processus de production et d’une qualité constante de nos produits tout en maintenant une efficacité énergétique optimale. "Forcadell est également satisfait de la stabilité. Le dimensionnement des agrégats compacts avec une pompe redondante est juste. À ce jour, il n’y a pas eu un seul arrêt.“
Léger et puissant : le nouveau moteur à pistons radiaux Hägglunds AMX (à droite) est nettement plus compact que le moteur hydraulique précédent (à gauche).(Source d’image : Stahl)
Grâce à la nouvelle commande numérique des entraînements hydrauliques, Stahl dispose désormais de nombreuses informations numériques pour l’analyse et la documentation des processus de production. „Nous sommes en train de construire un système de contrôle des processus pour visualiser tous les paramètres“, explique Alfieri. „Le savoir personnel devient ainsi transférable. Les informations obtenues sur des paramètres spécifiques et l’analyse rapide des erreurs simplifient la production de manière durable.“
Grâce à l’hydraulique à commande numérique de Bosch Rexroth, Stahl peut désormais optimiser la qualité du processus de manière ciblée via la vitesse de rotation. Un effet secondaire bienvenu de la modernisation est le fonctionnement nettement plus silencieux des nouveaux moteurs hydrauliques Hägglunds et des groupes compacts dans les salles des machines. Si l’agitateur raccordé ne nécessite aucune puissance, le groupe haute pression concerné est complètement désactivé. Dans l’unité de service centrale, les pompes d’alimentation sont automatiquement activées en fonction des besoins. Ce mode veille réduit à la fois le niveau sonore et la consommation d’énergie.
Après la modernisation réussie des entraînements hydrauliques, une nouvelle ère s’est ouverte pour les responsables de la production sur le site de Stahl à Leinfelden. „Le projet de durabilité et de numérisation a durablement amélioré la stabilité et la transparence des processus dans le domaine des revêtements haute performance“, résume Alfieri. „Ce n’était pas un projet facile, mais la performance et la collaboration de Bosch Rexroth et des partenaires impliqués étaient excellentes. Toutes les exigences ont été réalisées dans les délais et le budget prévus.“