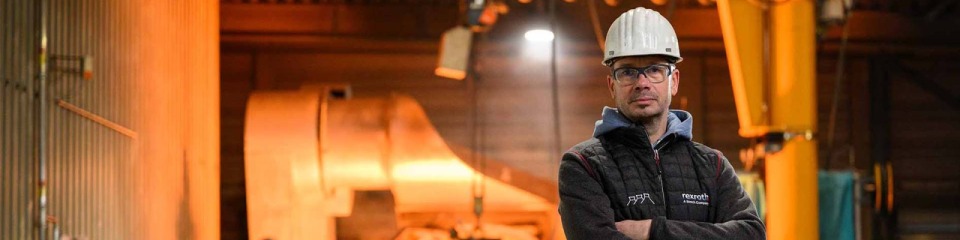
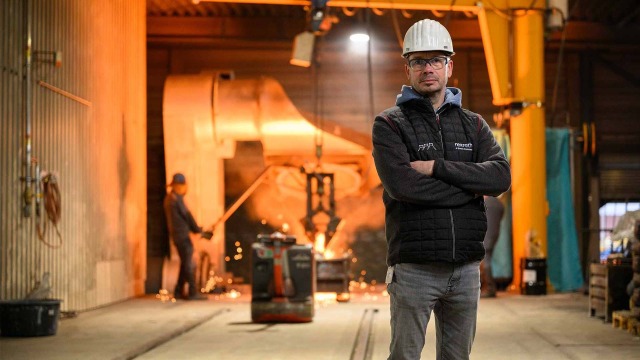
Hos Bosch Rexroth er vi stadig på jakt etter måter å spare energi på. Oppdag noen av de siste innovasjonene vi har implementert i anleggene våre over hele verden – som viser frem hvordan man gjennom kreativ tenkning og grundig analyse kan bidra til økt energieffektivitet.
Nye måter å kjøle ned på
I Lohr-anlegget i Tyskland produseres hydrauliske støpegods i flere forskjellige kvaliteter av støpejern. En del av denne produksjonsprosessen involverer en spesiell varmebehandling kalt «gløding», hvor støpestykkene varmes opp til over 900 °C, og deretter kjøles ned i henhold til nøyaktig definerte spesifikasjoner.
En enorm mengde energi brukes til gløding, men nylig har ekspertene våre funnet en mer energieffektiv måte – å erstatte glødingen i denne prosessen ved å bremse nedkjølingen.
Vårt nye kjølehus gjør at vi kan eliminere glødeprosessen, og hjelper oss å redusere karbondioksidutslippene i støperiet vårt med mer enn 2500 tonn per år. Dette har en direkte innvirkning på karbonfotavtrykket til våre produkter.
(Bilde til høyre: Bosch Rexroth)
Reduksjon av energiforbruket ved å modernisere smelteprosessen
Vi har også installert vår tredje nye smelteovn med middels frekvens på Lohr-støperiet vårt. Den nye ovnen har toppmoderne smelteteknologi, der alt er designet for økt energieffektivitet. Dette gjør det mulig å erstatte tre eksisterende ovner med denne nye.
Ved å digitalisere og automatisere smelteprosessene, restrukturere materialstrømmen og redusere transporten av jern – og dermed det resulterende temperaturtapet – reduserer vi energibruken ytterligere. Det nye oppsettet i vårt smelteverk gjør at vi kan spare opptil 2,9 GWh elektrisk energi per år.
(Bilde til høyre: Bosch Rexroth)
Bytte til sentral vannkjøling
Kompresjonskjølesystemer er en sentral del av produksjonsprosessen for hydrauliske komponenter i anlegget vårt i Beijing. Disse fungerer på samme måte som kjøleskap eller klimaanlegg, med varm luft som slippes ut mens systemet er i gang. Den varme luften må fjernes gjennom ventilasjonssystemet, noe som betyr et høyt energiforbruk.
Teamet vårt så på hvordan de kunne forbedre energistyringen, og henvendte seg til det eksisterende kaldtvannsnettverket til anlegget, som allerede brukes til å kjøle ned andre maskiner og prosesser i produksjonen. De fant ut at energieffektiviteten kunne forbedres betraktelig ved å bruke dette eksisterende kaldtvannsnettverket til å kjøle ned installerte verktøymaskiner. Kompresjonskjøleanleggene kan erstattes med en varmeveksler koblet til kaldtvannsnettverket.
Vi rullet dette ut i første fase, hvor fem maskineringssentre ble omgjort, noe som førte til redusert energiforbruk til kjøling med over 80 % sammenlignet med den desentraliserte løsningen – tilsvarende årlige besparelser på ca. 85 000 kWh.
(Bilde til høyre: Bosch Rexroth)
Kretskortproduksjon: spare energi med UV-stråling
Ved produksjonsanlegget for kretskort i Xi'an-anlegget vårt, Kina, herdes nå syntetiske harpikser uten varme ved bruk av UV-stråler, noe som forbedrer betydelig anleggets energisparingsevne.
Under produksjonsprosessen monteres trykte kretskort (PCB) mekanisk med elektroniske komponenter og loddes. Etter funksjonstesting blir det sammensatte trykte kretskortet (PCBA) belagt med lakk for å beskytte elektronikken mot ytre miljøpåvirkninger. Dette gjør det egnet for bruk i industrielle bruksområder.
Inntil nylig ble dette belegget tørket med temperaturer på ca. 100 °C i 15–20 minutter, før PCBA-kort måtte avkjøles i to timer. Men ved å bruke UV-teknologi, kan produksjonsteamet forårsake en kjemisk reaksjon i løpet av sekunder, spare over 80 % per PCB i energibruk sammenlignet med den tidligere prosessen og redusere tørketiden med ca. 90 %. Ikke bare det, men prosessen gjør det mulig å påføre et tykkere lakkbelegg, noe som betyr høyere beskyttelse og bedre kvalitet på kretskortene de produserer.
(Bilde til høyre: Bosch Rexroth)
Leo Pototzky
Direktør, driftsmessig bærekraft