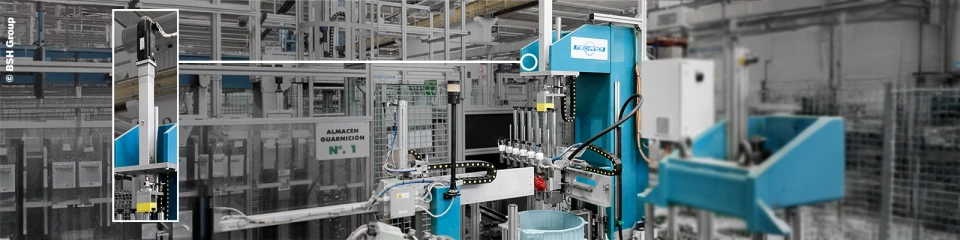
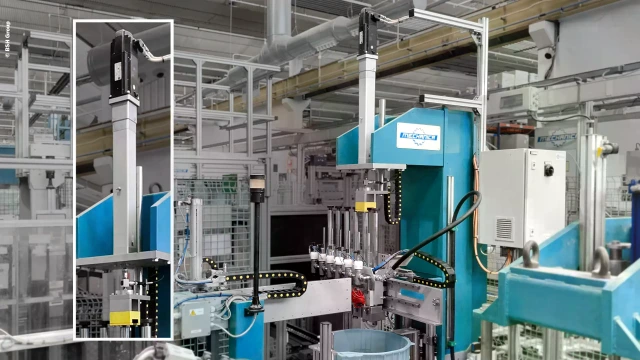
BSH Hausgeräte standardisiert qualitätskritische Press- und Fügeprozesse in der Waschmaschinenfertigung. Wie? Mit dem mechatronischen Subsystem Smart Function Kit Pressing. Ergebnis: mehr Flexibilität, Stabilität und Transparenz bei minimalem Zeitaufwand für Engineering, Integration und Qualitätskontrolle.
Für Maximilian Aßmuth, Industrial Engineering Team Wäschepflege bei BSH Hausgeräte, haben die neu eingeführten elektromechanischen Servopressen auf Basis des Smart Function Kit Pressing entscheidende Vorteile gegenüber den bisher eingesetzten pneumatischen Lösungen: Sie ermöglichen hochpräzise Prozesse, sparen Energie ein und schaffen eine verlässliche Basis für Qualitätssicherung und weitere Prozessoptimierung. Warum? Weil die elektromechanischen Servopressen das elektrisch erzeugte Drehmoment über den Gewindetrieb im elektromechanischen Zylinder EMC direkt in Bewegung umsetzen, fein zu steuern sind und die Prozessdaten mittels Sensor und Software exakt erfassen können. Eben diese Vorteile macht sich BSH zu nutze, um die Prozesse im weltweiten Produktionsnetz wirtschaftlicher zu gestalten.
Maximilian Aßmuth
Industrial Engineering Team Wäschepflege bei BSH
Der Startschuss für das internationale Standardisierungsprojekt fiel mit dem ersten Smart Function Kit Pressing für das Werk im spanischen La Cartuja bei Zaragoza. Die mechatronische Lösung besteht aus einem elektromechanischen Zylinder mit Kraftsensor, einem Servomotor mit Antriebsregler und einem Industrie-PC mit vorinstallierter Bediensoftware. In der Waschmaschinenfertigung wird die smarte Servopresse dazu genutzt, eine funktionskritische Dichtung zwischen Trommelwelle und Wassertank, die das Wasser in der Maschine hält, zuverlässig zu fixieren. Dank des vormontiert gelieferten Komplettpakets und guter Vorbereitung stellte sich der Projekterfolg schnell ein. Nach nur drei Tagen inklusive Testlauf nahm die leistungsfähige Kombination aus Einpresstechnik, Software und Service zuverlässig ihren Betrieb auf.
Das erste Smart Function Kit Pressing bei BSH Hausgeräte ging 2021 im Werk La Cartuja bei Saragossa in Betrieb. Weltweit sind mittlerweile über 20 Servopressen in Betrieb. (Bildquelle: BSH Gruppe)
Heute werden in La Cartuja vor allem Hausgeräte für bekannte Marken wie Bosch, Siemens, Gaggenau oder Neff produziert. Der spanische Standort mit rund 400 Mitarbeitenden gehört zu einem weltweiten Produktionsverbund von 37 Werken mit rund 60.000 Mitarbeitenden. Das Smart Function Kit Pressing spielt darin eine wichtige Rolle bei der Prozessstandardisierung, ebenso wie die weltweite Präsenz von Bosch Rexroth. „Nach der Evaluierungsphase hat sich das Smart Function Kit als die am besten geeignete und auch kostengünstigste Lösung herausgestellt. Die einfache Bedienung bewährt sich vor allem in Nachtschichten, wenn das Bedienpersonal keinen Zugang zum technischen Support hat“, erklärt David Ochoa, Prozessingenieur bei BSH.
Schon vor der Inbetriebnahme am Einsatzort spart das Smart Function Kit Pressing wertvolle Engineeringzeit ein. Denn mit den intelligenten eTools von Bosch Rexroth lässt sich das mechatronische Subsystem innerhalb weniger Minuten digital auslegen, konfigurieren und über den Rexroth Shop bestellen. Im Anschluss an die vormontierte Lieferung der Servopresse in einem Paket führt die browserbasierte Bediensoftware mittels Wizard Schritt für Schritt durch die Inbetriebnahme. Die Prozessdefinition erfolgt visuell anhand von Bausteinen, die grafisch aneinandergereiht und parametriert werden. Auch die Linienintegration ist dank vorbereiteter Funktionsbausteine schnell erledigt. Ergebnis- und Prozessdaten werden direkt über das Dashboard visualisiert und lassen sich über unterschiedliche Schnittstellen an verschiedene Systeme übertragen.
Das Smart Function Kit Pressing spart Zeit vom Engineering bis zur Betriebsphase. Auslegung, Konfiguration und Bestellung erfolgen rein digital, die vorinstallierte Bediensoftware reduziert den Aufwand für Inbetriebnahme, Prozessdefinition und Linienintegration. (Bildquelle: Bosch Rexroth)
Mit dem Smart Function Kit Pressing lassen sich drei Arten von Anwendungsfällen im Kraftbereich von 2 bis 70 kN realisieren: Fügen auf Position, Fügen auf Kraft oder Fügen auf Kraft mit anschließendem Halten. Im BSH Werk La Cartuja wird die Dichtung auf Position gefügt. Dazu wird sie zunächst in das Lagergehäuse gepresst. Nachdem der Dichtring der Achse zugeführt wurde, fährt die Presse in einer kurzen Taktzeit auf die produktspezifisch vorgegebene Position.
Wird per RFID eine neue Variante erkannt, überträgt die Liniensteuerung automatisch die relevanten Parameter wie Wege, Kräfte und Toleranzen an die Servopresse. „Dank der digitalen Prozesssteuerung können wir sehr schnell auf Bauteiländerungen reagieren“, erklärt Ochoa. „Die Wiederholgenauigkeit der Eindrücktiefe hat sich deutlich verbessert. Im Gegensatz zur pneumatischen Positionierung können wir auf mechanische Anschläge verzichten.“
Die konsequente Kraft- und Wegerfassung identifiziert jede nicht korrekt montierte Dichtung sofort und zeigt diese über die browserbasierte Bediensoftware direkt an der Station als NOK-Meldung an. Die Übertragung der Qualitätsdaten ist über verschiedene Schnittstellen möglich. Unter anderem ist eine BSH Applikation über TCP/IP mit dem Smart Function Kit verbunden. Darüber hinaus werden die Prozessdaten auch als JSON-Dateien an den BSH Cloud Server übertragen. „Durch die gewonnene Prozesstransparenz können wir die Qualität lückenlos überwachen, Abläufe kontinuierlich optimieren und mögliche Fehler schneller beheben“, sagt Aßmuth. „Wir erstellen unter anderem Trendanalysen, um genaue Toleranzfelder für den Prozess in Bezug auf das Design oder das Bauteil selbst zu definieren.“
Inzwischen hat BSH das erfolgreiche Konzept auf weitere Standorte in Polen, Deutschland, der Türkei, Indien und China ausgeweitet. Innerhalb von drei Jahren wurden 21 Smart Function Kit Pressing in Betrieb genommen. In neueren Stationen wird häufig noch ein zweites Smart Function Kit Pressing installiert: Dieses bringt das Bauteil von unten exakt in die Nullposition, wodurch die obere Servopresse noch präziser arbeiten kann.
Im Vergleich zu früheren pneumatischen Lösungen punkten die elektrischen auch unter dem Aspekt der Nachhaltigkeit: „Indem wir sukzessive weitere Montagevorgänge und Prozesse elektrifizieren, können wir die verbleibenden pneumatischen Anlagen nach und nach ersetzen. Sind die Kompressoren erst einmal abgeschaltet, verbessert sich die Energieeffizienz unserer Linien schlagartig“, so Aßmuth.
Der Technologiewechsel zur Elektromechanik ist für BSH ein voller Erfolg. „Das Smart Function Kit Pressing arbeitet seit dem ersten Tag zuverlässig mit über 99 Prozent Gutteilen“, berichtet David Ochoa aus dem Werk La Cartuja. Und auch Maximilian Aßmuth ist sehr zufrieden mit dem mechatronischen Komplettpaket: „Dank des innovativen Lösungsansatzes von Bosch Rexroth konnten wir weltweit wichtige Press- und Fügeaufgaben zukunftssicher standardisieren. Gut gefallen hat uns auch die Offenheit unseres Lösungspartners für Verbesserungsvorschläge, die teilweise direkt im nächsten Softwareupdate umgesetzt wurden. Diese Kundennähe trägt wesentlich zum gemeinsamen Projekterfolg bei.“