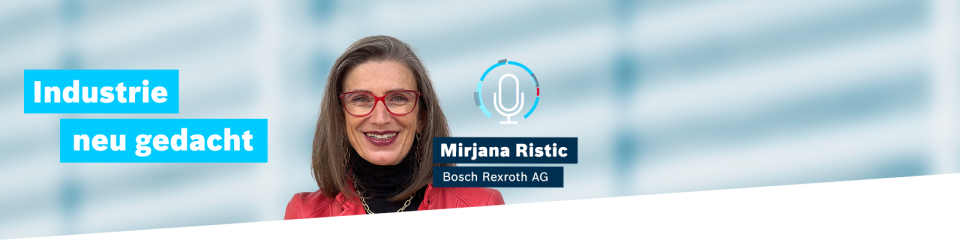
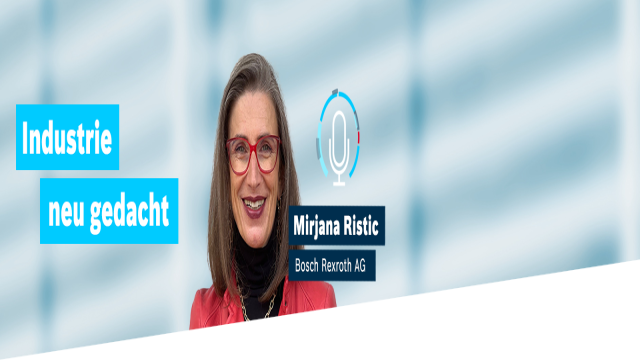
Energy costs are exploding for many manufacturing companies, and at the same time many entrepreneurs are wondering: how secure is the power supply? For several years, experts have been discussing and researching an "old" technology that promises better energy efficiency and more self-sufficiency, reduction from industrial power consumption from the utility grid as well as its quality - direct current (DC). The implications for automation: with a global DC grid, classic rectifiers are eliminated, which in turn reduces conversion losses, and drive systems become more compact, less material-intensive. Also an increasing use of protection, circuit technology and of DC/DC converters at the consumers with DC supply as well as at integration of regenerative energy sources and energy storage will then be necessary. The software solutions such as network and energy or power management as well as design tools finally ensure the above-mentioned promise of this technology.
According to research by Dr Mirjana Ristic in the context of technology scouting on DC technology and the results of the publicly funded project DC-INDUSTRIE, there is great potential for energy savings in this technology: "Industry consumes about 45 percent of the electricity in Germany, about 70 percent of which is accounted for by drive systems. If we start there, we can achieve great efficiency gains." At the German Electrical and Electronic Manufacturers' Association (Zentralverband Elektrotechnik und Elektronikindustrie e.V., ZVEI), experts calculate an energy savings potential of about ten per cent, according to industry sources. The cost effect is estimated at about 20 percent. This is mainly due to the saving of AC (alternating current) to DC converters on the motors. The average system availability can also be increased to around 98 per cent, they add.
In addition, the potential of DC technology can be better exploited or even increased by intelligently combining it with other new technologies and methods such as artificial intelligence, communication technologies, digitalisation or virtualisation.
In addition, the factory will become a prosumer in the future. The artificial word stands for producer and consumer - i.e. energy producer and consumer. Today, the factory draws energy from the external AC grid, which is then converted to the DC grid. Internally, consumers such as machines and drives or motors as well as energy storage units are connected via a DC grid. The availability of a large roof area at most factory sites makes it possible to generate one's own electricity through photovoltaic (PV) systems. These can be connected to a DC grid with minimal losses, so that the electricity demand can be covered proportionally from self-generation. This leads to fewer grid failures, more flexibility and greater self-sufficiency.
The first local DC grids are already emerging in factories. Robot cells or press lines, for example, already use a DC supply. One example: with conventional solutions, the braking energy of the robots or presses cannot be fed back into the AC grid; it is destroyed in the braking resistors or converted into heat. The equipment or control cabinets must be cooled and air-conditioning units must regulate the temperature in the production halls. With a DC network, the process-related braking energy can either be made directly available to other DC network participants (axes, devices or machines) or buffered for the time being in a suitable energy store and thus not destroyed in braking resistors. Consequently, a significantly lower cooling power is required in such systems, both for control cabinet and motor cooling. Local DC networks are already used in industry, in the form of a DC axis or DC machine network. A larger DC network extension to factory level brings further advantages and possible solution concepts. Today, Ristic sees a simplified connection and increased use of regenerative energies as the advantages of DC technology that are currently coming to the fore. There is a growing trend among many companies to generate their own energy, i.e. through photovoltaic systems on their factory roofs. With an internal DC grid, the energy could be used directly, stored or even fed back into the supply grid. This increases the degree of flexibility and self-sufficiency of production sites, at the same time relevant cost savings are possible through peak shaving, and the reduction in average electricity consumption achieved is a plus point for sustainability.
Research has qualified and quantified the technological potentials and delivered sound results, including a holistic system concept. "The demand is also there, now we have to think in terms of industrial solutions," says Ristic. And the DC discussion does not only have a European dimension. Industry representatives in other world regions are also working on DC strategies. "We will certainly see hybrid systems of AC and DC for the first time - especially in the brownfield, because implementation in stages enables a technologically risk-minimised transition," says Ristic. The already established local DC networks can then gradually expand to the complete factory.
You can find this and other episodes on the factory of the future in our tech podcast channel "Industry rethought" on all known platforms or you can subscribe directly here via Podigee (only available in German).
Contact person for the Bosch Rexroth Tech Podcast: Susanne Noll
Please feel free to contact Bosch Rexroth!