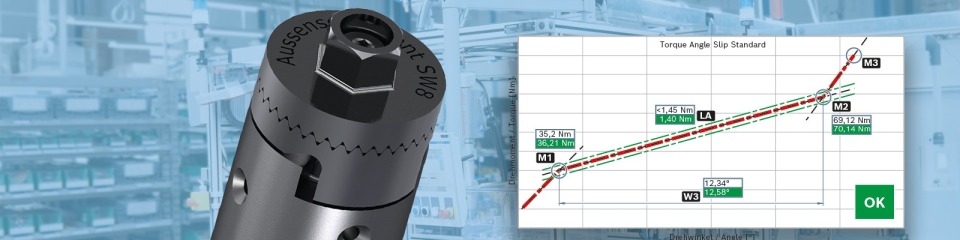
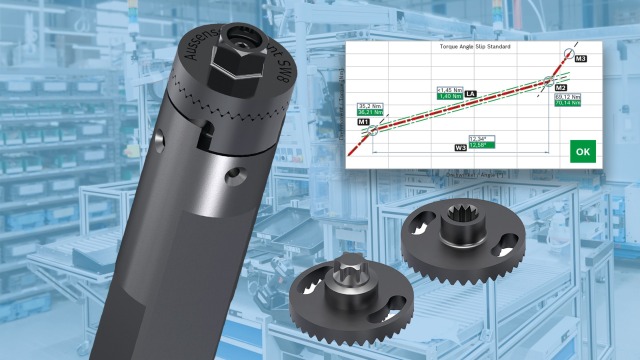
Innovative TASS testing system ensures assembly quality and productivity directly during the process
With Bosch Rexroth’s TASS testing system for tightening systems, manufacturing companies can ensure assembly quality and productivity directly during ongoing processes. Compared to previous testing practices, the on-the-fly process is significantly more effective and efficient. This means that the intervals between machine capability tests can be extended, which saves time and money. TASS testing systems are available for all stationary tightening spindles and wired hand-held nutrunners from Bosch Rexroth and can be operated directly at the workstation without any additional equipment or specialist personnel.
Be it for the plastics industry, automotive or mechanical engineering – the importance of functionally relevant and safety-critical bolted connections is growing. For manufacturing companies, this means walking a fine line: they have to provide evidence of faultless assemblies while also manufacturing profitably. The tightening tools use have to be tested regularly to maintain the required tolerances and to exclude liability risks or damage to the company’s reputation. The challenge is that standard testing procedures are relatively time-consuming, interrupt the workflow and cut down productivity.
The innovative TASS testing system resolves the conflict between quality testing and productivity by mapping tightener testing directly during the assembly process. This occurs with the help of a mechanical torsion element and evaluation software that runs directly on the tightening control unit IndraLogic, for example on the CS351 compact system or the KE350 communication unit.
For the on-the-fly test, the torsion element is “bolted” between the real components as part of typical assembly with a certain angle of rotation and a low tightening speed. For the right frictional or locking fit in the workpiece fixture, Bosch Rexroth delivers torsion elements in five sizes and thus covers a torque range from 1 Nm to 600 Nm.
During the testing process, the control unit records the bolt connection and transfers the process data to the TASS software, which compares the stored target curve of the standardized torsion element with the recorded characteristic curve and displays “OK” or “NOK” as the measurement result. Optionally, the test result can also be transmitted to a superordinate system.
Thanks to seamless process integration, any testing frequency can be realized, for example twice per day or once per shift. Additionally, TASS tests can be integrated quickly and easily in the line and, in doing so, allow comprehensive testing of the entire tightening system including output.
Additionally, using regular on-the-fly tests, the intervals between time-consuming machine capability tests can be set to enable optimal manufacturing without any risk to quality.
Media Assets
Basic Information Bosch Rexroth
As one of the world’s leading suppliers of drive and control technologies, Bosch Rexroth ensures efficient, powerful and safe movement in machines and systems of any size. The company bundles global application experience in the market segments of Mobile Applications, Machinery Applications and Engineering, and Factory Automation. With its intelligent components, customized system solutions and services, Bosch Rexroth is creating the necessary environment for fully connected applications. Bosch Rexroth offers its customers hydraulics, electric drive and control technology, gear technology and linear motion and assembly technology, including software and interfaces to the Internet of Things. With locations in over 80 countries, more than 31,000 associates generated sales revenue of around 6.2 billion euros in 2021.
Basic Information Bosch
The Bosch Group is a leading global supplier of technology and services. It employs roughly 402,600 associates worldwide (as of December 31, 2021). The company generated sales of 78.7 billion euros in 2021. Its operations are divided into four business sectors: Mobility Solutions, Industrial Technology, Consumer Goods, and Energy and Building Technology. As a leading IoT provider, Bosch offers innovative solutions for smart homes, Industry 4.0, and connected mobility. Bosch is pursuing a vision of mobility that is sustainable, safe, and exciting. It uses its expertise in sensor technology, software, and services, as well as its own IoT cloud, to offer its customers connected, cross-domain solutions from a single source. The Bosch Group’s strategic objective is to facilitate connected living with products and solutions that either contain artificial intelligence (AI) or have been developed or manufactured with its help. Bosch improves quality of life worldwide with products and services that are innovative and spark enthusiasm. In short, Bosch creates technology that is “Invented for life.” The Bosch Group comprises Robert Bosch GmbH and its roughly 440 subsidiary and regional companies in some 60 countries. Including sales and service partners, Bosch’s global manufacturing, engineering, and sales network covers nearly every country in the world. With its more than 400 locations worldwide, the Bosch Group has been carbon neutral since the first quarter of 2020. The basis for the company’s future growth is its innovative strength. At 128 locations across the globe, Bosch employs some 76,100 associates in research and development, of which more than 38,000 are software engineers.
Press Contact
Spokesperson technology topics
Manuela Kessler
+49 9352 18-4145
Manuela.Kessler@boschrexroth.de