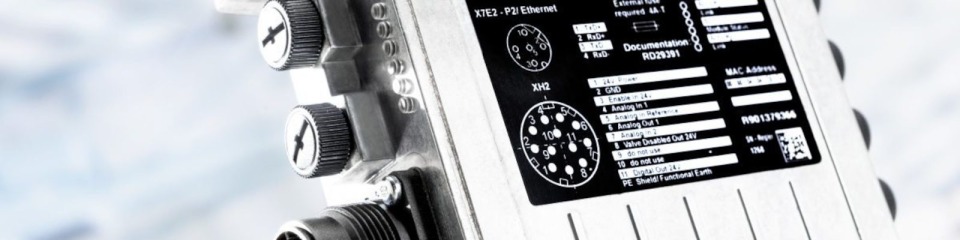
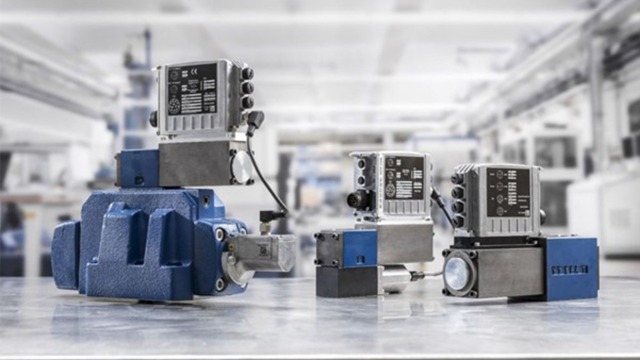
What are the current market requirements for hydraulic valves?
We are currently experiencing a transition from classic, analogous hydraulics to connectable digital fluid technology. European machine manufacturers in particular are increasingly digitizing their machine designs and expect that hydraulics can be seamlessly embedded into these connected environments. This means that regarding the level of automation, hydraulics are on a par with electromechanical drives. One of the decisive features in this respect is the seamless integration of intelligent hydraulic valves into different automation topologies via open standards such as multiple Ethernet interfaces.
Which new technical possibilities are available to meet these requirements?
Smart single-axis controllers are already remotely regulating hydraulic motions in a closed control loop. In addition, a powerful motion control is integrated into the on-board electronics of the valve. It performs the target-actual comparison on site and regulates accurately to a few micrometers. The control quality of the system is exclusively determined by the resolution of the measurement systems. These motion controls without control cabinet are increasingly used in saw lines, paper mills and machine tools. In addition, there are smart variable speed pump drives and smart pump controls. They provide completely new possibilities of replacing the throttle controls, which were predominantly used up to now, by more energy-efficient displacement controls. In this way, functions which were previously executed by valves are relocated to the software.
What about the integration of sensor technology into hydraulic valves?
The mass production of sensors for the automotive or the consumer products industry has significantly reduced the costs. Now, sensors are increasingly used in hydraulics. In our opinion, the integration of sensor technology of this kind into existing valve housings is the next step. Regarding condition monitoring, sensors could collect information on fluid quality, temperature, vibrations and performed switching cycles. Via deep learning algorithms, users can then detect wear before it causes malfunction.
Which other possibilities of mechanization does a valve provide?
The degree of freedom regarding connection geometries is already limited by standard requirements. The hydraulics industry discussed the topic of digital hydraulics in great depth some time ago. The idea was and is to control flows in a “stepped” or “clocked” way using single- or multi-bit strategies. In certain applications, this can constitute an advantage compared to continuously variable technology.
Which other innovations in hydraulic valves are relevant in your company?
It is no longer a question whether hydraulic valve technology will benefit from connectivity or not. The only question is when. The current discussions around Industry 4.0 clearly show how important it is to define all required functions and functionalities. Only if mechanisms and sensor technology are standardized across different manufacturers will active connectivity and communication be possible. Even in the future, not every hydraulic-mechanical pressure valve will have digital electronics on board or be connected to a control system or other valves. An imprinted QR code with information on the manufacturer’s settings, functional descriptions or information on replacement seals are a first step towards connectivity. In the area of new materials and production technologies, Rexroth has many innovations in the pipeline. 3D printing of cores for cast housings or direct printing considerably lowers energy consumption during the operation of valves. While the divisibility of the core mold had to be taken into account in the design of the core, this is no longer necessary today thanks to core printing. This means that we can use other channel designs which allow for lower pressure losses and improve energy consumption. For a valve with a flow of 10,000 l/min, the reduction of flow resistance by 10 to 20 percent significantly reduces the operating expenses.
How do these trends affect your products?
With the IAC (integrated axis controller) valves, Bosch Rexroth offers motion control without control cabinet which is completely integrated into valve electronics. It can be fully connected via open interfaces. The same applies to servo-hydraulic axes with their own fluid circuit. In these ready-to-mount axes, pump, valves and cylinders form an assembly to which the machine manufacturer only has to connect power supply and control communication. They use the same commissioning tools and user interfaces which means that all drive technologies provide the same look and feel. Classic servo valves, however, can also be improved further. New plug-in amplifiers with pulse width modulation for on/off valves by Rexroth reduce the surface temperature of the connectors by more than 80 degrees to only 50 degrees. This is particularly interesting for saw lines where easily inflammable sawdust constitutes an explosion hazard.
Outlook: How will valve technology change in the next 10 years?
In 10 years, valves will allow for easier project planning, more comfortable commissioning and more efficient operation and will provide more information before a service case. If service is required, the valve may already have ordered its spare parts.