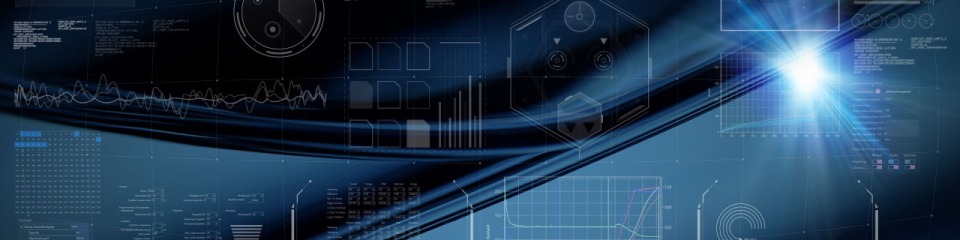
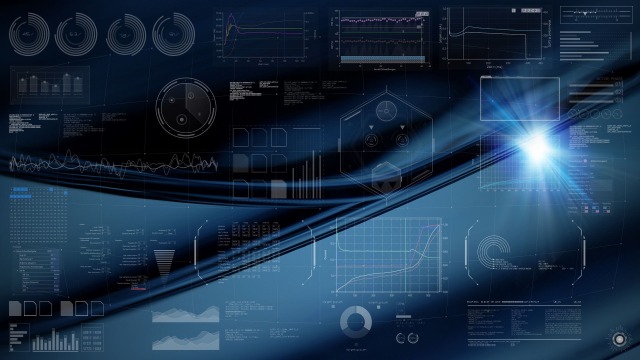
ある車両が、世界6つの工場、8 生産ラインで、4車種で生産される予定です。これは、12万個を超える溶接スポットのパラメータを決定し、入力し、最適化し、有効化する必要があることを意味します。この例は、抵抗スポット溶接の需要がいかに高いかを表わしています。しかも、状況はますます複雑化しています:軽量化などのトレンドが続く中、プロセスの安定性や生産性に関する新たな課題も常に予見されます。ここでは、たとえば、材料の組み合わせに迅速かつ動的に適応する溶接制御システムが必要とされています。
320個の部品、80種類の異なる板金とさまざまな厚さのコーティング - この結果、500もの材料と厚さの組み合わせが、5,000か所の溶接スポットで接合されることになります。これが今の代表的な車体です。しかも、需要は常に高まっています。つまり自動車製造のトレンドは、ますます軽量でより安全な車両へと向かっています。その理由のひとつとして、軽量化により燃費やCO2排出量が削減される点が挙げられます。また自動車メーカーにとっては、材料の使用量を減らすことで、生産コストの削減につながります。同時に、設計フォームはますます複雑化し、衝突安全に関する要件も満たさなければなりません。
異なる材料の組合せにより、要求の厳しい溶接作業数は増加し続けています。自動車業界では、同じ生産ラインで生産される車種やモデルがますます増加しています。これらはすべて、溶接制御やモニタリングに関する要件だけでなく、試運転にも直接影響を及ぼしています。
必要な軽量化設計を実現するために、ここ数年、自動車構造では、腐食防止コーティングを施した高強度鋼材の使用がどんどん増加しています。高強度鋼材を使用すると、同じ機械的特性を持ちながらも、薄い壁厚のコンポーネントを設計できます。しかし、これらの材料は通常、抵抗スポット溶接中にクラックが入る可能性が高くなります。
もう1つの課題は、アルミニウムと鋼鉄の持つ極端な物理的特性が、抵抗スポット溶接を使用してこの2つを接合することを難しくしている点です。鋼鉄は電気抵抗が高く、アルミニウムは抵抗が低いためです。ボッシュ レックスロスの新しい高性能溶接制御システムPRC7000は、この両極端に対応することができます。変圧器が、溶接制御システムの出力電力を、手元の溶接作業に合わせて正確に変換します。
PRC7000を使用すると、鋼鉄からアルミニウムまで、異なる板厚と材料の組み合わせを簡単に処理できます。これを可能にするために、新しい溶接制御システムは、適応制御機能と柔軟なプログラマブル性を使用しています。そのため、完璧な溶接スポットの再現も可能です。
ある大手自動車メーカーでは、初めて抵抗スポット溶接を使用して、新車のシャシー(車台)に多数のアルミニウム部品を接合しました。この場合、本体はアルミニウム製で、異なるアルミニウム板の組み合わせで、約2,000か所の溶接スポットを必要とします。
PRC7000の最新バージョンでは、たとえば、ガンデータモジュールにより、ガン本体でプロセス信号をデジタル化することができます。手動ガンは利用可能なすべての制御システムで操作可能で、制御システムを再度パラメータ化する必要はありません。データは、完全な溶接作業としてガンデータモジュールに保存され、その後、多くのインターフェースを介さず制御システムに送信することができます。これにより、ユーザーの自由度および新しいユースケースへの自由度が増え、コスト削減が可能になります。
PRC7000溶接制御システムにより、自動車メーカーは、抵抗スポット溶接の非常に動的な要件を、効率的かつ柔軟に、最高の品質基準に従って満たすことができます。経済性、処理の安定性、生産性だけでなく、競争力も保証されます。