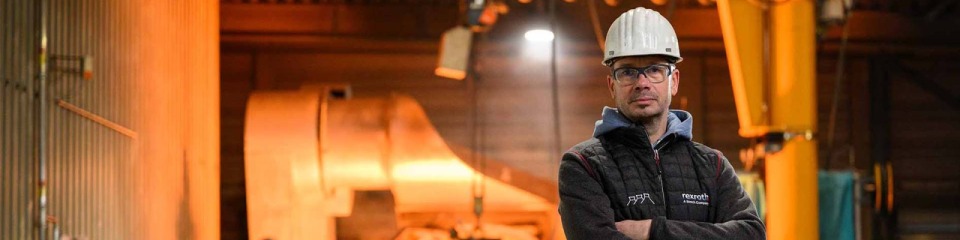
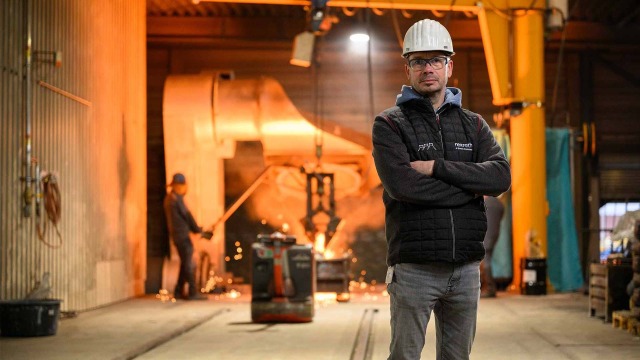
ボッシュ レックスロスは常に省エネを追求しています。世界中の工場で導入された最新の技術革新のいくつかを紹介します。創造的な思考と慎重な分析により、エネルギー効率の向上にどのように貢献できるかをご覧ください。
クールダウンの新手法
ドイツのローア・インダストリーの工場では、油圧機器向けの鋳物は数種類の異なるグレードの鋳鉄で製造されています。この製造工程の一つとして、900°C以上に加熱した後、精密に定められた仕様に従って冷却する「焼なまし)」という特殊な熱処理工程が含まれています。
焼なましには膨大な量のエネルギーが使用されていますが、当社の専門家はよりエネルギー効率の高い方法を発見しました。冷却のスローダウンにより工程から焼なましを排除したのです。
当社の新たな冷却棟は、焼きなまし工程の排除を実現し、これにより鋳造所の二酸化炭素排出量を年間2,500トン以上削減できます。これは当社製品のカーボンフットプリントに直接的な影響を与えます。
(画像:ボッシュ レックスロス)
溶解工程の近代化によるエネルギー使用量の削減
第三の中周波溶融炉をローア・インダストリーの鋳造工場に設置しました。この新たな炉は最先端の溶解テクノロジーを誇り、すべてが省エネ向上のためにデザインされています。これにより、古い炉三基がこの新炉一基に置き換えられます。
溶解工程のデジタル化と自動化、原料の流れの再構築、鉄の運搬の低減、ひいては熱損失の低減により、エネルギー使用量をさらに削減しています。これらの溶解工場の新しい設備により、年間最大2.9GWhの電気エネルギーが節約できるようになりました。
(画像:ボッシュ レックスロス)
中心水冷却への切り替え
中国の北京工場の油圧構成部品の製造工程では、圧縮式冷凍システムが重要な役割を果たしています。冷蔵庫やエアコンと同様に、システムが稼働すると温風が放出されます。温風は換気システムを介して取り除く必要がありますが、これは高いエネルギー消費量を必要とします。
当社のチームは、どのようにエネルギー管理を改善できるかを検討し、工場の既存の冷水網に目を向けました。これはすでに他の機械や製造工程の冷却に使用されています。この既存の冷水網を使用して設置された工作機械を冷却することで、エネルギー効率の大幅改善が可能であることが判明しました。圧縮式冷凍システムは、冷水網に接続されたオイルクーラーで置き換え可能でした。
第一段階では5つのマシニングセンターを変更し、分散型ソリューションと比較して冷却用エネルギー消費量を80%以上削減しました。これは、年間約85,000kWhの節減に相当します。
(画像:ボッシュ レックスロス)
回路基板製造、UV照射による省エネを実現
中国の西安工場の回路基板製造工場では現在、合成樹脂を紫外線を利用して熱を使わずに硬化させることで、工場の省エネ性能を大幅に向上させています。
製造工程では、プリント基板(PCB)が電子部品と機械的に組み合わされてはんだ付けされます。機能試験の後、組み立て済みのプリント基板(PCBA)は外部環境の影響から電子機器を保護するために塗料でコーティングされます。そのため、これは工業用途にも適しています。
最近までこのコーティングは、プリント基板(PCBA)を2時間冷却する前に、約100℃の温度で15~20分間乾燥させていました。しかし紫外線テクノロジーを用いることで、数秒で化学反応を起こし、従来の工程と比較してPCB当たりのエネルギー使用量を80%以上削減し、乾燥時間を約90%短縮できました。そればかりではなくこの工程によって、より厚い塗料コーティングの使用が可能になったため、保護性を高め、生産される回路基板の品質も向上しました。
(画像:ボッシュ レックスロス)
レオ・ポトツキー
オペレーショナル・サステナビリティ担当 取締役