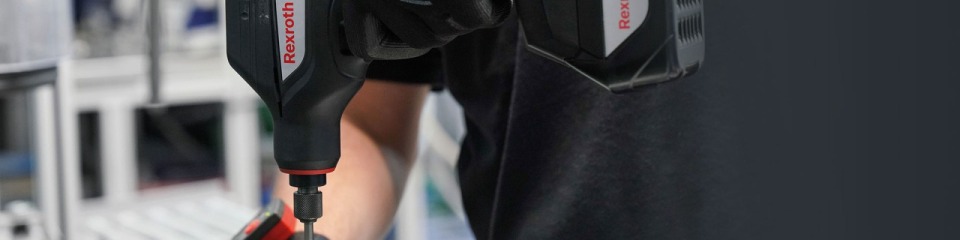
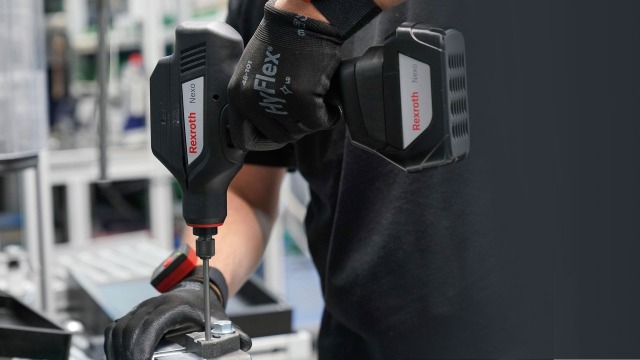
コネクテッドインダストリーの産業生産環境への導入に関連するより有望なブレークスルーの1つは、製造における分散型インテリジェンスからもたらされるイノベーションです。これは、製造企業に、製造施設を静的なものから非常に柔軟な生産システムに変換する機会を提供します。
生産サイクルの短縮、対応時間の短縮が、モバイルファシリティモジュールの運用で実現します。インテリジェントなコードレスタイトニングツールと組み合わせると、特に変化の大きい市場において柔軟性と生産性が向上するため、決定的な強みとなります。本記事では、インテリジェントなバッテリーツール、ボッシュ レックスロス Nexoコードレスナットランナーがどのようにタイトニングアプリケーションで効率性の高い多機能な生産を実現するのかについて説明します。
オートメーションシステムと言えばこれまでは、一元集中型のインテリジェンスを用いてトップダウンで設計され、下流の生産マシンをすべて制御していました。このようなシステムはステーションPLCと通信し、次に各生産マシンと通信するラインPLCで構成されるのが一般的でした。タイトニングシステムの場合は、こうしたマシンは各チャネルから情報を収集して指示を出すタイトニングコントローラで構成されます。このシステムでは明らかにセットアップで膨大な量のリソースを要するため、変更が難しく、柔軟性もありません。このシステムは、同じ製品を大量生産するのは得意です。
インダストリー4.0アプリケーション向けの分散型制御インテリジェンス:タイトニングテクノロジーでは実用化済み。
インダストリー4.0環境では、バッチサイズ単位が1であっても対応できるような柔軟性が求められます。変更を効率よく実施するには、ロジック決定をなるべくローカルで行うことが重要です。
トップダウン型のアプローチを廃して、ローカルレベルの分散型インテリジェンスを使用すると、生産需要の変動に対して生産ラインで対応できるようになります。ロジック決定を複数まとめて実行するローカルコントローラを組み合わせたバーコードスキャナーなどをローカルで追加できるインテリジェンスを使用すると、複雑な課題に対しても効率性と柔軟性の高いソリューションが得られます。
バーコードスキャナーとコントローラを統合したNexoが生産現場の課題を処理できた経緯を実際にあった事例で説明しましょう。
あるお客様が、M8ボルトを使う12のタイトニングアプリケーションとM6ボルトを使う18のタイトニングアプリケーションが必要な4つの製品を持っていました。このお客様はコストをミニマイズしたかったため、作業すべてを1つのツールで済ませたかったのです。ツールが2つ必要なうえに、バーコードスキャナーまで追加するのは避けたかった。
ソリューションとなったのは、M8ボルトとM6ボルト両方のトルクレンジをカバーするNexoモデルでした。これだけです。このアプリケーションに指定されたNexoナットランナーは、タイトニングジョイント(ボルト)の検出に内蔵バーコードスキャナーを搭載されていたものでした。ロジックの決定に加えて、ドキュメントにアセンブリの部品のタイプとシリアル番号を添付することにより、バリューストリームが増加します。
このアプローチ、つまり ローカルのロジック決定のためにバーコードスキャナーを組み合わせたNexoのメリットとは、 上流のPLCを再プログラミング、構成することなく、複雑なタスクに柔軟性と効率性をもたらす能力にありました。
Nexo採用のメリットはこれだけではありません。多くの組立環境では、 ラインバランシング のニーズがありました。つまり、組立タスクをあるステーションから別のステーションに再配置して、生産フローを能率的に変更することが頻繁にありました。タイトニングツールに関連したラインバランシングについてですが、コントローラを組み合わせたタイトニングシステムを採用すると、既存のコントローラを取り外したり、トレイや付属デバイスの各種ケーブルの接続を解除し、そのすべてを新しい場所に再配線したり、さらには電源供給、アース接続、コントローラへの通信回線接続、ツールケーブルの新規敷設などが起こり得ます。Nexoコードレスナットランナーを使用すると、新しい組立場所にツールを導入するのと同じくらいに、タスクがシンプルになります。ケーブルがありませんから、配線で頭を使うこともなくなります。プラグアンドプレイと言って差支えない高度にソフィスティケートされたシステムです。リーン製造は、これ以上望めないレベルに達しました。
高度なタイトニングシステムでも、分散型インテリジェンスなら、ワイヤレスにモバイルにマッピング可能。だからこそラインバランシングがスムーズに進みます。
特に 安全性にリスクのあるアプリケーション に使えるタイトニングシステムとして、Nexoナットランナーはそのほかのボッシュ レックスロスのタイトニング製品と同様に、単にタイトニングして、オペレーション中のトルクや角度値をレポートするだけにとどまりません。ラインコントロールから信号を送受信する機能を使用して、ワイヤレス通信を備えたこのバッテリーツールは、製造プロセスに垂直統合された他の有線マシンと同じように動作します。たとえば、ポカヨケシステムにフル統合すると、 エラーゼロ生産 に貢献できるでしょう。適切にパラメーター化すると、各種パーツが組立ラインに正しく存在するのか検出できます。たとえばタイトニング作業であれば、ボルトにはワッシャを組み合わせる必要があります。不正な(過大な)角度値によってワッシャの欠落が検出されます。誤ったねじ長のボルト検出にも使用できます。
インテリジェントなNexoとバーコードスキャナーを組み合わせると、各IDの複数入力からなる新たなIDが付与されます。そのため、製品の組立ラインのさまざまなパーツでスキャンされたIDコードで記録できます。このIDコードは、この組立アプリケーションのタイトニング結果として最終文書にも記載されます。また、 トレーサビリティ に関しては、タイトニングプロセスで高い透明性が達成されます。製品不具合が発生すると、収集データのレビューによって不具合の原因が特定されます。必要であれば、不良品回収を個別に行い、回収量を低減できます。
まとめると、必要なパーツの所在や使用順序、求められるスペックの範囲に収まるタイトニング、パーツが次の組立ステーションに進むまでにボルト欠落がないことを保証するような集中型のPLCとは違います。それを制御するのがインテリジェントなコードレスナットランナー、Nexoです。