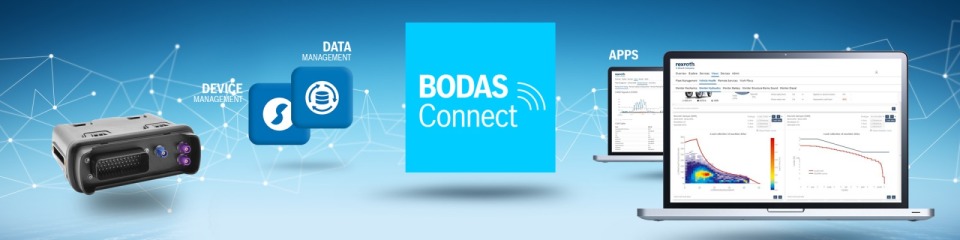
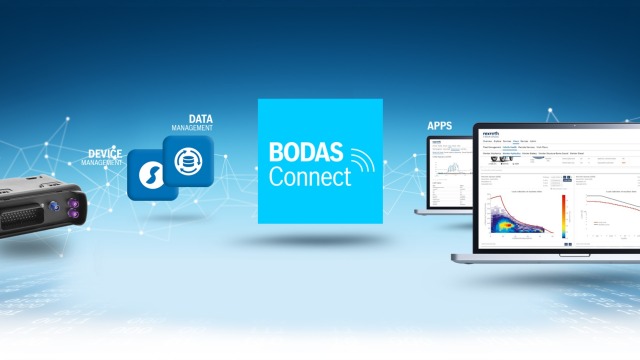
Products
OverviewIndustries
OverviewService
OverviewCompany
OverviewProduct groups
OverviewEngineering
OvervieweConfigurators and Tools
OverviewManufacturing automation solutions
OverviewPartner
OverviewJob opportunities
OverviewIoT data are regarded as the “new oil”. But what does this mean for vehicle data in the off-highway segment? They too are extremely valuable. While manufacturers would like to strengthen their competitive position and safeguard their aftersales business, operators would like to improve their productivity and the economy of their mobile machines on a permanent basis.
If a manufacturer has done its telematics homework “under the bonnet”, i.e. has chosen a future-proof telematic control unit (TCU), implemented software for efficient data collection and transmission and taken care of device management (including over-the-air services, remote diagnostics, monitoring etc.), things can get going. The data now need to be prepared for specific target groups and visualized. But the interests of the various groups involved are very different:
User-based dashboards for various roles in the company
Fleet and operations managers want a quick overview of their vehicles, their location and their status in order to refuel or maintain them if necessary. A customized dashboard and the automatic forwarding of relevant performance data should also relieve the administrative burden on them, e.g. as a result of use-based billing.
Service staff use their specific dashboard in order to provide quick remote support in the event of damage. They need a detailed insight into the machine in order to diagnose faults over the air, to change parameters which help to maintain productivity, to initiate software updates or to order spare parts without delay.
Telematics provides the development team with the data needed to continually improve product quality and machine design. For a more detailed evaluation, the telematics solution must record the actual load collectives and user behavior.
User-based dashboards via drag & drop
In spite of the different perspectives, all three groups have one common concern: They need customized dashboards in order to find, review and evaluate the right information quickly. The question regarding the basic functions of the telematics solution applies here too: Should a company program the dashboard itself, have it programmed or use standard building blocks?
BODAS Connect – All-in-One Connectivity: A coordinated off-the-shelf solution including connectivity, device management and data management. The logical separation of device and user data improves security, usability and cost-effectiveness.
For the frontend, there are ready-to-use off-highway modules which allow manufacturers and web agencies to create customized dashboards and functions cost-effectively. For example, the toolbox for the end-to-end telematics solution BODAS Connect All-in-One Connectivity contains among other things easy-to-adapt visualization tools. On the basis of off-highway-specific apps, standard dashboards and widgets, user-based cockpits can be created simply by dragging & dropping ready-to-use modules. At the same time, the complete solution is so flexible that OEMs can integrate their own know-how in the form of algorithms, programs and scripts which they have written themselves.
The relevant dashboards can easily be created using configurable, tailored widgets and other elements. The look and feel of the frontend can also be adapted to the desired corporate design with just a few clicks. At the same time, the toolbox offers standard interfaces for cloud-to-cloud communication, via which user-based billing for example can be triggered in another system.
The added value that data management delivers during the day-to-day work of construction machinery, farming equipment or municipal vehicles ultimately depends on the application experience of the solution provider. The following three use cases show the various time and cost benefits as a result of using the adaptable off-the-shelf solution BODAS Connect All-in-One Connectivity.
Drag & drop: Creation of dashboards via preconfigured, customizable modules
Monitoring for fleet managers, operations managers and service staff: The Machine Info app monitors important operating parameters and warns in the event of deviations from the target/actual figures. As a result, refueling, oil changes and other maintenance work can be planned and initiated easily.
Fleet and operations managers want to know the status of their fleet at a glance and identify acute need for action. In the event of a fault, they need to isolate the cause quickly and take appropriate steps to eliminate the fault. Monitoring the relevant operating figures and passing on performance data to ERP and billing systems for use-based billing and documentation helps to relieve the administrative burden. This is important in the municipal sector, among others, but also in forestry and agricultural engineering, where contractors document their performance for the client and as proof for EU subsidies.
Fleet and operations managers mainly use apps such as Vehicle Tracking, Geo Fencing & Curfew (theft prevention), Machine Info (monitoring operating parameters), Usage Scheduling (planning vehicle use and driver assignment) and Conditional Action (automatic triggering of actions and notifications for automatic reports). In order to visualize the data provided via the apps on suitable dashboards with minimal effort, the complete solution from Bosch Rexroth offers a comprehensive self-service kit. This includes ready-to-use rich text modules, widgets and modules for statistics, tables, graphs and charts.
Bosch Rexroth allows service staff and product managers to get a deep insight into the subsystems of a vehicle. Remote tools such as CAN Tracing, Diagnostics, Analytics & Measurement or Flashing OTA allow quick troubleshooting. All information from these and many other standard and customer-specific apps can be provided for role-based dashboards via easy-to-adapt frontend modules.
The information obtained using monitoring and diagnostic apps is also very useful for engineering, sales and service. For example, the machine design can be optimized on an ongoing basis using real load collectives and usage data. At Bosch Rexroth, users can also create suitable dashboards for this with just a few clicks.
Conclusion: Get onto the market more quickly with off-the-shelf modules
For their day-to-day work, fleet managers, service staff and product managers require role-based frontends with the right information and functions. The standard-based off-the-shelf solution BODAS Connect All-in-One Connectivity provides ready-to-use modules which can be adapted to specific requirements quickly and easily. This is only logical. After all, even the basic modules of the complete solution are designed to put in place customized and future-proof telematics services on the basis of prefabricated "off-the-shelf" modules and to improve the competitive position in the long term.
What also needs to be taken into account when it comes to data management? Find out more in our free white paper. Download it now