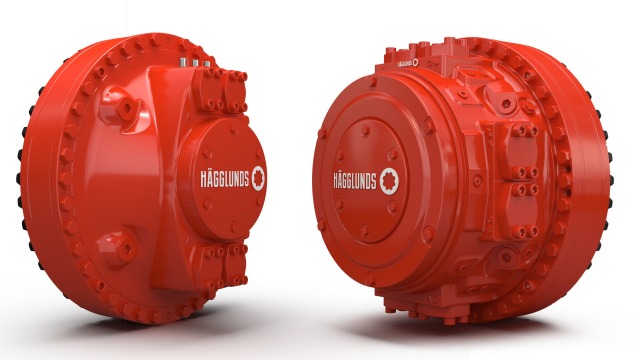
Produkte
ÜbersichtBranchen
ÜbersichtService
ÜbersichtUnternehmen
ÜbersichtKarriere
ÜbersichtSo kaufen Sie
ÜbersichtProduktgruppen
ÜbersichtEngineering
ÜbersichtKonfiguratoren und Tools
ÜbersichtEinstiegsmöglichkeiten
ÜbersichtEDI (Electronic Data Interchange)
Übersicht