
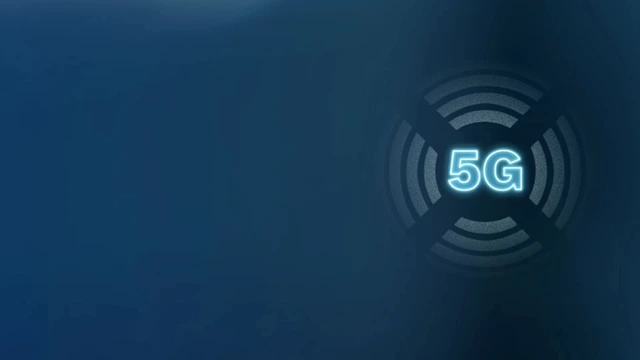
Select your location
Bosch Rexroth around the world
Asia & Pacific
Europe
The arrival of 5G technology marks the beginning of a new era in manufacturing. We look at shop-floor developments, at the future potential – and we also find out why IoT needs 5G.
Everyone these days is accustomed to seeing technology constantly evolving. We see it with operating software, with apps, with mobile devices, and more. Sometimes the change from one version to the next is only incremental, but sometimes it’s more significant.
The advent of 5G technology is firmly in the second category. It represents a huge shift in wireless communications, because for the first time, what is on offer is data rates and levels of reliability that are comparable to those in the wired environment – data rates that are ten times higher than the generation that precedes them.
For 3G and 4G, the focus has been principally on the implications for the world of the consumer – but 5G will extend far beyond this, and into industrial applications. Why? Because at the speeds and reliability levels on offer, the technology will be able to work in real time. What’s more, it will be able to serve higher numbers of subscribers or Internet of Things (IoT) devices than ever before.
When everything can work in real time as before, but this time wirelessly, manufacturing can be much more flexible, much faster, and much more cost-effective. Dr. Gunther May, Director of Technology at Bosch Rexroth, provides a good example.
Gunther May
Director of Technology at Bosch Rexroth
The implications extend far beyond this simple instance. With 5G and industrial IoT, we believe there will no longer be a need for factory production lines to be fixed. Instead, they can be modular, reconfigured at will in line with requirements, which is an essential part of the Factory of the Future. “Production can react to short-term, new orders in small quantities”, says Gunther May. “The processes and the machines on which they run must be flexible, maneuverable and applicable. Cables would only interfere with that. At the same time, you need hard real-time capability – and this is something 5G innovation can now provide.”
Of course, there are already other communication systems in the factory, such as time-sensitive networking (TSN). But they needn’t be mutually exclusive. “We leave it up to customers to decide which technology they want to use”, says Gunther May. “What’s important to us is an interface in the modems to 5G and to TSN.”
However, some options can’t be considered as alternatives. Wi-Fi 6, is a case in point. “It’s not as reliable as 5G technology”, Gunther May states. “Also, Wi-Fi is transmitted on unlicensed bands like 2.4 GHz. This space is earmarked for use by consumer devices as well, such as microwaves, immobilizers and baby phones. By contrast, 5G has its own frequency bands, e.g. 3.5 to 3.7 GHz for public and 3.7 to 3.8 GHz for campus networks in Germany, and every company can secure its own campus license easily and at a reasonable cost.”
Getting started with 5G technology doesn’t need a major investment in new hardware. Earlier mobile radio systems needed armies of technicians and lots of accessories – but with 5G, that's a thing of the past. Companies won’t need a lot of input from telecoms providers either: they’ll be able to organize maintenance and network operations themselves. “There’s no hard dependence”, Gunther May says. “Yes, sometimes it can be helpful to seek support – for example, to set up data rates for critical applications – but it’s not a must.”
At Bosch Rexroth, our approach to 5G is both internal and outward-facing. We use the technology in our own plants, but we also provide products that are themselves 5G-enabled. For example, our autonomous guided vehicle (AGV) ActiveShuttle and our ctrlX AUTOMATION platform will support 5G.
Of course, even here, the version numbers will ultimately change: 5G will one day give way to 6G. But until then, this latest iteration of telecommunications technology has so much to offer. In particular, we’re eagerly anticipating the AGV potential that 5G localization functionality will unleash.
Gunther May
Director of Technology at Bosch Rexroth
The 5G Alliance for Connected Industries and Automation (5G-ACIA) is the globally leading alliance for shaping and driving the development of 5G in the industrial domain. Dr. Andreas Mueller is Head of Communication and Network Technology at Bosch Corporate Research, and General Chair of 5G-ACIA. We asked him about the organization’s role, and about the latest developments in the area as a whole.
The main objective of 5G-ACIA is to ensure that 5G meets the needs of the manufacturing and process industries. Do you think it’s succeeding in achieving that objective?
Industrial IoT has become a key focus area for the entire 5G ecosystem. As such, many features have been specified, which address the specific needs of industrial use cases and applications. This includes support for real-time traffic, ultra-high reliability and low-latency, time-sensitive networking (TSN) and high accuracy positioning. In addition, so-called non-public networks have been enabled, so that factories can be equipped with their own, dedicated 5G networks, which are – at least to some extent – decoupled from the established public networks. This gives factory owners a lot of flexibility and independence in the way they can make use of 5G.
5G-ACIA has played a crucial role by providing a global forum for stakeholders from the ICT and OT industries. A close collaboration between these two groups is necessary in order to unlock the full potential of Industrial 5G, and 5G-ACIA is the place to be for that purpose.
What do you think have been the biggest successes of the Alliance?
In a very short time, we’ve become the leading global organization for driving and shaping Industrial 5G, currently with 81 member organizations from around the world. We also got the status as a ‘3GPP Market Representation Partner’, thus formally representing the interests and views of the manufacturing industry towards 3GPP, where 5G is being standardized. However, we’re not there yet. While we’ve made very good progress, especially with respect to the 5G standard, we now have to make sure that it will also ultimately be a major commercial success. This will remain an important objective in the next year or two.
What have been the biggest challenges?
We had to create an efficient infrastructure for 5G-ACIA from scratch, and assess how we could influence the relevant developments in the best possible way. This had to happen quickly, because technology and especially 5G standardization moves fast.
Can you tell us anything about what will come after 5G?
A rough rule of thumb is that it takes about ten years to come up with a new generation, so 6G is a long way off. Until then, a lot of work still needs to be done on the evolution of 5G technology and its introduction in all the different vertical markets, including manufacturing.
It’s also important to note that 5G isn’t a single standard, but is constantly being enhanced and extended, with new releases coming out roughly every 15-18 months. Many features that will make a major difference to the manufacturing industry, such as ultra-reliable low-latency communication and TSN support, will likely hit the market later this year. I believe this will mark the beginning of a more widespread adoption of 5G in industrial automation.
Could you give us some examples of further developments?
In the long-term, I expect other developments and enhancements will include an even stronger focus on vertical applications and private / non-public networks, the deep integration of artificial intelligence and machine learning – for example, for automating the operation of networks – and the usage of ever higher frequencies beyond 100 GHz. This last development will also make possible other completely new features and functions, such as imaging, material inspection, and RADAR – all of them integrated into a single network.
But this is the future and will be part of 6G. In my view, 5G technology will remain at the center point of real-world implementations for many years to come.