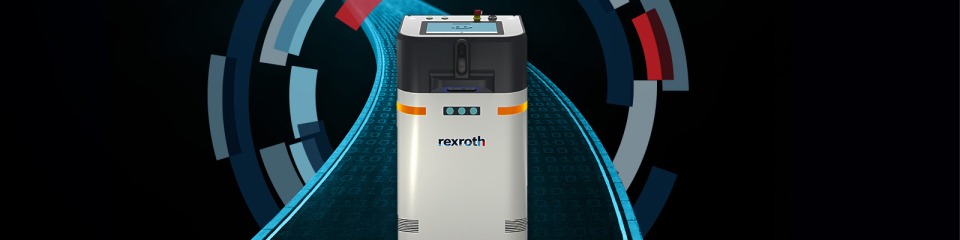
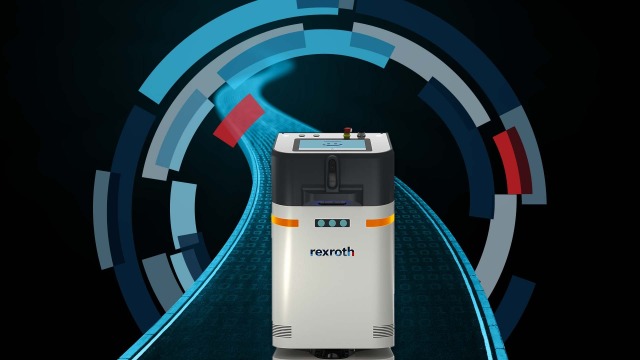
Select your location
Bosch Rexroth around the world
Asia & Pacific
Europe
Autonomous mobile robots (AMRs) tend to have defined paths – but in a broader sense, where are they going? Here, we bring you up to speed with the latest developments in AMR technology and look at what the future might have in store.
If we think of robots, most of us will probably picture a metal humanoid. C-3PO from Star Wars and Optimus Prime, the Transformer, are good examples. In other words, when we think of robots, we tend to think of machines that have arms and legs. Of metal people. But if we think instead of robotics, rather than robots, the picture changes.
With robotics, we’re accustomed to machines of different sizes and shapes, and with moving parts that vary in type, and also in their axes of movement. For instance, a paint-spraying module on an auto assembly line can twist and turn in a way no human arm can replicate. And an automated vacuum cleaner can scurry around under tables so that we don’t have to get down on our hands and knees.
At Bosch Rexroth, we have teams hard at work to take the industrial application of this technology to the next level. This includes the development of ActiveShuttle, our autonomous mobile robot that can, for example, deliver boxed components on demand from a central store to an assembly point on a production line.
We’ve recently enhanced ActiveShuttle in line with feedback from our customers. It now ‘sees’ even more, is interactive, and finds its way around the factory safely and independently. Thanks to camera-based 3D obstacle detection, it avoids obstacles and can even detect objects protruding into its path. The integrated touchscreen allows for individual configuration and quick intervention on site, while the control software enables fleets to be managed easily and flexibly.
The demand for this type of AMR is clearly rising. A recent report by the International Federation of Robotics states that turnover for autonomous mobile robots and delivery robots grew by 11% to over one billion US dollars in 2020.
There are three main evolutionary stages that we foresee for autonomous transport systems. The first of these involves the further development of sensor technology. With digital camera and lidar technology, mobile robotic systems will be better able to see and understand their environment. Parallel developments in other sectors are sure to help in this respect. For instance, the automotive industry is addressing exactly this area on the open road.
The second evolutionary stage is to improve the ability of mobile robotics systems to interpret the information they receive. Previous generations were only able to repeat predetermined patterns, and they had a low level of independence. The improved sensor technology that shop-floor 5G and IoT will enable ought to liberate autonomous mobile robots from these constraints – especially if artificial intelligence is brought to bear. Self-learning systems will be of particular importance, so these mobile robotics systems can respond to changing and new environments.
The third and final stage relates to the reaction to what is perceived. Typically, robotic devices such as AMRs need to learn the environments in which they move, and those environments need to be stable, so the AMRs can follow well-defined paths. But as everyone knows, the factory floor rarely provides this perfectly stable environment. A just-in-time delivery may temporarily be blocking the space between assembly lines; a forklift truck may be busy in a loading area; and a normally open door may be closed in the loading bay.
More communication and better networking are one way that autonomous mobile robots will be able to address such issues. This is where initiatives such as VDA5050, a German automotive and manufacturing industry program, are important. Until recently, manufacturers have been working very independently of each other, and it is only with initiatives such as this that devices from different manufacturers will be able to communicate with each other, and also with a master control system, to tackle such scenarios.
Another key factor is, of course, on-board artificial intelligence. The smarter AMRs are, the better able they will be not just to respond to their environment, but to engage with it. So that roller door is closed, when normally it’s open? Is there any obvious reason why it’s closed right now? No? OK, let’s open it.
We spoke to Philipp Maurer, the Product Manager for ActiveShuttle at Bosch Rexroth, to find out how ActiveShuttle was developed and why it will be such a key part of the Factory of the Future.
When did you realize there was a requirement for this type of AMR and what drove that need?
The idea first came from a Bosch manufacturing plant in Nuremberg. They wanted to automate the transport of small load carriers. Several Bosch plants had the same need, so they joined forces to create a functional model. When Bosch looked into this further – discussed it with customers, investigated special use cases and explored the market – they realized there was a real need for this type of AMR. So, our team at Bosch Rexroth took on the challenge and brought ActiveShuttle to life.
How do you go about this sort of development work? What’s the process or your way of working?
We use the agile product development method, which is a very customer-centered approach – customers are very closely involved throughout the development process. We also partner with other Bosch companies. Being part of the wider Bosch Group gives us a huge advantage because it means we can try out the products in our own factories and make sure they’re just right before we sell them to customers.
How long did it take to develop ActiveShuttle and how many people were involved?
It took three years to develop the first version of ActiveShuttle. We then made some enhancements and the second generation ActiveShuttle is now available. To start with, just a handful of people worked on this development, but the team is growing step by step now.
Were there any big issues or challenges you had to overcome?
Well, this was a new area for us and a new market entry, so we had to grow the team quickly, but having a big new development project like this was also one of the reasons it was so exciting to work on.
Why do you think AMRs like ActiveShuttle are such an important part of the Factory of the Future?
The Factory of the Future is completely flexible and connected – AMRs fit perfectly into this type of environment, delivering goods to the point of need, exactly where and when they’re needed. There’s an increasing demand for multi-variant and small batch production, and ActiveShuttle helps to solve this challenge, making intralogistics processes flexible but without having to change factory infrastructure.
Philipp Maurer