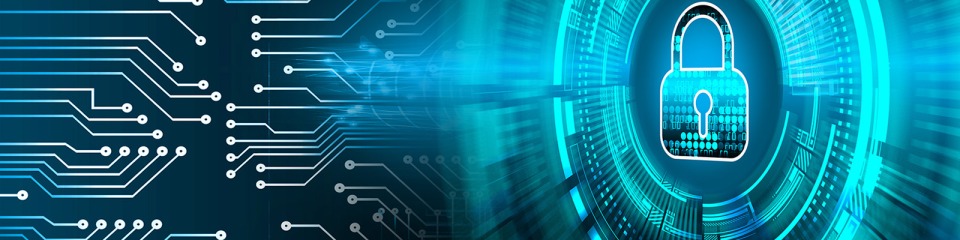
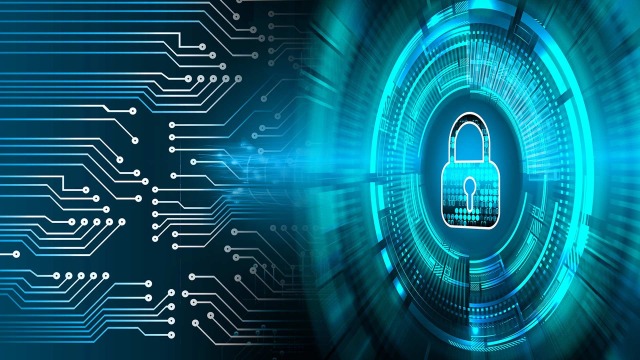
Select your location
Bosch Rexroth around the world
Asia & Pacific
Europe
The Asset Administration Shell (AAS) will help to unlock the power of data within industrial automation. Here we take a look at the prerequisite to realizing data-based manufacturing and explain how it will simplify and speed up processes, reduce time to market, increase overall equipment effectiveness and contribute to sustainability. And we introduce you to the innovative Bosch Rexroth project that exploits the potential of the AAS.
Back in the 1980s and 1990s, if you wanted to install a printer or scanner on a PC, it was a lengthy process. After considering the different interface types, you had to shut down your system, connect a new device and reboot again, load the software and manually install it. Then in 1996, USB – the first multi-vendor serial interface – came along, and the old process became a thing of the past.
But in the world of automation, the laborious installation process has continued to be the reality until recently, with the emergence of the Asset Administration Shell (AAS) for industrial applications to standard IEC 63278. Developed by the German associations VDMA, ZVEI and Bitkom with the help of around 20 companies (including Bosch Rexroth), in many ways it’s the USB port of automation.
This approach unifies communication, services and semantics with industry-neutral standards. As a result, the Asset Administration Shell speeds up the onboarding of new assets, ensures interoperability, creates complete process transparency in real time and contributes to greater sustainability.
Firstly, it’s not a new data silo. It’s a cross-vendor implementation of the digital twin – or digital representation – for all types of devices and components, all in a standardized, uniform language. The Asset Administration Shell consists of:
At Bosch Rexroth, we’ve already equipped 170 million of our products with Asset Administration Shells according to IEC 63278. They’re fully interoperable with assets from other manufacturers.
The Asset Administration Shell simplifies the handling of assets over the entire life cycle. When developing new machine concepts, OEMs can directly integrate the assets of different suppliers into their simulations, as well as compare and commission them virtually. This streamlines and speeds up the process, enabling OEMs to get new solutions to market quicker.
Manufacturers only need one interface in their MES and ERP systems to establish a two-way connection with all assets at field and controller levels. This allows data at all levels to be analyzed, and commands to be issued from all levels. Not only that, but it’s possible to subsequently integrate machines and components that have already been installed. So, the advantages of the Asset Administration Shell come into play in both greenfield and brownfield environments.
The manufacturer of an asset stores the relevant environmental data, in particular the product’s carbon footprint (PCF), in the Asset Administration Shell. This shows the amount of CO₂ generated in the production of that asset. OEMs and end customers can use this data to calculate the PCF of their products, so the environmental impact of products can be compared at a glance.
In the future, the Digital Product Passport in Europe will make it a mandatory requirement to provide the PCF of all products and systems. OEMs will be able to do this by simply adding up the PCF values of all the assets.
The Asset Administration Shell is the prerequisite for seamlessly connecting the field level with corporate IT. Bosch Rexroth’s FACTORY Orchestration Platform (FOP) offers a software solution that’s the missing link between the two. It simplifies the integration and orchestration of entire production lines and factories and consists of four modules: onboarding, workflows, instructions and monitoring.
The FOP is an application that allows the user to orchestrate production processes and machines using the industry standard Asset Administration Shell (AAS). By following the industry standard AAS, new assets can be added very quickly and communication is easy to set up. The application will allow the user to design the production processes based on the low-code Business Process Model Notation 2.0 (BPMN 2.0). This allows the process to be adapted to changes during production by dragging and dropping, reducing changeover and downtime. This workflow management increases the flexibility of production systems.
As most production systems rely heavily on people working close to the machines, information needs to be presented and displayed according to the current situation. To support workers in their daily tasks, the FOP is able to send dynamic worker instructions to any mobile device to guide the worker through the process. It sends specific information to an individual’s device, based on their role, so the right people receive the specific information they need at the right time. Because quick action is required when an error occurs, the FOP also enables processes and their current status to be monitored. If something happens and it is detected by the FOP, a worker can react immediately, which reduces downtime.
New product data and control information can be accessed effortlessly via the Digital Service Assistant (DSA) app. Integrating a new Bosch Rexroth asset is simple, just scan the QR code via the app and close the connection to the target system via scan and connect.
The graphical user interface means that production workers can design workflows without programming expertise, shortening the changeover effort for small and medium-sized series. This significantly reduces changeover times and increases overall equipment effectiveness (OEE).
The Asset Administration Shell creates a barrier-free data flow from the field level to corporate IT. The FACTORY Orchestration Platform gives companies complete process transparency and flexibility. This enables continuous improvements as well as predictive maintenance concepts. The result: higher productivity and less downtime.
As an open standard, the Asset Administration Shell creates the prerequisites for further-reaching, data-based manufacturing developments. Initiatives and programs such as Gaia-X, Catena-X (for the automotive industry) or Manufacturing-X (as a data space for Industry 4.0), only have a chance of realization through the Asset Administration Shell. It’s an absolute necessity for data-based manufacturing and business models of the future.