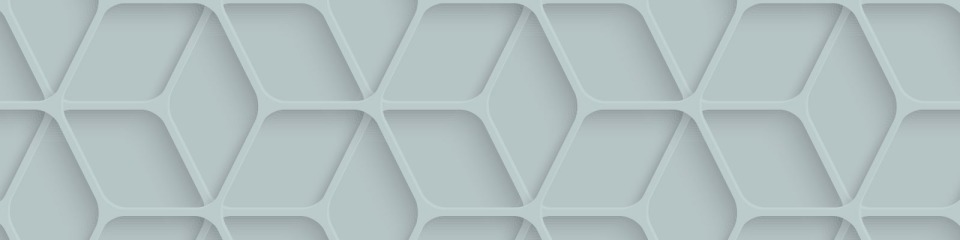

Select your location
Bosch Rexroth around the world
Asia & Pacific
Europe
The Bosch Group is more than the sum of its parts. By combining the knowledge and expertise of different companies and divisions from within the group, innovative solutions are created that push the boundaries of what is possible and help improve our customers’ worlds. A case in point is the production of a new hydraulic component, which Bosch Rexroth and Bosch Manufacturing Solutions came together to create using a hybrid additive manufacturing process. The result? A hydraulic component that’s "impossible to manufacture" can be produced in series.
As a leader in sustainable hydraulics, we at Bosch Rexroth are continuously working to make our drive technology more energy and resource efficient. We recognized that one significant way of doing this is by reducing the amount of oil in hydraulic circuits. In virtual simulations, members of the hydraulics development team identified an opportunity to calm the oil flowing back through the tank by adding an additional component – a diffuser. This simple change could make a significant contribution to the efficiency of smaller hydraulic circuits, so Bosch Rexroth’s designers drew up the design for the additional component based on the simulations.
With the design established, the next phase was to turn the idea into a series product. The manufacturing technology department at our hydraulics plant in Lohr took on the production planning for the new hydraulic component. However, the manufacturing specialists quickly realized that this component wouldn’t be easy to produce. Stefan Hövel, Head of Manufacturing Technology at our hydraulics plant in Lohr, describes the challenge: “One issue was the cost, which we needed to address to make the product affordable for our customers.”
Having decided that the component had to be made of homogeneous stainless steel without welded seams, additive manufacturing became the ideal choice. At Bosch Rexroth, we’ve been using 3D printing machines for years to produce prototypes, spare parts and very small series. But as soon as it comes to series production, 3D printing isn’t yet economically viable industry-wide.
Had the team reached a dead end? “We all saw the added value of the diffuser for our customers and the whole team felt really motivated to break new ground”, Stefan Hövel recalls.
Stefan Hövel
Head of Manufacturing Technology at the Bosch Rexroth hydraulics plant in Lohr
At this point, being part of the wider Bosch Group made all the difference. The Bosch Rexroth team were able to use Bosch’s internal network for additive manufacturing, which ranges from basic research to design to machine construction. The Bosch Manufacturing Solutions team had the in-depth expertise and know-how needed, having successfully handled several additive manufacturing projects, so they were the ideal specialists to bring on board.
Andreas Reifert
The responsible group leader at Bosch Manufacturing Solutions
The team decided the idea was viable, but it could only be realized through a new approach in which everyone contributed their knowledge and experience. The product management team used simulation programs to check the additional function in various forms. On this basis, the designers drafted variants that matched the manufacturing technology and Bosch Manufacturing Solutions with a 3D printing machine at our Lohr plant. All progress was shared amongst the team immediately and step-by-step they got closer and closer to the result they wanted, but it still wasn’t quite enough.
The decisive breakthrough was the decision to use a hybrid solution, whereby we use a standard nut onto which the 3D printing machine prints the functional surfaces.
Despite all the specialist equipment the team have on site, sometimes a simple, practical approach is required. To test the first iteration of the ‘printed’ diffuser, one of the designers took the component home, screwed it into his garden hose and observed how the water flowed into a container without turbulence – just like the simulations had predicted.
The patent-protected hydraulic diffuser went on to pass further, more rigorous tests, and at the same time fulfilled the requirement for a hydraulic component that can be produced economically using additive manufacturing.
Andreas Reifert
The responsible group leader at Bosch Manufacturing Solutions
The next step is about optimizing the process for series start-up. So far, most of the process has been performed manually because the 3D printing machine we’re using has a closed system and only allows certain activities to be done manually. Based on the results of this joint project, Bosch Manufacturing Solutions have started work on an additive manufacturing system that’s tailored to the hybrid process and open to automation.
A core element of this is the use of Bosch Rexroth’s MTX control and drive solution. In addition to its high performance, it offers the possibility of integrating functions tailored to the application independently and of making one's own parameterizations. This enables the software specialists at Bosch Manufacturing Solutions to significantly reduce process times and at the same time achieve the required level of accuracy in a reproducible manner – the prerequisites for economical production.
The first prototypes produced with the hybrid additive manufacturing process are proving themselves with customers and meeting all the expectations of the team. The new hydraulic diffuser makes an important contribution to significantly reducing the amount of oil required in hydraulic circuits. This project has demonstrated once again that the Bosch Group is more than the sum of its parts, it’s a unique reservoir for creating innovative solutions through cross-divisional cooperation.