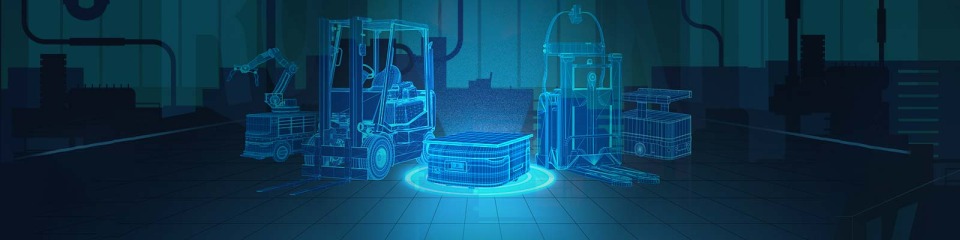
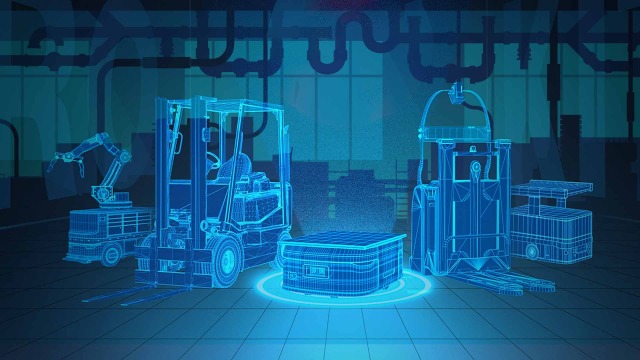
Select your location
Bosch Rexroth around the world
Asia & Pacific
Europe
Demand for autonomous mobile robots and automated guided vehicles is growing, and the market is rapidly evolving. The complexity of building mobile robots puts pressure on manufacturers and system integrators, and time-to-market has become even more critical. Here, we answer some of the common questions asked by AGV and AMR manufacturers and explain how our modular solution set of robotics and automation components simplifies and accelerates the development of mobile robots.
Autonomous mobile robots (AMRs) and automated guided vehicles (AGVs) play an intrinsic role in the factory of the future. They’ve already proved that they can improve efficiency, enable variable batch size production, and work safely and reliably alongside people.
So, it’s no surprise that demand for autonomous mobile robots has increased recently – so much so, that in 2022 mobile robot shipments grew by 53%, and it’s predicted they’ll grow at an annual rate of about 50% between 2022 and 2027. However, the complexity of some solutions can be off-putting to many businesses. In fact, the International Federation of Robotics has included making “robots easier to use” as one of its top trends for 2023.
The mobile robotics market is highly dynamic and driven by innovation. An influx of different autonomous mobile robot solutions and technologies are now available, and established companies are under pressure because new start-ups are coming up with innovative approaches. Timing is all, and time-to-market is a critical element in the development of these solutions.
But building a mobile robot takes time, effort, and knowledge – it’s a challenging process. AMR and AGV manufacturers need to be able to concentrate on their core competencies and focus on developing features that will help to differentiate them in – what has become – a crowded market. What’s more, many solutions are complex and inflexible, so integrating them into existing manufacturing environments can be sophisticated.
There’s a growing need for open, modular, and flexible software and hardware components that do not only enable quick and easy development of mobile robots, but also form a robust and reliable basis for automation. This enables manufacturers and system integrators to build mobile robots that suit their customers’ needs and use cases.
Here, we explain how Bosch Rexroth’s modular solution set can help, and answer some of the questions asked most commonly by manufacturers of mobile robots and system integrators.
What should I look for when selecting components or systems for AMR and AGV automation?
The key to fast, easy automation of autonomous mobile robots and automated guided vehicles is modularity. Both ROKIT – The Robotics Kit, and the automation toolkit ctrlX AUTOMATION, provide modular, flexible solutions that can be quickly and easily integrated into AMRs and AGVs.
ROKIT includes software and hardware components that take care of localization, navigation, and motion of a wide range of vehicle types. ctrlX AUTOMATION surmounts the classic boundaries between machine controls, the IT world and the Internet of Things. With a real-time-capable, Linux-based operating system, consistently open standards, app programming technology, web-based engineering and a comprehensive IoT connection, ctrlX AUTOMATION reduces components and engineering effort by 30 to 50 percent.
Our robotic and automation components simplify and speed up the development, commissioning, and engineering of automated guided vehicle systems. They’re highly integrated and compact, meaning fewer components and less installation space, fewer interfaces and cabling, and less time in development. In fact, with our solution set, we’ve changed the topology of an AGV, making it less complex and more flexible.
How do ROKIT – The Robotics Kit and ctrlX AUTOMATION work together? And how is data exchanged between them?
Our software and hardware solutions are modular, so you can choose components to suit your individual use case and needs. The automation toolkit ctrlX AUTOMATION is based on open standards such as EtherCAT, OPC UA, MQTT or VDA 5050, providing common ground for a wide variety of systems. ROKIT components also give you plenty of flexibility, as they’re compatible with established PCs, operating systems and laser scanners. The control platform ctrlX CORE covers all the tasks that would previously have been distributed across PCs, PLCs and safety controls. Consequently, the ROKIT Locator, ROKIT Navigator and ROKIT Motor can be effortlessly connected to, and controlled via, the ctrlX CORE and its app architecture, supported by the safety solution ctrlX SAFETY.
The 6-in-1 wheel drive module, ROKIT Motor, is tailored to the performance profile of AGVs and AMRs. Its integrated controller enables safe fieldbus communication between the drive unit and the ctrlX SAFETY via EtherCAT. The ctrlX Data Layer ensures rapid, error-free data exchange between process and safety functions.
How much programming knowledge is needed to implement these AMR and AGV components?
Expert knowledge isn’t required to implement our components, due to the engineering tools, as well as the flexibility, openness, and modularity of the components. This significantly reduces time-to-market and enables you to focus on the factors that differentiate you from your competitors.
The ROKIT components are controllable and linkable via an open user interface (API). The graphical user interface aXessor is intuitive and enables rapid engineering, commissioning, operating and servicing of vehicles – all without expert knowledge.
Thanks to ctrlX AUTOMATION's open software architecture with flexible app technology, developers can select the apps they need or use any open-source software. It’s also possible to run self-developed software on the control platform. Furthermore, functions in all common programming languages can be converted into apps, made available via the ctrlX Store and operated on the ctrlX CORE.
How can I implement the safety requirements for AMRs and AGVs?
ctrlX AUTOMATION and the ROKIT Motor cover this. All secure information is exchanged via a Fail Safe over EtherCAT (FSoE) connection. This means you can achieve functional safety in accordance with performance level d with minimal effort. The safety solution ctrlX SAFETY offers the necessary interfaces and modules. In addition to the standard functions, it’s also possible to perform safe arithmetic calculations.
How can plant managers implement autonomous mobile robot solutions quickly and easily, without making expensive changes to their infrastructure?
There’s no need for plant managers to change their factory infrastructure to incorporate AMRs and AGVs. The laser-based localization software – ROKIT Locator – determines the vehicle’s position in real time and automatically produces maps of the surroundings, without the need for any structural changes.
I need a solution to automate my mobile robots that’s flexible enough to be changed and adapted over time. What can you recommend?
As all the components in our solution set can be used independently, they can be exchanged and used in customized constellations or can be integrated step-by-step. For example, if the profile of the ROKIT Motor doesn’t fit, another drive module can be used instead. On the software side, ctrlX CORE is based on app technology, so developers can select from numerous Bosch Rexroth apps, make use of third-party apps or create their own. Even after delivery, updates or additional apps can be installed quickly and easily. The ctrlX Device Portal enables remote management of all the vehicles in a fleet, so that additional vehicles can be easily incorporated, if required. Finally, the ROKIT software gets updated frequently and expanded by new features.